The zinc die casting process uses molten zinc to produce high-precision metal parts. This technique has become increasingly popular in recent years due to its numerous benefits, including low cost and ease of production. Zinc die casting is used in a variety of industries, from automotive and electronics to consumer goods and mechanical sectors. In this article, we’ll look at the zinc die casting process, benefits, and some of the most common zinc die casting products used in industries.
The Future of Manufacturing: The Rise of Zinc Die Cast Products
The future of manufacturing is always changing, and zinc die casting is becoming an increasingly popular option for a variety of industries. This method of manufacturing has shown itself to be cost-effective, efficient, and versatile–making it an attractive option for many businesses looking to get their products made quickly and efficiently. Zinc die casting is known for its ability to produce large quantities of high-quality, precise parts. This makes it ideal for use in the automotive industry, where mass production is crucial.
Zinc die casting is also used to make a wide range of consumer goods, from electronics and home appliances. This casting method is a fast and automated process that can produce large quantities of parts in a short amount of time. The quick turnaround time of this method is not only cost-effective, but also ensures consistent quality across all parts produced.
The increasing demand for environmentally friendly manufacturing techniques is driving the growth of zinc die casting. Compared to other manufacturing techniques, zinc die casting produces minimal waste and uses less energy, making it a more sustainable option for the future.
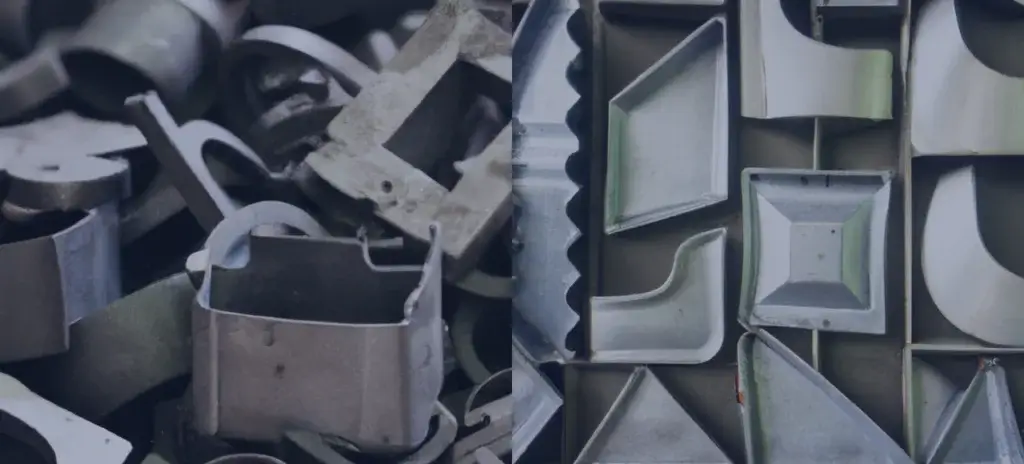
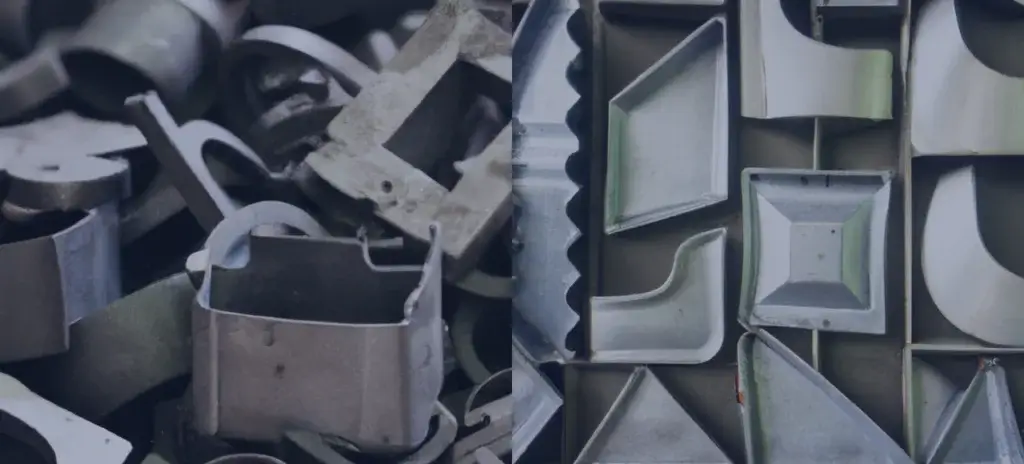
Introduction to Zinc Die Casting
Zinc die casting is a process where molten zinc alloys are injected into a steel die that has been finished with lubricant. Due to their flexibility, impact strength and low melting point, zinc alloys are used for parts production. In addition, the casting process takes place at a lower temperature due to the low melting point of the material. This makes the hot chamber die casting process. In addition, hot chamber die casting is a process that promotes longer die life and faster recovery time compared to other die casting compatible materials.
The Manufacturing Process of Zinc Die Cast Products
- Die Preparation : Clean the mold to remove impurities, then grease it so that it will be easier to push out when it cools. Finally, tighten the die with high pressure.
- Trimming : Trimming removes excess metal from other die casting defects. A saw, trim die, or other methods can be used for trimming.
- Injection : Melt the zinc alloy and pour it into the spray chamber of a casting machine. The spray chamber is heated as zinc casting is done using hot chamber die casting. The molten zinc material then gets injected into a mold under high pressure.
- Cooling & Ejection : After the zinc has cooled in the mold, loosen the mold to eject the solid zinc casting from the die.





Advantages of Zinc Die Casting over Other Manufacturing Techniques:
- Cost Effective : Zinc die casting is one of the most cost-effective methods for manufacturing metal parts, especially when high volume production is required.
- Design Flexibility : Zinc, with its complex and intricate melting point, can be cast into a variety of shapes, making it a popular option for many different designs.
- Surface Finish : Zinc die casting is ideal for applications that require a smooth surface finish, which can be easily painted or plated and thus eliminates the need for additional finishing operations.
- Material Properties : Zinc is a versatile material with good strength, corrosion resistance, and stability. It is used in many applications.
- Fast Production : This casting is an efficient and rapid production method, making it well suited for large-scale manufacturing.
- Precision : Zinc die casting can produce highly accurate and consistent parts with tight tolerances.
Applications of Zinc Die Casting Products in Various Industries
Zinc die casting parts are used in various industries due to its durability and strength. Below is a list of applications of zinc die casting products
- Home Appliances : Zinc casting is used to make a variety of household items, including belts, furniture inserts, door handles, and locks. Its strength and dimensional stability make it ideal for use in home appliances.
- Automobile/Automotive Sector : Zinc castings are used in the production of interior fittings in automobiles. These castings are preferred over aluminum because they are stronger. Examples of automotive zinc alloy castings include bearings, steering and brake parts.
- Mechanical Sector : Zinc die castings are used to produce engine parts used in mechanics. The properties of zinc, such as creep resistance and hardness, make it a more desirable option than aluminum.
- Electronics : Zinc die castings are used in the production of electronic components, such as energy regulators, toggle switches, ceramic encased resistors, or wall clocks. The Zamak-3 alloy is best suited for these parts because it offers dimensional stability.
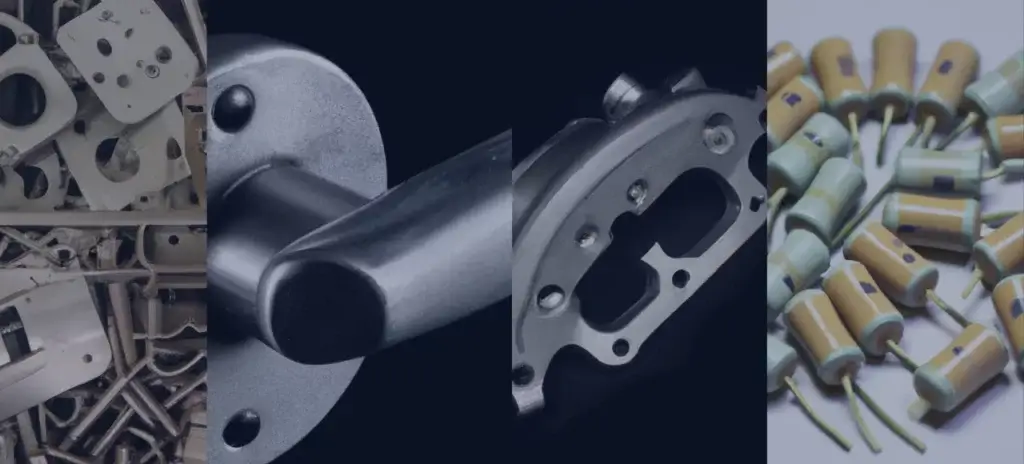
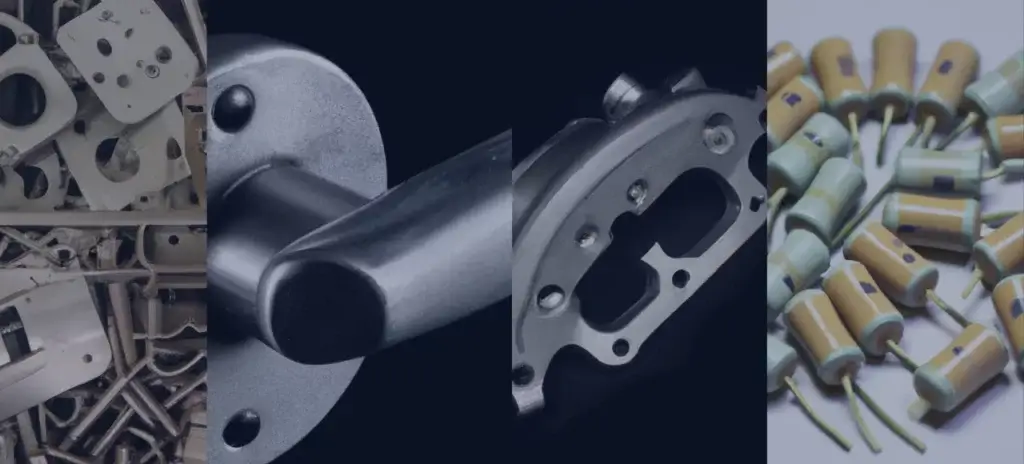
Join forces with Zetwerk for a seamless supply of high-quality zinc die cast products/parts. Experience exceptional service and consistent quality today.




