Precision casting is a type where the mold is made to very tight tolerances. This process is often used for small parts requiring high accuracy, such as gears or car engine parts. The process begins with the creation of a master model or pattern. This pattern is then used to create a mold, usually made of plaster or metal. The molten metal is then poured into the mold and allowed to cool. Once the metal has cooled, the mold is broken away to reveal the finished part.
Using custom precision casting, manufacturers can create custom-designed parts rather than mass-produced or standard parts. The process produces high-quality, intricate parts with great accuracy and surface finish. This method can make parts for various industries, including aerospace, medical, automotive, defense, and industrial.
Investment Casting Vs. Sand Casting
Both processes involve the use of a mold to shape the final product, but there are some critical differences between the two methods
Investment Casting: It involves the creation of a disposable pattern, which is used to create a mold. The mold is then filled with a liquid metal, which is allowed to solidify. The process produces high-quality, accurate parts with a smooth surface finish. However, the process can be more expensive and have longer lead times compared to sand casting.
Sand Casting: Sand casting involves using a sand mold to shape the final product. The mold is created by packing sand around a pattern, which is then removed to leave a cavity in the shape of the final product. The cavity is then filled with molten metal, which is allowed to solidify. Sand casting is more cost-effective than investment casting and is well-suited for producing large quantities of parts. However, the process could be more accurate than investment casting and delivering parts with a rougher surface finish.
Investment casting is typically the better choice for producing high-quality, accurate parts with complex geometries and fine details. In contrast, sand casting is better suited for producing large quantities of parts at a lower cost.
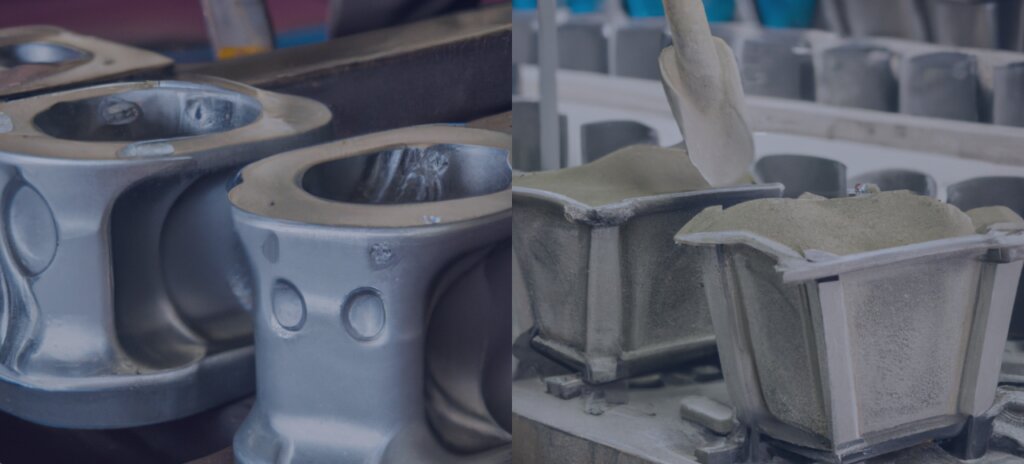
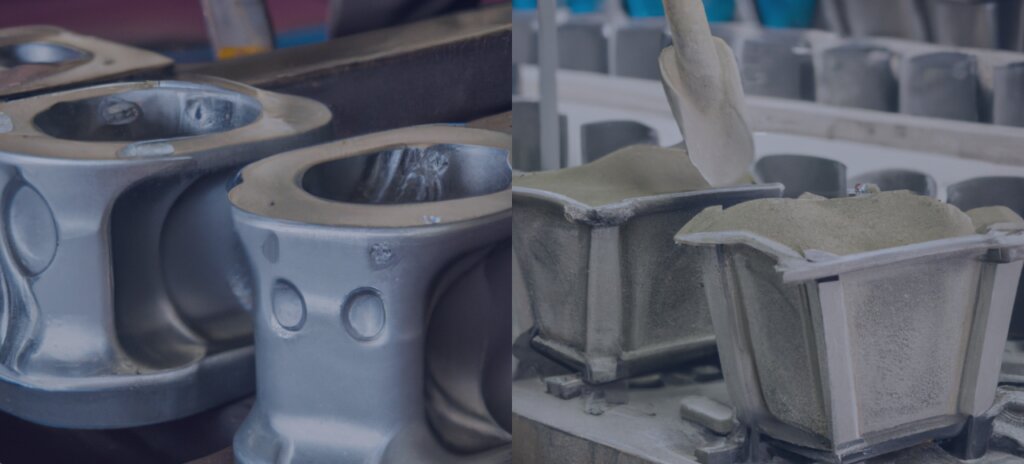
Materials Used In Precision Casting
Precision casting, also known as investment casting, can produce parts from various materials, including metals, alloys, and ceramics.
- Metals commonly used in precision casting include steel, aluminum, bronze, and brass. These materials are chosen for their mechanical properties, such as strength, flexibility, and corrosion resistance.
- Alloys are also commonly used in precision casting. These materials combine two or more base metals to create a material with improved properties. Examples of alloys used in precision casting include stainless steel, which is corrosion-resistance and has a high strength-to-weight ratio, and superalloys, which are materials designed to withstand extreme temperatures and environments.
- Ceramics are also used in precision casting, particularly for applications requiring high strength, wear resistance, and thermal stability. Examples of ceramics used in precision casting include silicon carbide and aluminum oxide.
Precision casting can produce parts from various materials, including metals, alloys, and ceramics. The choice of material depends on the application’s specific requirements, such as the required mechanical properties, corrosion resistance, and temperature resistance.
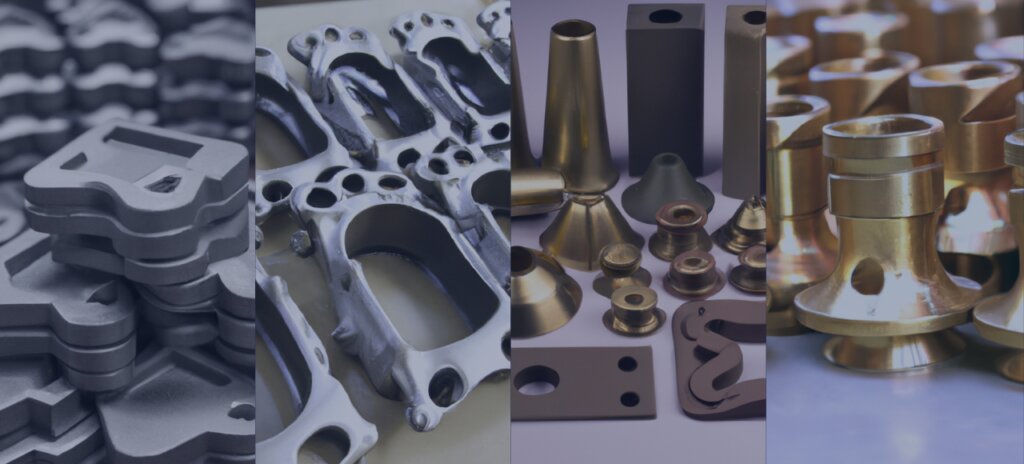
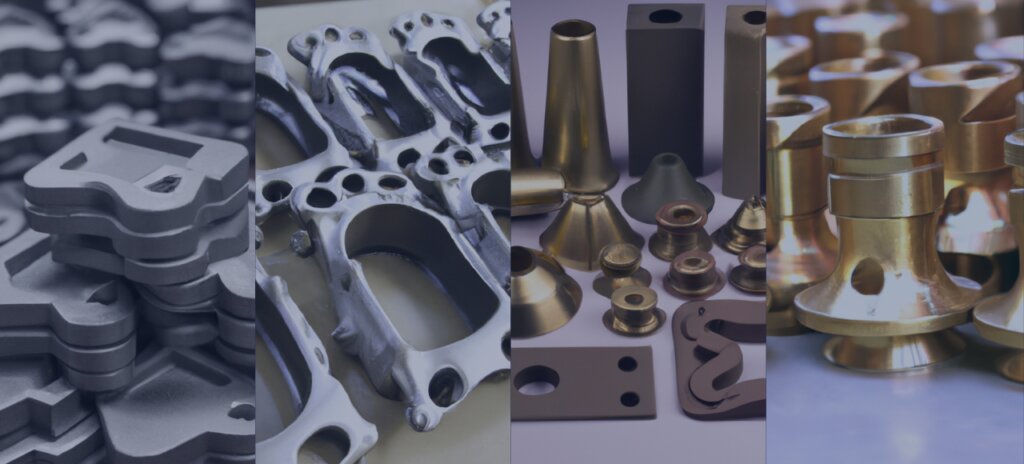
Advantages Of Custom Precision Casting
Precision casting is a manufacturing method that offers many advantages over other casting methods. The most significant benefit is producing parts with very tight tolerances. This is because the mold is made from a precision machined tool. It allows for much greater control over the shape of the final part.
In addition, custom precision casting can produce parts with very complicated shapes. This is possible because the mold can be made with very intricate features. This means that parts that would be difficult or even impossible to produce using other methods can be made using precision casting.
Finally, precision casting can produce parts with a very smooth surface finish. This is because the mold is made from a smooth material, which leaves a very smooth surface on the final part.
Disadvantages Of Custom Precision Casting
There are a few potential disadvantages to using the custom precision casting process:
- High initial cost: The precision casting process can be more expensive than other manufacturing methods due to the cost of creating the disposable pattern and using a refractory material to create the mold.
- Size limitations: The precision casting process needs to be better suited for producing extensive parts, as the mold size is limited by the size of the oven in which it is cured.
- Finishing operations may be required: The precision casting process may produce parts that need additional finishing operations, such as machining, to achieve the desired tolerance and surface finish.
- Long lead times: The precision casting process can have longer lead times than other manufacturing methods, as it involves creating a disposable pattern and curing the refractory material used to create the mold.
- Limited material options: Precision casting is typically limited to casting metals, and the selection of materials that can be used may be more limited compared to other manufacturing methods.





Zetwerk is the leading precision casting company in the United States. We specialize in the production of high-quality, precision-engineered castings for a variety of industries and applications. Our state-of-the-art facilities, experienced engineers, and technicians can produce castings to meet the most exacting standards.




