Investment casting is a manufacturing process that has been used for centuries to create components with complex shapes. Investment casting manufacturers are companies specializing in producing parts via this process. It requires exact and intricate molding to develop parts of the desired shape and size. Investment casting involves preparing a wax pattern, which is then coated with a ceramic material, melted away, and replaced by molten metal. The resulting part is then finished and inspected for quality assurance before being sent to its intended destination. Investment casting manufacturers have become increasingly popular as they offer cost-effective solutions for producing intricate components.
What Are The Alloys Or Materials Used In Investment Casting?
Investment casting creates complex, precision parts from various alloys and materials. Depending on the type of part and its desired properties, investment casting can be done with a range of alloys and materials. This includes aluminum, bronze, brass, stainless steel alloys, tool steel, cobalt-chrome alloys, low alloy steels, nickel alloys, and more. Each alloy or material has unique characteristics that make it suitable for various applications.
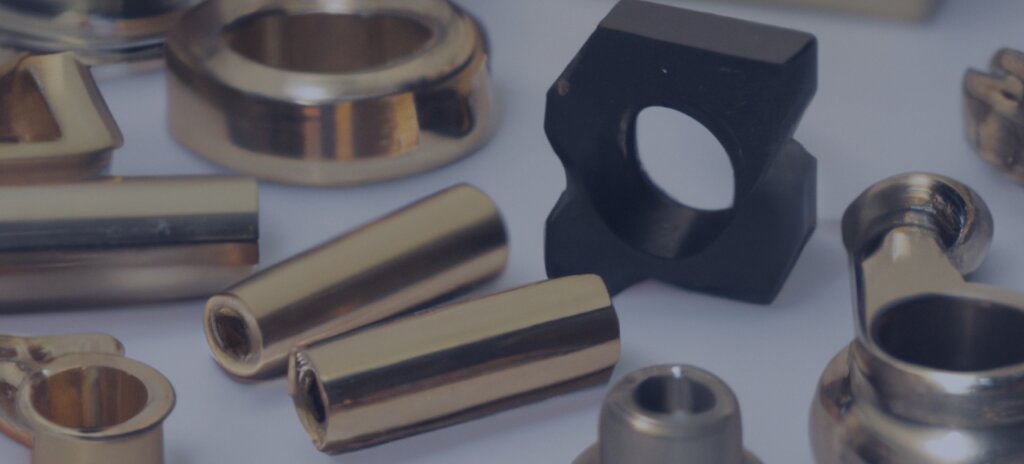
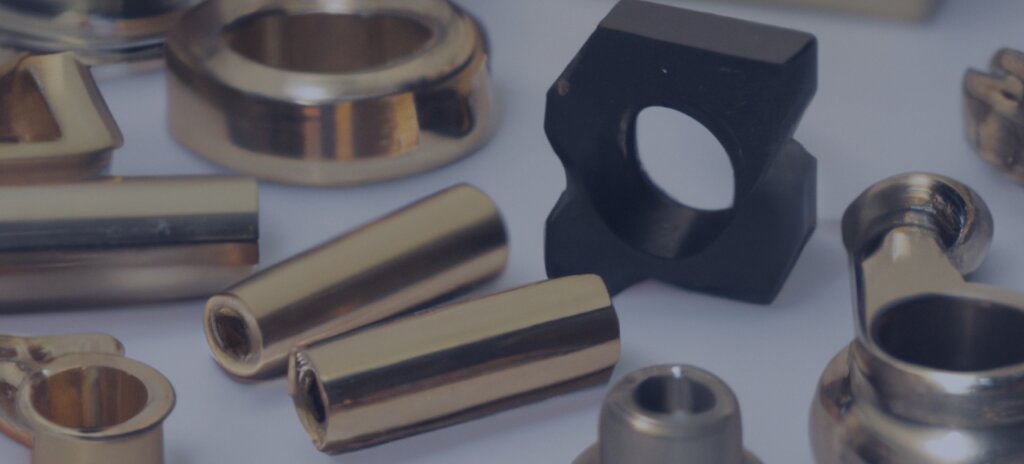
Top 5 Benefits 0f Using Investment Casted Components In The Product
Investment casting, or “lost wax” casting, is a centuries-old process used to produce precision parts. The process involves creating an exact wax replica of the part to be cast and melting it away after the metal is poured. This has many advantages over traditional machining processes, such as low tooling costs, high dimensional accuracy, and smooth surfaces. Investment casted components offer repeatable quality from batch to batch and can provide significant cost savings, higher precision, and greater surface finish accuracy.
- Reduced Costs : Investment casting can create intricate parts that would be difficult or expensive to make by other methods, such as machining or forming. This makes it ideal for producing prototypes and small batches of high-quality parts at low cost. One example is aircraft engine components, which require precise tolerances for proper operation but are too large for most other manufacturing processes.
- High Production Rates : Parts produced using investment casting tend to have less porosity than those made using other methods, making them strong and durable under pressure. This is especially true when it comes to large castings that require high tolerances and dimensional accuracy. The ability to create multiple parts at once at high speeds results in significant savings in terms of time and money for companies using investment castings as part of their manufacturing processes.
- Enhanced Design Flexibility : Investment casting allows manufacturers to create intricate details and complicated shapes in their components. This makes investment casting a good choice for manufacturers who want their products to be durable and visually appealing.
- Improved Surface Finish : Investment casted components can have smoother surfaces than other types of castings because they are made from wax or other materials that are easily removed from the finished product. In addition, these molds can be created with features like draft angles, which are difficult to produce manually; thus giving you a better-looking finished product than if you had used another method, such as sand casting.
- Less Material Waste : Investment casting makes it possible to produce parts with a near-net shape (NNS) or near-net-shaped (NNS) condition. This means very little material is left over after the casting process is completed. With other manufacturing methods, there may be considered waste material that needs to be removed before the part can be used.





Disadvantages Of Investment Casting
Investment casting is a popular manufacturing process used to produce complex parts with intricate details. However, this method also has its own disadvantages.
Some of the main negatives associated with investment casting include high production costs due to the time-intensive nature of the process, difficulties in producing components with thin walls, and a limited selection of metals that can be used. There are also some safety concerns related to the molten metal used in this process that must be considered. By understanding these drawbacks, companies can make an informed decision when selecting an appropriate manufacturing technology for their application.
Investment casting is a cost-effective and efficient process that allows manufacturers to produce complex shapes with high accuracy and repeatability. Partnering with an experienced Investment Casting Manufacturer can provide many benefits to your business, such as improved quality, shorter lead times, better customer service, and reduced material costs. With their help, you can create unique metal parts for your products without compromising quality or increasing production times. Investing in the right Investment Casting Manufacturer is key to ensuring you get the most out of this process for your business.




