The metal forging industry comprises companies that manufacture metal products by forging metal into the desired shape. This can include a wide range of products, such as automotive forged parts, construction materials, and tools. The metal forging industry is a significant part of the manufacturing sector and is crucial in many industries, including transportation, construction, and energy. Metal forging is a traditional manufacturing process that has been used for centuries and is still an essential part of modern manufacturing. Many metal forging companies use advanced technology and equipment to improve efficiency and increase production capacity.
Zetwerk provides high-quality Metal Forging Components and all secondary operations.
Submit the relevant part drawings, 3D files, and other information by clicking on the button below.





What is Metal Forging?
Metal forging shapes metal by pressing, hammering, or rolling it into the desired shape. The process is typically performed on hot metal, which makes it more malleable and easier to work with. Forging can be done by hand or machine, and it is often used to create parts for machines, tools, and other objects that are subject to high-stress levels or wear. Forging is a robust and durable way to shape metal, and it is often used to create parts that need to withstand a lot of force or wear
How Does Forging Strengthen Metal?
Forging strengthens metal in several ways. Metal forging is a highly effective manufacturing method for producing strong parts. Small cracks are sealed, and cavities are closed by heating and hammering the metal.
Hot forging breaks down any impurities and spreads them throughout the part, making inclusions less likely to occur. Inclusions are materials such as carbon and silicon mixed with the steel during manufacture and cause stress points in the finished product. Impurities must be removed during the initial casting process, making the metal purer.
Another way it does this is by aligning the grain structure of the metal in the direction of the applied forces. When the metal is forged, the grains stretch and orient toward the applied pressure. It makes the metal more robust and more resistant to failure in that direction.
The Standard Forging Equipments
Upsetters, hammers, ring rollers, and presses are all types of equipment that are commonly used in the forging process.
- An upsetter is a machine used to forge metal by applying pressure to the end of a workpiece, causing it to lengthen and thin out. Upsetters often create parts with a smaller cross-section than the original workpiece, such as bolts or nails.
- Ring rollers are used to create rings or other circular shapes from metal. They work by rolling the metal between a pair of rollers, which shapes it into the desired shape.





- Presses are also commonly used in forging. They apply pressure to the metal to shape it into the desired form. Several types of forged presses are used in forging, including mechanical presses, hydraulic presses, and pneumatic presses.
- Hammers are another forging equipment used to shape metal by repeatedly striking it with a heavy hammer. Various hammers are used in forging, including trip hammers, power hammers, and steam hammers.
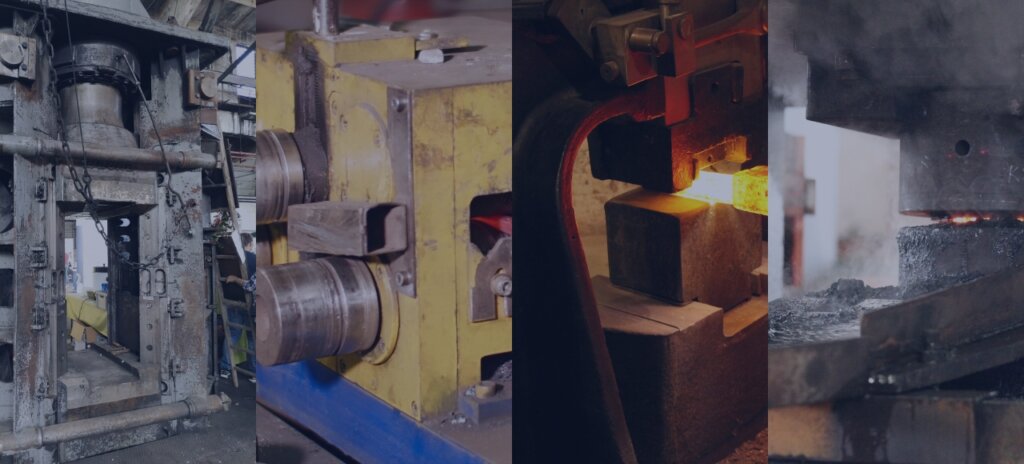
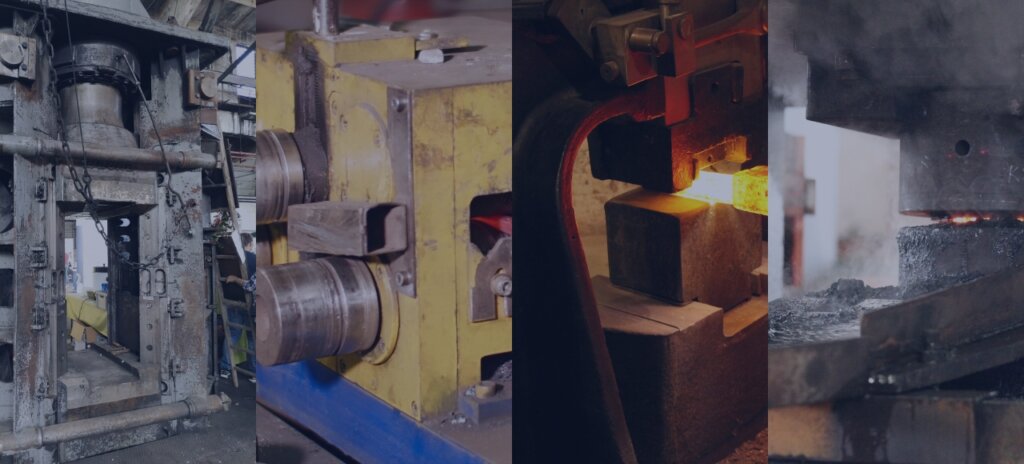
What is the Best Metal for Forging?
Many different metals can be used for forging, and the best metal for a particular application depends on the specific requirements of the part or product. Some most commonly used forged metals include steel, aluminum, brass, and copper.
- Steel is a strong and durable metal that is often used for forging. It is resistant to wear and can withstand high-stress levels, making it a good choice for parts subject to heavy loads or high levels of wear. There are many different steel types, each with specific properties and characteristics, so choosing the suitable steel for the intended application is vital.
- Aluminum is another commonly forged metal. It is lightweight and has good corrosion resistance, making it a good choice for parts used in outdoor or corrosive environments. It is also easier to work with than some other metals, making it a popular choice for parts that require complex shapes or fine details.
- Brass and copper are also commonly used for forging. These metals are relatively soft, easy to work with, and have good corrosion resistance. They are often used for decorative or ornamental applications, as well as for electrical components and other parts that require good conductivity.
Ultimately, the best metal for forging will depend on the specific requirements of the part or product being made, the intended use, and the environment in which it will be used.
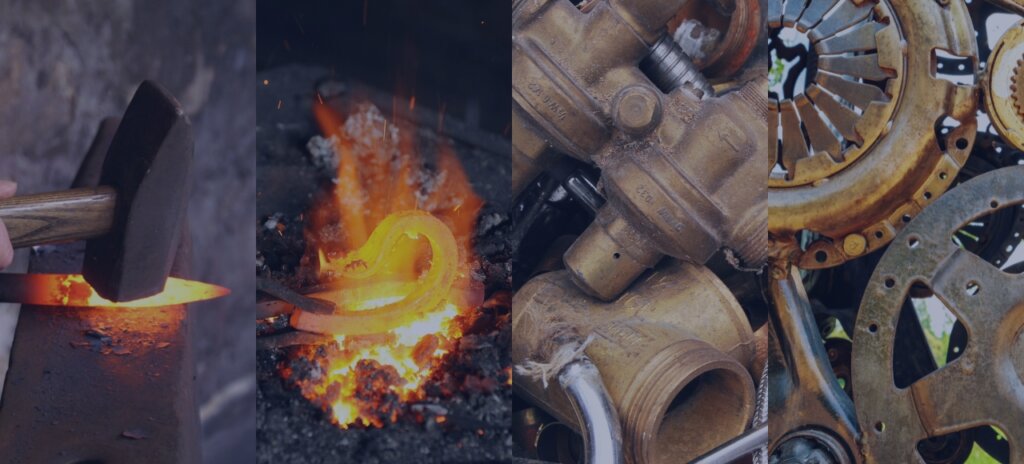
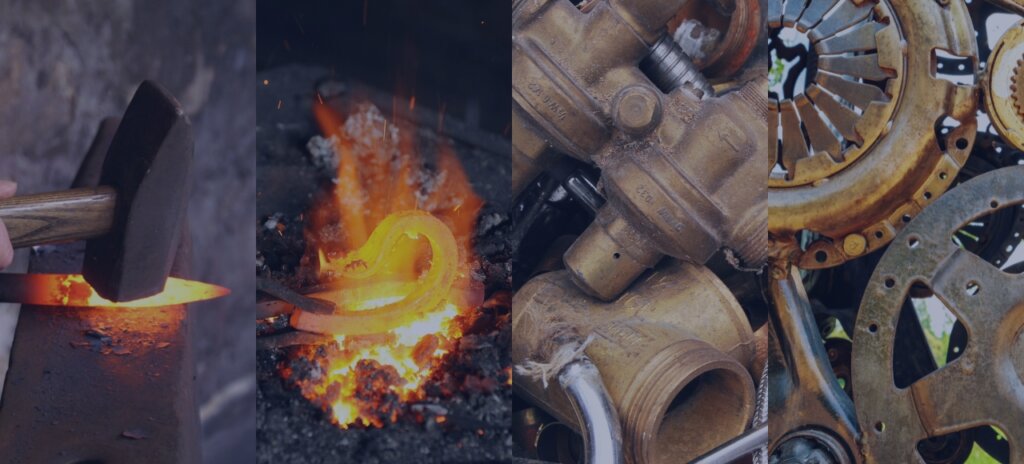
Finding a reliable company to do the job right can be a challenge, especially when it comes to finding reputable metal forging industries. Zetwerk, as an experienced partner for manufacturing custom metal parts, we will work with you every step of the way to ensure that your needs are met.




