The future of investment casting is also bright. Investment casting leads to high performance and lighter parts. Part weight reductions through investment casting technology are used in a wide range of industries ranging from aerospace to consumer products to medical equipment.
It isn’t easy to characterize the company as a purely investment-related entity. Investment casting is always connected to a specific product or final design. Generally, investment casting companies are associated with manufacturers, sellers, distributors, or those who provide investment casting services.
Overview Of Investment Casting
Investment casting process has been used for centuries to create metal objects. The process involves creating a mold of the desired object, then pouring molten metal into the mold. The metal then hardens, and the mold is broken to reveal the final object. Investment casting can be used to create objects of any size or shape and can be used with any metal.
The process is often used to make difficult or impossible objects using other methods, such as objects with intricate detail or delicate features. Investment casting is often used for objects that require high accuracy, such as turbine blades and engine parts. The process is also well suited for objects with complex shapes that would be difficult to create using other casting methods.
There are several benefits to investment casting:
- It is an exact process, allowing for intricate designs and tight tolerances.
- The process is relatively quick and easy, which reduces manufacturing costs.
- Investment casting can be used with various metals, including steel, aluminum, and brass.
Best Materials To Be Used In the Investment Casting Process
Steel, aluminum, and other metals are used to make investment castings. Each material offers strength, flexibility, and formability. Various metal alloys within these groups have different properties.
Carbon Steels : This steel consists mainly of carbon and commonly used steel. It’s the popular choice for investment casting due to its high structural integrity, especially after heat treatment. It is used in electrical appliances and motor parts.
Low Alloy Steels : This steel is used for its strength, hardness, and resistance to factors such as corrosion. This is partly due to nickel and chromium addition. Despite the increased hardness, it can still be welded well with suitable materials. We can see its uses in construction and military vehicles, pumps and valves, and oil & gas components.
Alloy Steels : Alloy steel combines carbon steel and one or more additional elements. For example,
- Adding chromium increases hardness and heat resistance.
- Adding cobalt makes the metal durable and robust.
- Adding nickel improves the strength and hardness of metallic carbon while providing additional corrosion resistance.
- Adding tungsten with carbon steel improves metallic carbon’s heat resistance and hardness.
- Adding vanadium to carbon metals improves various properties such as strength, hardness, and better corrosion resistance.
Austenitic Stainless Steels : This steel’s main crystal structure is non-magnetic iron. This metal does not increase hardness when heated and is completely non-magnetic. The corrosion resistance of this metal makes it extremely popular for hospitality, industrial equipment, and automobiles.
Ferritic Stainless Steels : These metals are rich in chromium, which makes them highly malleable, corrosion-resistance, and cracking. These materials are commonly used in automobiles, kitchen cookware, and offshore machinery.
Precipitation Hardened Stainless Steel : This metal is either semi-austenitic or martensitic, depending on its process step. Various heat treatments characterize this metal with high strength and hardness, especially in weight-to-strength ratio. Its common uses are in springs and aerospace parts.
Nickel Alloys : One of the most important things that make nickel alloys specific is their thermal expansion properties. They are also highly magnetic. A few standard nickel grades are Ni201, Ni205, and Ni200, each with unique benefits based on the part’s type. It is commonly used in the oil & gas industry, wires, and electrical housings.
Cobalt Alloys : Cobalt alloys have excellent heat and corrosion resistance. They are also very durable and usually last a long time. The most common alloys are 3, 6, 21, and 31. They are commonly used in jet engines and orthopedic plants.





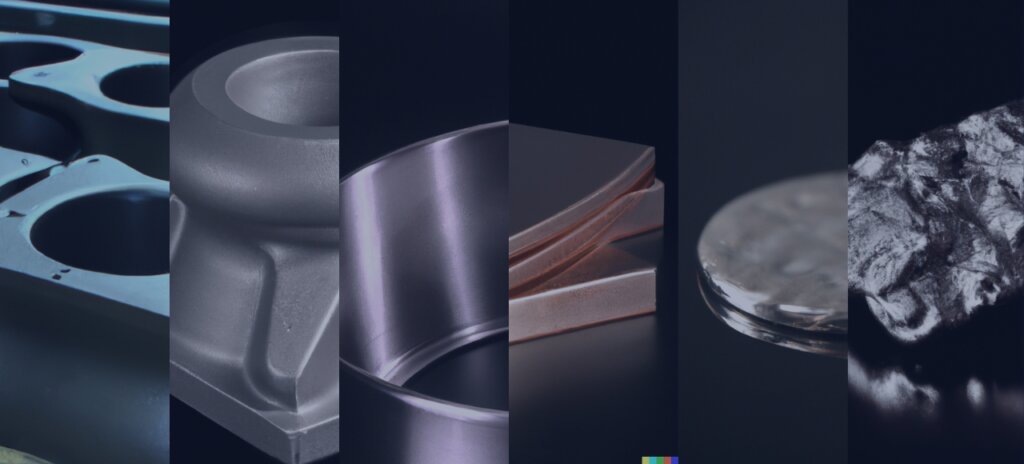
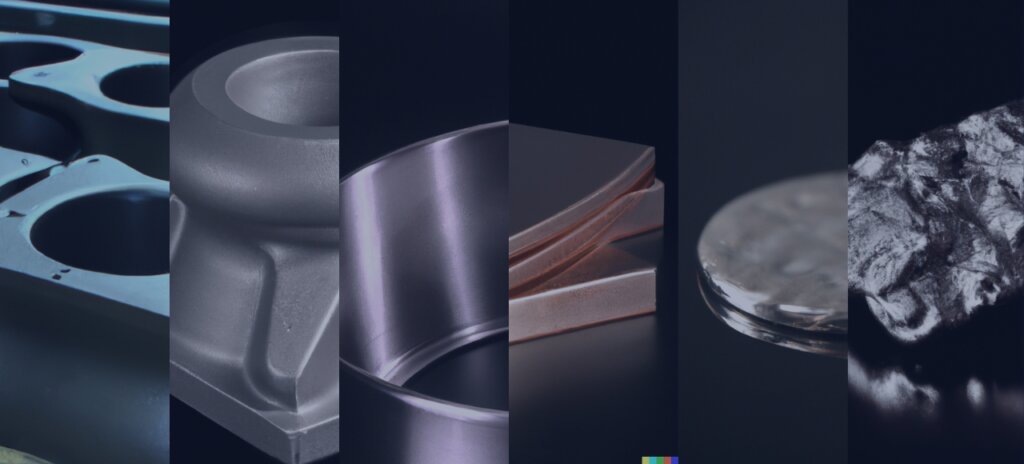
In recent years, investment castings have become a popular choice for many industries. As their popularity continues to grow, so does the need for companies specializing in producing these products. The investment casting industry has grown along with this demand and will continue to do so in the future.
As one of the top 10 casting companies in the USA, Zetwerk knows what customers worldwide want: cost-effective and high-quality products with guaranteed delivery on time. We achieve this by providing our customers with a wide choice of investment castings. Our tooling is designed according to the customer’s requirements, and we can offer short lead times for prototypes. Small and large volume production runs in various materials, including aluminum, copper, iron, steel, tin, and nickel-based metals.




