The pivot role of an aluminum forging company in business success depends on the specific goals and strategies of the company. Some possible ways include:
- Providing high-quality, reliable products: A company that consistently produces top-quality, dedicated aluminum forgings can establish a reputation for excellence, leading to increased customer loyalty and repeat business.
- Offering a wide range of products: A company that provides a diverse range of aluminum forgings can meet the needs of various customers and industries, potentially increasing its customer base and revenue.
- Innovating and staying up-to-date: A company that stays up-to-date on the latest technologies and techniques in aluminum forging can differentiate itself from competitors and offer more advanced products to customers.
- Building strong relationships with customers and partners: A company that makes strong relationships with customers and partners can foster long-term collaborations and partnerships that can lead to increased business opportunities.
- Maintaining a strong focus on efficiency and cost-effectiveness: A company that can produce high-quality aluminum forgings efficiently and cost-effectively can be more competitive in the market and potentially increase profits.
Zetwerk provides high-quality Aluminum Forging Components and all secondary operations.
Submit the relevant part drawings, 3D files, and other information by clicking on the button below.





Who Needs Aluminum Forging?
Aluminum forging manufacturing process is used to create complex shapes and parts from aluminum alloy. It is commonly used in aerospace & defense, automotive, industrial, and consumer products. For example, aluminum forging makes airplane parts, automotive wheels, engine components, and military equipment. It is also used to make consumer products such as furniture, appliances, and sporting goods. Generally, any industry that requires strong, lightweight components made from aluminum may use forging as a manufacturing process.
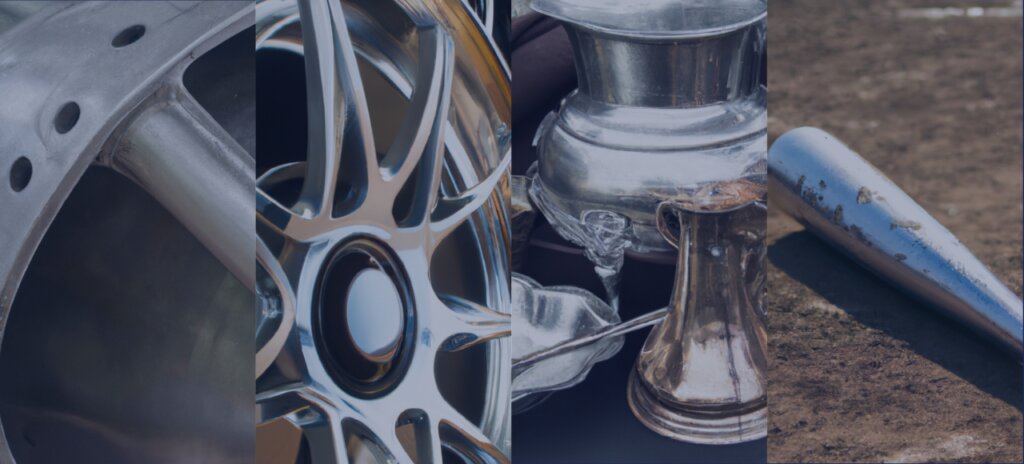
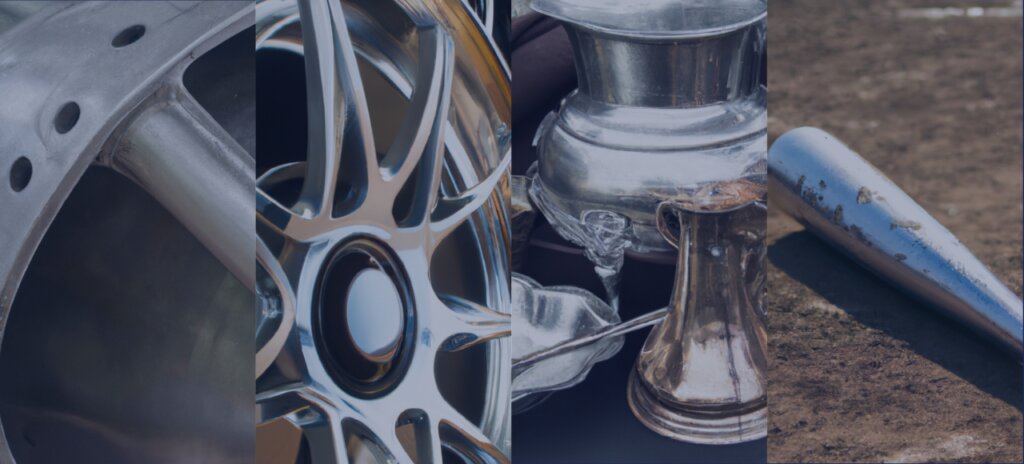
Can Forging Aluminum Make it Stronger?
In some cases, yes. Forging manufacturing process involves heating metal to a high temperature and then using pressure to force it into the desired shape. This can increase the metal’s strength and toughness. The process of forging aluminum can realign the metal’s grain structure, which can make it stronger and more rigid. However, the amount of forging increases strength and toughness depending on various factors:
- The specific aluminum alloy being used
- The type of forging process
- The final shape and size of the forged product
Physical Properties of Aluminum Forging
Aluminum alloys that are commonly used in forging have many beneficial physical properties. These properties make aluminum popular for various applications. Some of the physical properties of aluminum forging include the following:
- Lightweight : Aluminum is about one-third steel’s weight, making it an attractive choice for applications where weight is a concern, such as in the aerospace and automotive industries.
- Electrically conductive: Aluminum is a good conductor of electricity, which makes it useful in electrical applications.
- Strong: Despite its lightweight nature, aluminum alloys used in forging can be solid. They can be strengthened through various methods, including heat treatment, cold working, and alloying with other elements.





- Ductile: Aluminum alloys used in forging are flexible, which means they can be deformed without breaking. This makes them well-suited for creating complex shapes through the forging process.
- Corrosion resistance: Aluminum is naturally resistant to corrosion, making it suitable for various environments.
- Thermal conductive: Aluminum is a good conductor of heat, which makes it useful in applications where heat transfer is essential.
- Recyclable: Aluminum is 100% recyclable, making it environmentally friendly.
Why is Forging Preferred over Casting?
Forging is a process in which metal is shaped by pressing, hammering, or rolling it into the desired shape using a hammer or press. It is generally considered to be superior to casting for several reasons:
- Forging produces more robust and durable products. Because the metal is shaped by being subjected to high levels of force, the grains of the metal are aligned, and the structure of the metal becomes dense, resulting the final product.
- Forging can produce parts with more complex shapes. Because the metal can be shaped using various tools, forging can make parts with different shapes and sizes, including those with complex geometries that would be difficult or impossible to produce through casting.
- Forging can be more cost-effective. While the initial cost of the equipment needed to perform forging may be higher than that required for casting, the cost per part may be lower due to the increased efficiency and productivity of the forging process.
- Forging can be more precise. Because the metal is shaped using tools, it is possible to achieve high precision and accuracy in the finished product.
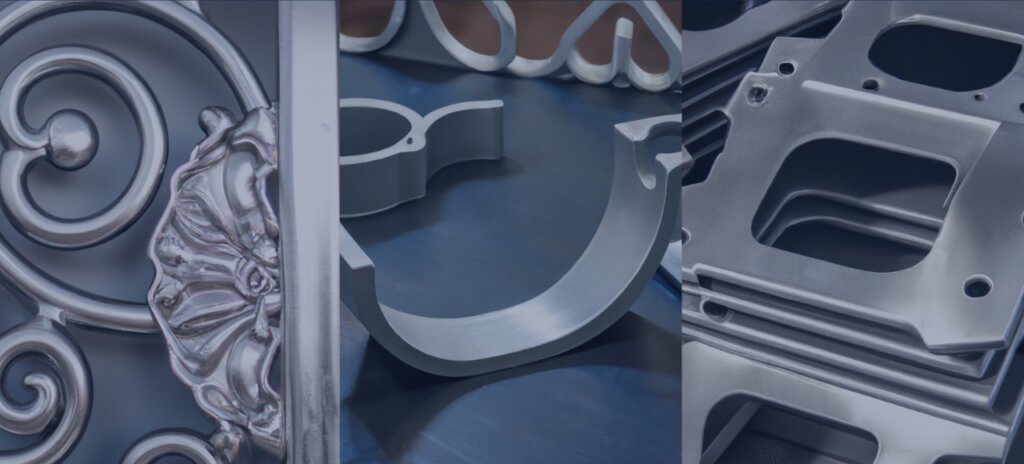
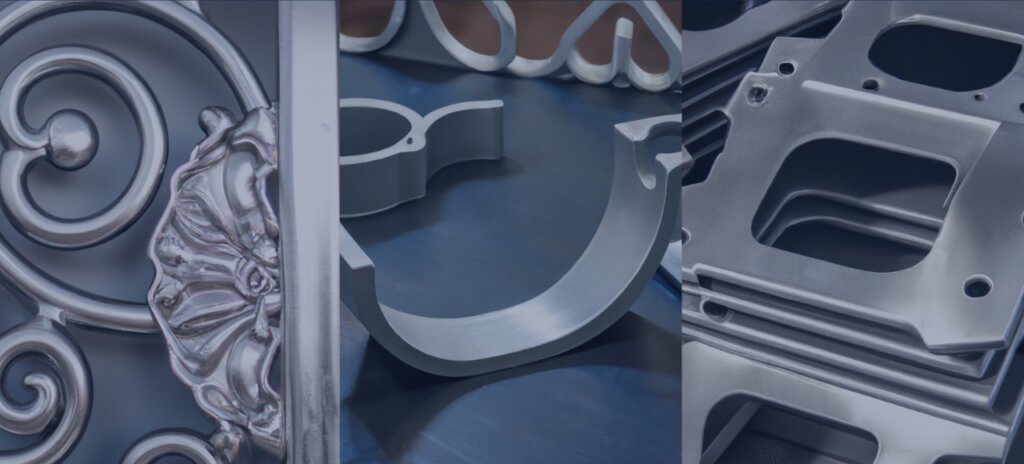
Overall, forging is preferred over casting because it produces more vital, more durable products with complex shapes that are highly precise and can be cost-effective to produce. If you’re looking for high-quality aluminum forged parts, check out Zetwerk – a leading Aluminum Forge Company USA.




