Production and characteristics of upset forging
Upset forging is a metal forging method that includes striking a workpiece with a forging hammer or press to condense it. The procedure is primarily used to manufacture small, high-strength components, such as bolts and screws, from a number of metal alloys, including steel, aluminum, and titanium.
There are various processes involved in the manufacture of upset forging, including forging design, material selection, and forging preparation. During the forging design phase, engineers determine the component’s desired final shape and select the most suitable forging procedure to accomplish that shape. Different alloys have diverse qualities that affect the forging process, making material selection a crucial factor to consider. Forging preparation consists of the following:
- Cutting the workpiece to size.
- Cleaning and pre-heating the material.
- Setting it in the forging machine.
A significant property of upset forging is that it is a very localized process in which the material is only compacted in specific regions of the workpiece. This results in a substantial increase in material density and related strength.
In addition, the localized compression of the material produces a highly homogeneous grain structure, which contributes to the component’s strength. In addition to its precision, upset forging is famous for its ability to produce parts with strict dimensional tolerances and consistent quality.
This makes upset forging excellent for the production of crucial components in industries such as the aerospace and automotive industries. Another critical aspect of upset forging is its capacity to make complex-shaped components. It is feasible to produce parts with intricate geometries and features, such as internal threads and profiles, by combining forging and machining.
Upset forging is a versatile and effective method for creating high-strength, complex-shaped components with great precision. With its capacity to create high-density materials and exact geometries, upset forging is crucial in numerous industrial sectors. It will play a significant role in metal forging and production for many years.
Heating procedure in upset forging
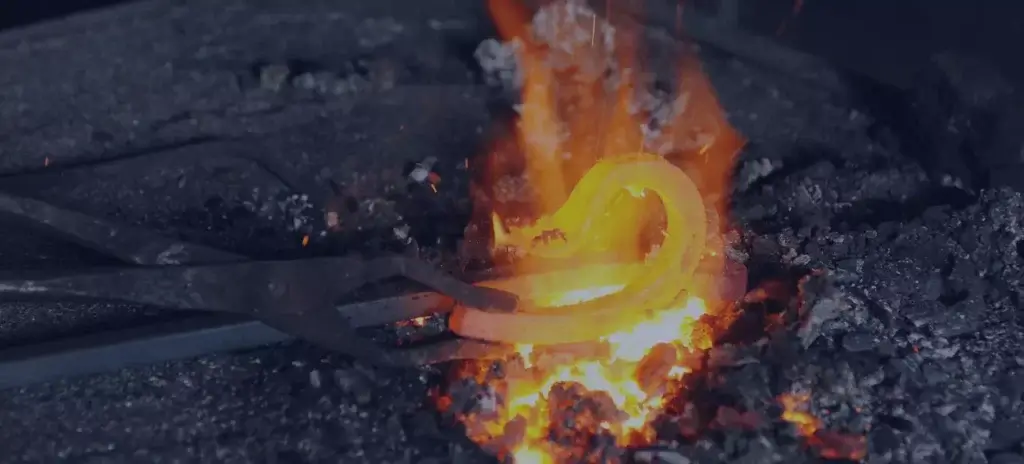
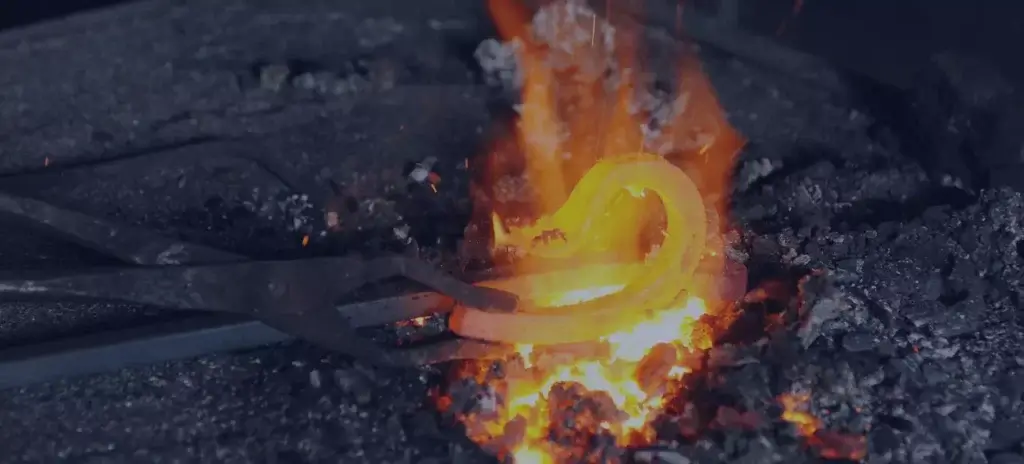
The heating procedure in upset forging is a critical step in the process and affects the final properties of the component. The main objectives of heating in upset forging are to:
- Increase the temperature of the workpiece to a suitable forging temperature
- Ensure uniform heating of the workpiece to avoid thermal gradients and cracking
- Improve the material’s ductility, allowing it to be more easily shaped during the forging process
Generally, the heating operation involves preheating the workpiece in a furnace or oven. However, induction heating may be used in some forging procedures. The workpiece’s temperature is carefully regulated and monitored to ensure it achieves the proper forging temperature.
Depending on the forged alloy, this temperature can range from 800 to 1500°C. After heating, the workpiece is removed from the furnace and transferred to the forging machine. It is critical to begin the forging process immediately after heating to avoid cooling and hardening of the material.
In some circumstances, extra heat treatment may be undertaken after forging to improve the final qualities of the component. In upset forging, the heating technique plays a significant part in achieving the component’s required final qualities. Temperature and heating duration must be precisely controlled to create forgings with homogeneous microstructures and mechanical attributes.
Forging and Finishing Procedure in Upset Forging
The forging and finishing procedures in upset forging are two essential stages in the production of high-quality forgings. The steps involved in these procedures are:
- Forging: The piece of work is positioned in the forging machine and then compressed using the forging hammer or press. The material is compressed and distorted by applying pressure to the required shape. Forging entails repeatedly rotating and striking the workpiece to get a consistent deformation.
- Finishing: If the component’s dimensions aren’t quite what you need, or if the surface polish isn’t suitable, more work may be required after forging. Machining, grinding, and polishing are all examples of this type of work. A component’s final mechanical qualities can be enhanced through heat treatment as part of the finishing process.
In rare instances, extra forging procedures may be done to achieve shapes and geometries with more complexity. This may involve forging the component between dies to produce internal characteristics, like threads or profiles. The specific forging and finishing techniques utilized in upset forging must depend on the component’s specific needs and intended application. In order to manufacture high-quality forgings with consistent mechanical qualities and accurate dimensions, it is necessary to manage these processes as well as the material selection and heating.





Benefits of Upset Forging
Upset forging offers several benefits over other metal forging processes and other manufacturing methods, including
- High Strength: High material density and a homogeneous grain structure are produced by the compressive stresses used during upset forging, resulting in higher strength and enhanced fatigue resistance.
- Precision: The precision of upset forging enables the production of components with tight dimensional tolerances and consistent quality, making it ideal for critical applications in industries such as aerospace and automotive manufacturing.
- Complex Shapes: Upset forging can produce complex shapes and geometries through a combination of forging and machining.
- Efficient Production: The high-volume production capabilities of upset forging make it an efficient and cost-effective process for producing small components in large quantities.
- Reduced Waste: The localized deformation of the material during upset forging minimizes the amount of material waste compared to other forging processes and results in improved material utilization.
Upset forging offers a range of benefits over other metal forging processes and manufacturing methods. Its ability to produce high-strength, precise components with complex shapes and improved surface finishes makes it a valuable process for many industrial applications. Zetwerk specializes in customized solutions for various industries. When it comes to upset forging, Zetwerk stands out by offering bespoke services that meet individual industry needs. Zetwerk’s expertise in this area ensures high-quality results for custom projects. We can produce forged components that meet our customers’ specifications by leveraging the latest technology and best-in-class equipment. This means that whether you’re in the automotive, aerospace, or construction industry, Zetwerk can provide custom upset forging solutions to help you achieve your unique project goals.




