Companies in the manufacturing industry are increasingly using custom investment casting parts to meet their production needs. However, there are various challenges that businesses need help with getting these parts supplied. These include finding reliable suppliers, ensuring quality standards, sourcing raw materials, and dealing with the cost of production.
What is Investment Casting?
Investment Casting (lost-wax casting) is a manufacturing process commonly used in producing metal components that are complex in shape and require precise tolerances. It involves creating a wax pattern of the desired shape, dipping it into a ceramic slurry, drying it, and finally melting out the wax and pouring molten metal into the remaining ceramic mold. The result is a quality cast with superior surface finish and accuracy. Alloys used in investment casting are typically selected for their ability to be melted and poured into a mold and their strength, durability, and affordability.
Commonly used alloys include aluminum alloys, bronze, stainless steel, cobalt-chrome alloy, nickel-based alloys, and tool steels. It is often used where the highest level of precision is required or when a mass production method like die casting would not be economical. This method is used in various aerospace, automotive, medical, and commercial casting industries. The investment casting process is very precise but time-consuming and requires a high level of craftsmanship. This is why investment casting is often used for products that require high accuracy, such as medical implants or aircraft engine parts.
How To Do Investment Casting?
There are many investment casting methods, but the most common method is creating a mold of the desired object. This mold can be made from various materials, but the most common is plaster. Once the mold is created, it is filled with liquid metal, such as bronze or brass. The mold is then placed in a furnace and heated to a high temperature. It causes the metal to melt and flow into the mold. Once the metal has cooled and hardened, the mold is broken away to reveal the newly cast object.






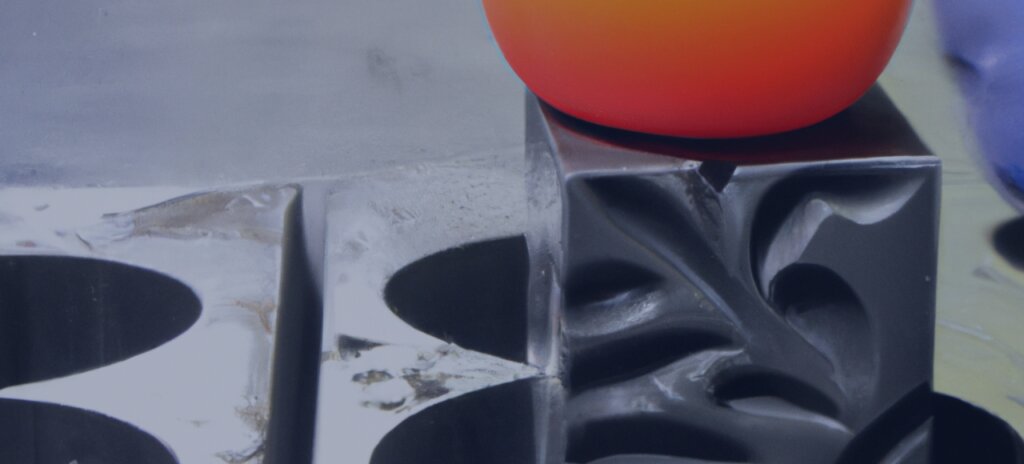
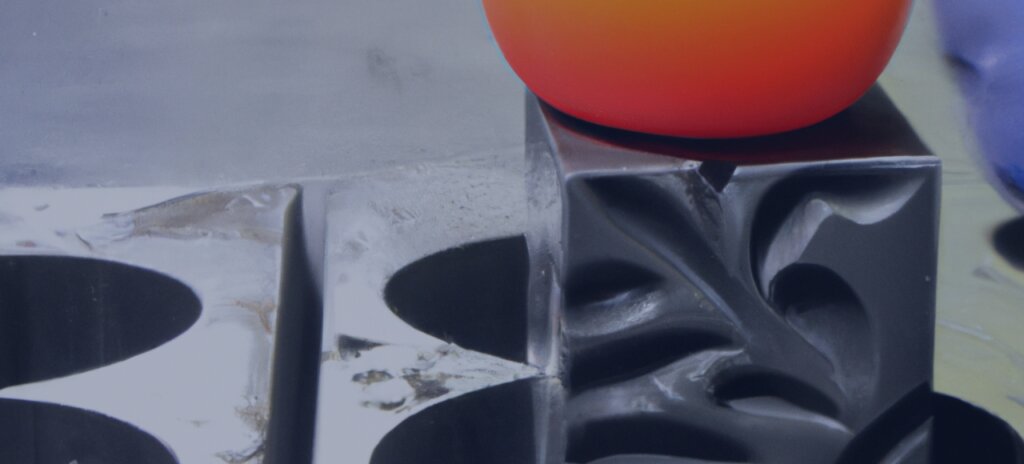
Why to Choose Investment Casting?
Investment casting is an effective and efficient manufacturing process that has gained traction in the industrial sector due to its numerous benefits. This process involves using a molding material such as wax or ceramic to create a negative impression of the desired product, which is then filled with molten metal. The result is a precise and detailed product that requires minimal finishing. Investment casting offers several advantages over other manufacturing methods, including improved surface quality, cost savings, and shorter production cycle times. Additionally, it can manufacture complex shapes with intricate details that are difficult to achieve with other processes. As such, investment casting is becoming increasingly popular among businesses looking for quality products at an affordable cost.
Investment Casting Vs. Die Casting
Die casting and investment casting are commonly used methods to create parts and components from metal. Both investment and die casting have their own advantages, but the most crucial difference between them is the type of mold used to cast the parts. Investment casting uses a wax mold that is then replaced by molten metal. Die casting uses a steel or aluminum die that shapes the parts when molten metal is injected into it. Both processes require high skill, precision, and attention to detail to produce high-quality results. Understanding the differences between these two types of casting is essential before deciding which one would be best suited for your project.






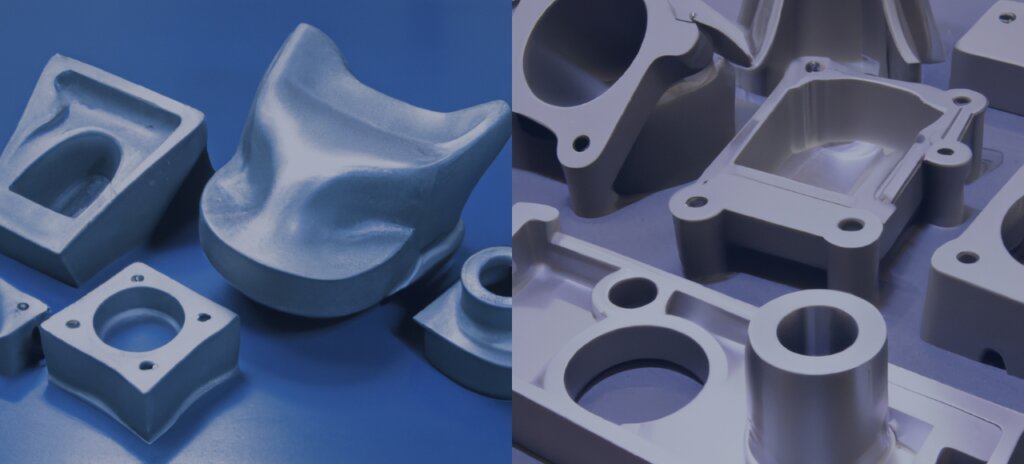
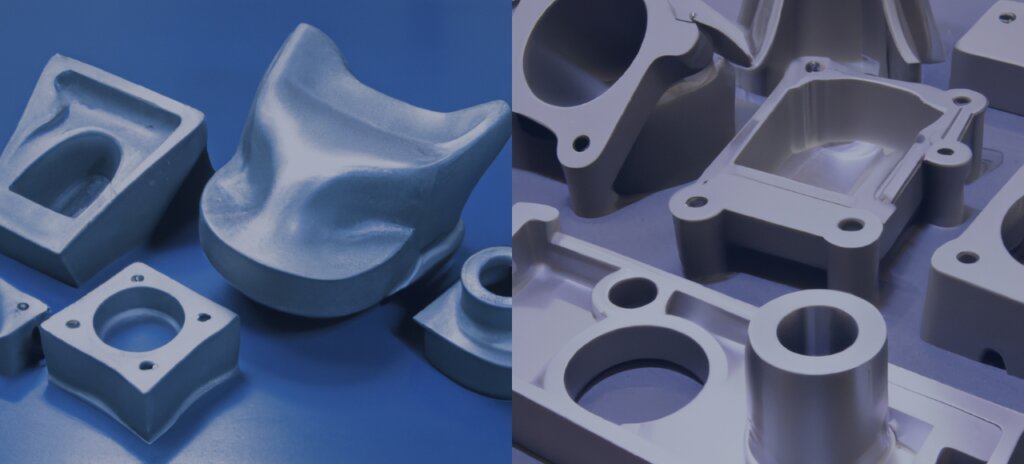
How To Choose The Right Investment Casting Foundry?
Investment casting is one of the oldest and most reliable metalworking processes in manufacturing. When looking for an investment casting foundry to produce your components, choosing a reliable partner who can deliver consistent, high-quality parts is essential. Find the right foundry; there are several factors you should consider, such as experience, quality control procedures, material availability, cost, and delivery times.
- Experience is an essential factor to consider because it indicates that the foundry has a good understanding of the investment casting process and has a track record of producing quality parts.
- Price is also important, as you want to get the best value for your money. Talk to several different foundries and ask for quotes to find the best option for your needs.
- Capacity is another factor to consider, as a foundry that is too small may not be able to meet your production needs, while a foundry that is too large may be more expensive than necessary.
- Quality is also an essential factor, as it will determine the accuracy and surface finish of the parts.
Zetwerk is the best choice for your investment casting needs. We provide a wide range of services, including precision casting and 3D printing, to deliver the highest quality results for your project. Our experienced professionals can help you choose suitable materials, processes, and techniques for your application. We also offer an extensive range of post-casting services like machining, heat treatment, anodizing, and finishing to ensure that your parts are ready for use.





