In the dynamic world of manufacturing processes and supply chains, every industry seeks the ultimate solution to attain high-quality results. One such essential innovation that has revolutionized manufacturing is the zinc casting mold. From casting zinc in silicone molds to utilizing zinc alloy die casting molds, this technology has proved its worth in delivering exceptional outcomes. This article will explore the wonders of zinc-casting molds and how they contribute to achieving top-notch results in various industries.
Zinc Alloy Die Casting Mold: Precision and Efficiency in Manufacturing
- The utilization of zinc alloy die casting molds has significantly impacted various industries and for a good reason. Zinc alloy die casting is a highly versatile technique that enables the creation of intricate and detailed components with unparalleled precision.
- Die casting molds are made from durable materials such as steel, which ensures consistent and repeatable results. The process involves injecting molten zinc alloy into the die cavity at high pressure, resulting in rapid solidification. This quick production cycle and minimal material wastage make zinc alloy die casting an economical choice for high-volume production.
- Industries such as automotive, electronics, and aerospace have embraced zinc alloy die-casting molds because they deliver strong, lightweight components with exceptional surface finishes. This has led to enhanced product performance and overall customer satisfaction.
Advantages for Various Industries in Using Zinc Casting Molds
The advantages of zinc-casting molds extend far beyond the manufacturing process itself. Several industries have reaped the benefits of utilizing these molds to achieve high-quality results:
- Automotive Industry: Zinc casting molds have found extensive use in the automotive sector, where lightweight yet sturdy components are vital. The ability to produce intricate parts with precision has resulted in improved vehicle performance, fuel efficiency, and safety.
- Electronics Industry: In the fast-paced electronics industry, zinc casting molds offer the advantage of creating small, intricate parts with excellent conductivity and thermal properties. This makes them ideal for manufacturing connectors, heat sinks, and other electronic components.
- Aerospace Industry: The aerospace industry demands components that are not only lightweight but also robust and reliable. Zinc casting molds have enabled high precision production of critical aerospace components, contributing to enhanced flight safety and fuel efficiency.
- Consumer Goods Industry: Zinc casting molds have also found applications in the production of consumer goods such as jewelry, accessories, and decorative items. The ability to easily replicate intricate designs has opened new avenues for creativity and innovation in this sector.
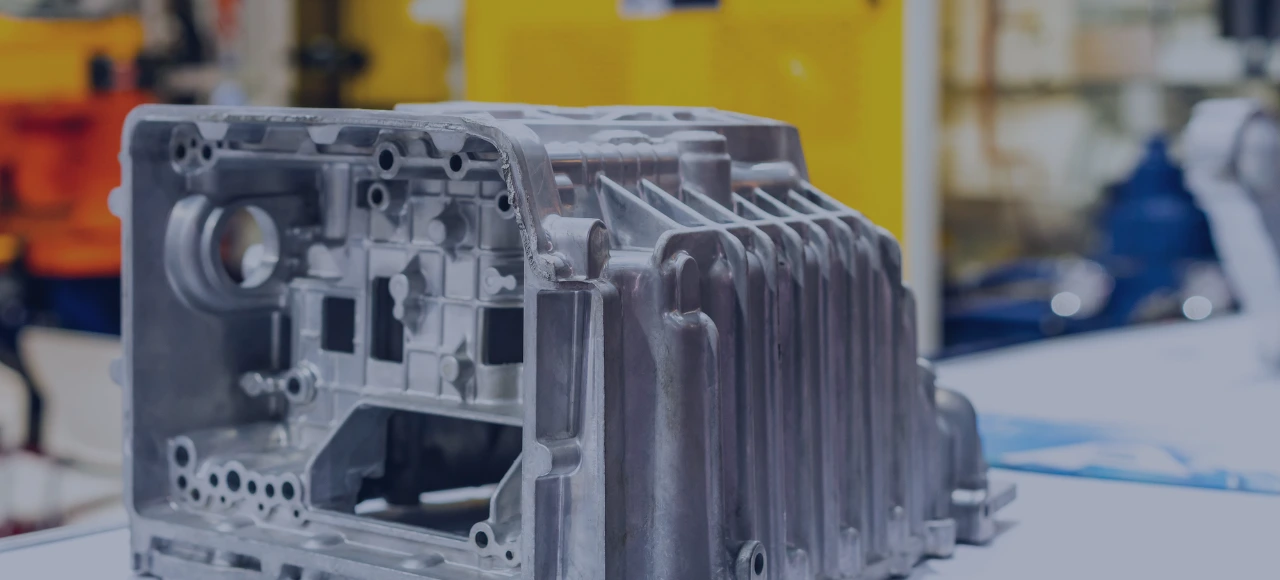
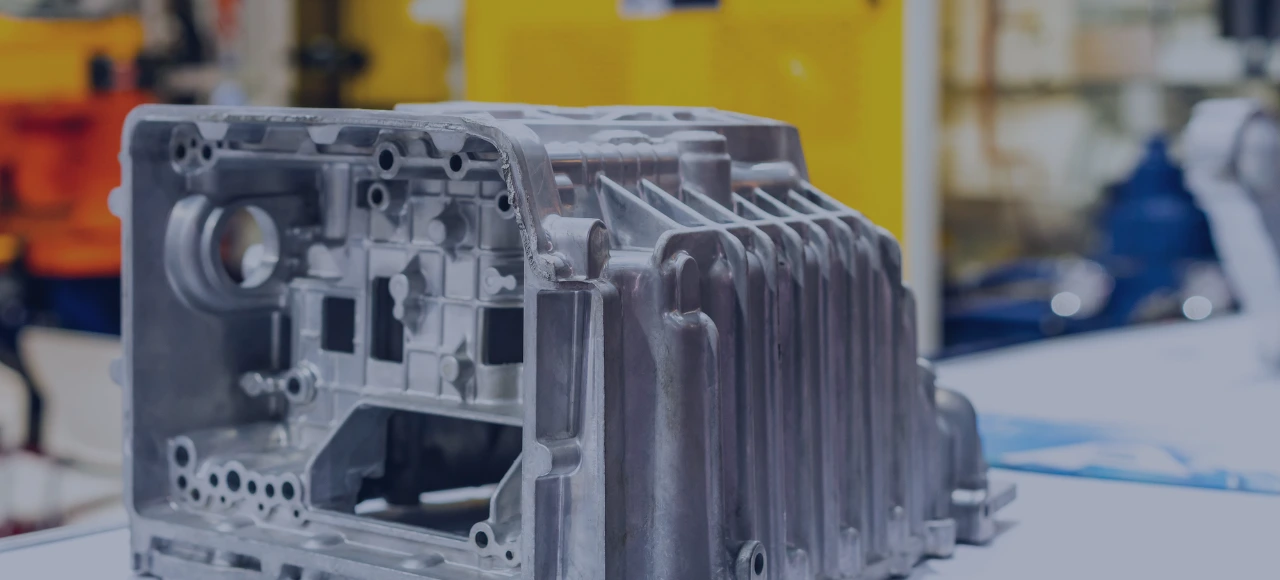
Casting Zinc in Silicone Mold: A revolutionary development in the manufacturing industry
- Casting zinc in silicone molds has emerged as a revolution for numerous industries. Silicone molds offer unmatched flexibility, precision, and durability, making them ideal for casting zinc components with intricate designs. The process involves pouring molten zinc into the silicone mold, allowing it to solidify and take the desired shape.
- Manufacturers can easily replicate complex designs with silicone molds, ensuring consistent quality across production batches. This capability reduces production time and minimizes the need for post-processing, resulting in cost-effective and time-efficient manufacturing.
Zinc Casting Mold: A Green and Sustainable Approach
Beyond their impressive technical capabilities, zinc casting molds also align with the growing emphasis on sustainability in manufacturing. As a metal, zinc is fully recyclable, allowing for a closed-loop production cycle that minimizes waste and environmental impact.
Moreover, the high precision achieved with zinc casting molds reduces the need for secondary operations, minimizing energy consumption and resource usage. Manufacturers can contribute to a greener future by adopting zinc-casting molds while ensuring top-notch product quality.
Leverage the Potential of Zinc Casting Molds in Manufacturing
Unlocking the Potential of Zinc Casting Molds, Zinc casting molds have emerged as a cornerstone of high-quality manufacturing processes across industries. From casting zinc in silicone molds to utilizing zinc alloy die casting molds, this technology provides unmatched precision, efficiency, and sustainability. Industries can achieve exceptional results, elevate product performance, and meet customer expectations by harnessing the power of zinc-casting molds. Embrace the possibilities of zinc casting molds and unlock a new era of manufacturing excellence.
Zetwerk is a leading manufacturing platform that connects businesses with top-tier suppliers, enabling seamless production and supply chain management. To explore the wide range of manufacturing capabilities and solutions, including zinc casting molds, visit Zetwerk.




FAQs
Casting zinc in silicone molds is a process that offers flexibility and precision, ideal for intricate designs. On the other hand, zinc alloy die-casting molds utilize high-pressure injection to create detailed components with exceptional precision, suitable for high-volume production.
Zinc casting molds are highly versatile and can be used for small-scale and large-scale manufacturing. They offer excellent reproducibility and can meet the demands of various industries.
Zinc is a sustainable material as it is fully recyclable. Zinc casting molds align with sustainability principles by minimizing waste and environmental impact.
Zinc-casting molds excel in creating complex shapes and intricate designs. Their precision and flexibility make them ideal for industries that require high-quality components with detailed features.
Zinc casting molds have wide-ranging applications across industries such as consumer goods, automotive, electronics, and aerospace. These industries benefit from the precision, durability, and lightweight properties offered by zinc casting molds.