The Advantages and Challenges of Custom Investment Casting
The manufacturing process of custom investment casting, also known as lost wax casting, has been used for producing delicate and complicated metal components for thousands of years. The procedure begins with the production of a wax mold of the component that is to be replicated, followed by the formation of a shell around the wax mold using refractory material, which is heated to melt the wax and then removed, leaving behind a mold. After that, liquid metal is poured into the mold, and the process is repeated to cool and solidify the metal. This creates a solid metal component with a shape and detail very similar to the original wax mold.
The capacity of bespoke investment casting to generate very accurate and detailed pieces that adhere to close tolerances is one of the most significant advantages of this casting method. The process of wax molding enables precise control over the contours and proportions of the finished object, ensuring that the result precisely conforms to the requirements laid out by the client. In addition, investment casting can be utilized in producing intricate geometries and shapes, which would be highly challenging, if not impossible, to make via conventional manufacturing processes.
The flexibility of custom investment casting is another advantage of this casting method. As a result of the fact that such a diverse selection of materials, aluminum, brass, bronze, iron, stainless steel, and superalloys may be used in the manufacturing process, it is feasible to create components for a wide range of different industries and applications. Because the technique may be used to produce both small and large parts, it is ideally suited to meet the requirements of various manufacturing applications.
The production can also be completed quickly and with little waste when using custom investment casting. It is possible to complete the process more rapidly and at a lesser cost than other manufacturing methods because it does not require considerable machining or any other post-production operations. Additionally, the mold is reusable, which means it may be used to make numerous pieces at once, making it a cost-effective option for high-volume production runs.s
Custom investment casting does not come without any difficulties, despite the fact that it has numerous advantages. One of the most challenging tasks is ensuring that the wax mold is precise and that the finished product conforms to the requirements laid out by the customer. In addition, the procedure can be time-consuming and labor-intensive, necessitating the use of trained personnel and specialized equipment. Additionally, the high temperature involved in the process can represent a risk of contamination; consequently, particular attention must be paid to the selection and preparation of materials and the environment in which the casting will take place.
The manufacturing technique known as custom investment casting is an effective and flexible method that is capable of producing metal components that are complicated, complex, and with tight tolerances. Despite the difficulties involved, investment casting is a fantastic option for satisfying a wide variety of production requirements because of its many benefits, including its adaptability, accuracy, and cost-effectiveness. Custom investment casting is a solution that is dependable and efficient, and it may be used for the production of small or big parts, for a single project, or high volume manufacturing.
Deciding When to Choose Custom Investment Casting for Your Business
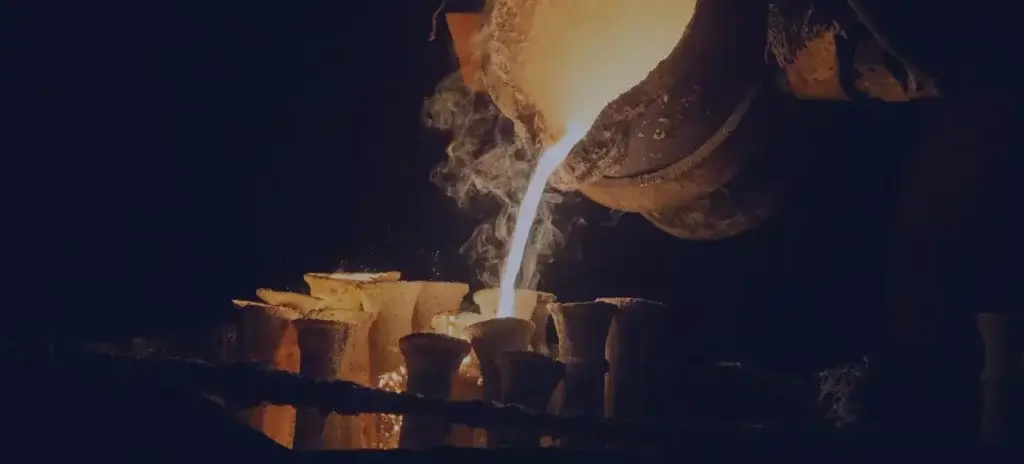
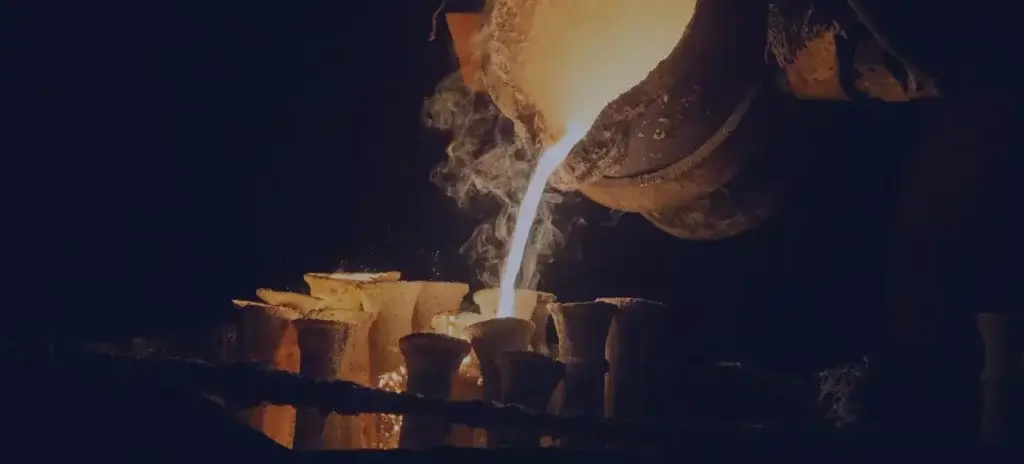
The level of complexity of the component that needs to be cast should be one of the first considerations you make when selecting a custom investment casting method. Investing in casting could be a good choice for your company if it needs parts with complicated contours, precise tolerances, and minute details. Because the procedure permits exact control over the form and dimensions of the finished product, it is ideally suited for producing components with a high degree of complexity.
One more thing you must think about is the material you have to work with. The process of investment casting can be applied to a vast assortment of materials, such as aluminum, brass, bronze, iron, stainless steel, and superalloys, amongst others. Investment casting is an option worth considering if using a specific material or combination of materials is necessary for the operation of your company. Another reason to select investment casting made to order is that it is a more cost-effective process. This method does not call for heavy machining or any other post-production processes, which is one factor that helps keep costs down. In addition, the mold is reusable, so it may be used to produce numerous components simultaneously, which makes it a cost-effective option for high-volume production runs.
It is also essential to consider the number of components your company needs to manufacture. Casting in investment is ideally suited for high-volume production runs, but it is only sometimes the most cost-efficient choice for casting a limited number of individual components. When this occurs, other production methods, like stamping or machining, might be a better and more cost-efficient solution. The robust manufacturing method known as custom investment casting is an option worth considering for companies that need to manufacture high quality and sophisticated metal components. When selecting investment casting for your company, it is vital to evaluate the level of complexity of the part, the type of material required, the cost-effectiveness, and the volume of parts needed. If you are unsure whether investment casting is the best option for your company, consult a manufacturer specializing in the process. This will allow you to discuss your requirements and determine the most suitable choice for your company.
Zetwerk is an industry-leading manufacturing platform that can assist your custom investment casting project in a precise way. Zetwerk offers end-to-end solutions for custom investment casting, including design, prototype, and production, owing to its extensive manufacturing and engineering knowledge. Our facilities and highly qualified crew guarantee the highest quality castings, while our flexible strategy enables rapid turnaround times and cost-effectiveness. As a result of Zetwerk’s dedication to innovation and continuous improvement, the company is continually researching new technologies and techniques to push the limits of what is possible in custom investment casting. Working with Zetwerk can provide your project with world-class manufacturing capabilities and experience, thereby contributing to the project’s success.



