Precision forging factories are companies that specialize in the production of precision-forged parts. These companies typically have a range of specialized equipment and trained personnel and can produce complex and precise shapes using the precision forging process Precision forging manufacturers can supply the forged components to various industries, including aerospace, defense, automotive, and medical devices. They work with multiple materials, including aluminum, steel, and titanium, and produce various parts and components for numerous applications. Precision forgings factory works directly with end-users or serves as suppliers to other manufacturers. They also provide design and engineering services to help customers develop and optimize their parts for production.
Zetwerk provides high-quality Precision Forging Components and all secondary operations.
Submit the relevant part drawings, 3D files, and other information by clicking on the button below.






Precision Forgings Factory – Why Do Businesses Need To Approach Them?
Precision forging is a manufacturing process that involves shaping metal using high pressure and temperature. It is an exact and accurate way to create complex shapes and parts. It is often used for critical components in the automotive, aerospace, and defense industries. Businesses may approach a precision forgings factory for a variety of reasons, including:
- To produce high-quality, precision parts : Precision forging allows for the creation of parts with tight tolerances and high dimensional accuracy. This can be important for businesses requiring precise and reliable product components.
- To reduce costs: Precision forging can often be more cost-effective than other manufacturing methods, especially for high-volume production runs.
- To access specialized equipment and expertise: Precision forging factories typically have a range of technical equipment and trained personnel, making them well-suited to handle complex and specialized forging projects.
- To improve product performance: The high-quality and precise nature of precision forged parts can improve the finished product’s performance and reliability.
Overall, businesses approach a precision forgings factory to access this manufacturing process benefits and produce high-quality parts for their products.
Precision Forging
Precision forging can also be called net or near-net forging. It’s a more advanced forging technique than traditional die forging. Precision forgings don’t require further processing after machining, making them more accessible and faster to produce. Precision forging is seen as an approach to blacksmithing rather than an actual forging process. It is not a separate forging process. After precision forging, the material is ready before being shipped to its final destination.
Precision forging was developed to reduce the waste and cost of post-forging operations. Precision forging uses less material than conventional forging, resulting in less waste and less energy use. Precision forging requires much less machining than traditional forging, reducing production costs. Because precision forging requires little deformation, it results in fewer defects than is the case with conventional forging (1° to 0°).
How Precision Forging Differs From Conventional Forging Method
Conventional forging technology (closed die forging technology) differs significantly from precision forging technology in many respects. Some of them are;
- Although closed die forging often has a delicate surface finish, further machining may be required to produce a finer finish. This contrasts precision forging, which requires little or no machining.
- The final product of precision forging is almost in its final shape, unlike conventional forging techniques that do not.
- Precision forging is cheaper compared to closed-die forging.
- Precision forging requires less than one draft (1° to 0°) as opposed to closed die forging, which requires at least a 3° draft for aluminum and at least 5° to 7° for steel.






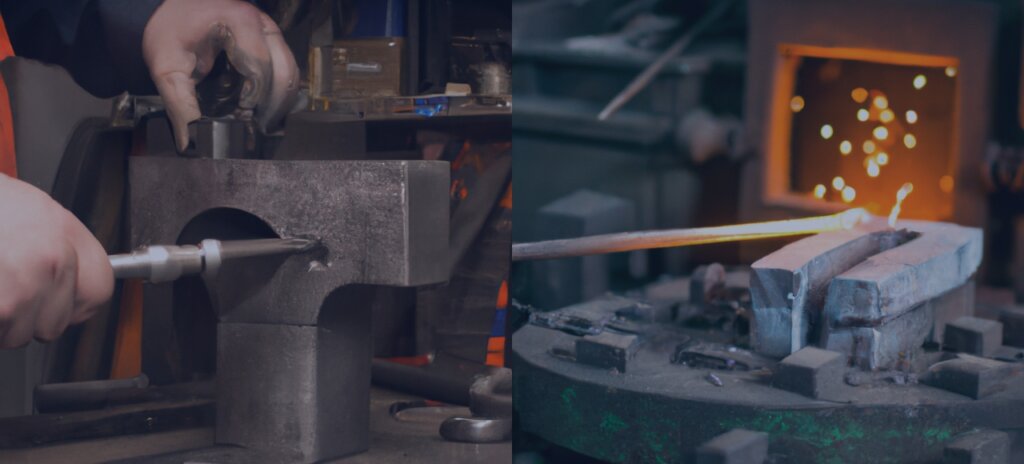
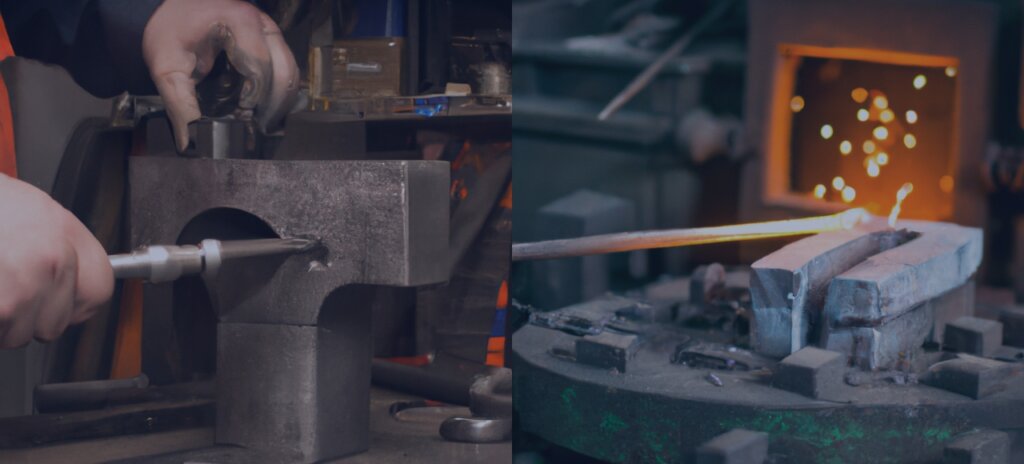
Advantages Of Precision Forging
- High Material Utilization : Metal can be formed into the desired shape and size after plastic deformation, especially with no glue. Parts can be forged directly into their final form or processed further after forging.
- Complex Shapes & Sizes Available : Precision forging is more versatile than cold die-forging because it allows for the production of complex shapes.






- Accuracy : Precision forging produces materials with close tolerances or near-net shapes. Precision-forged parts are made with great accuracy. They are so precise that they are interchangeable with most manufactured parts.
- Temperature : Forging at high precision doesn’t require high temperatures. This is unlike conventional forging processes, which usually require high temperatures.
- Better Work Performance : The process of precision forging often results in a better product, as there are no flash edges, which cause leaks. This leads to a higher resistance to fatigue and corrosion. The metal fiber is evenly distributed and dense, forming a shaped part.
Disadvantages Of Precision Forging
Precision forging has its drawbacks, including the high cost of the equipment. However, precision forging is used when a company is sure that it will save money in the long run.
Ultimately, forging offers superior quality, performance, and precision over any other manufacturing process option. From aerospace components and engine parts to medical instruments, from automotive components and even kitchenware, you can be assured that only through precision forging can the customer truly gain the best results. Precision forgings play a crucial role in industries.





