Design plays a crucial role in the die casting process, directly impacting the quality, cost-effectiveness, and efficiency of the final product. To achieve high-quality die cast parts that meet performance requirements, manufacturers must consider various design factors throughout the production cycle. In this article, we will provide advanced design tips for die casting that can help optimize your manufacturing process in various industries. From material selection to tooling design optimization and surface finish considerations, these tips will enable you to produce cost-effective components with superior quality and reliability.
Top 6 Design Tips For Die Casting
The best result can come from the die casting process only when you follow certain design tips. Here are some of the major tips that one must follow.
Select the material wisely:
When designing for die casting, it is essential to carefully consider material selection based on specific properties required for the application. Strength, durability, corrosion resistance, and thermal conductivity are key factors to evaluate when choosing materials for die cast parts.
Aluminum alloys are commonly used in die casting due to their lightweight nature and excellent mechanical properties. However, other materials such as zinc alloys or magnesium can also be suitable depending on the application requirements. It is important to balance material performance with cost and availability considerations.
Optimize the Geometry of Parts:
The geometry of a part has a significant impact on its manufacturability and performance in die casting. Designers need to consider factors like shape complexity, thin walls, deep pockets, sharp corners, or undercuts when developing part geometry. Special tooling or cooling techniques may be required to address these challenges effectively.
For example, thin walls can lead to porosity or insufficient filling of molten metal. Conformal cooling channels can improve heat dissipation during solidification. Deep pockets may cause shrinkage defects or slower solidification. Incorporating core slides or complex tooling can help achieve uniform filling and efficient ejection.
Tooling Design Optimization:
The tools must withstand high temperatures, pressures, and stresses during the casting cycle while ensuring efficient filling, solidification, and ejection of parts. Factors that impact tooling design optimization are as follows:
- Gate location: Proper gate placement ensures the even flow of molten metal into the mold cavity and minimizes turbulence or air entrapment.
- Runner design: Well-designed runners facilitate smooth metal flow and help prevent cold shuts or misruns.
- Venting: Adequate venting is essential to allow gases to escape during filling to avoid porosity defects.
- Cooling channels: Optimizing cooling channels helps control solidification rates and reduces cycle times.
Surface Finish and Coatings:
The surface finish of die-cast parts is essential for both aesthetic appearance and functional performance. Depending on the application requirements, different surface treatments such as shot blasting, polishing, anodizing, plating or painting may be necessary. Surface treatments offer several benefits, like enhanced appearance, corrosion resistance, and functional performance.
Treatments like polishing or painting can improve the visual appeal of die-cast parts, making them more appealing to end-users. On the other hand, shot blasting can improve surface roughness. Anodizing or plating can provide an additional protective layer against corrosion.
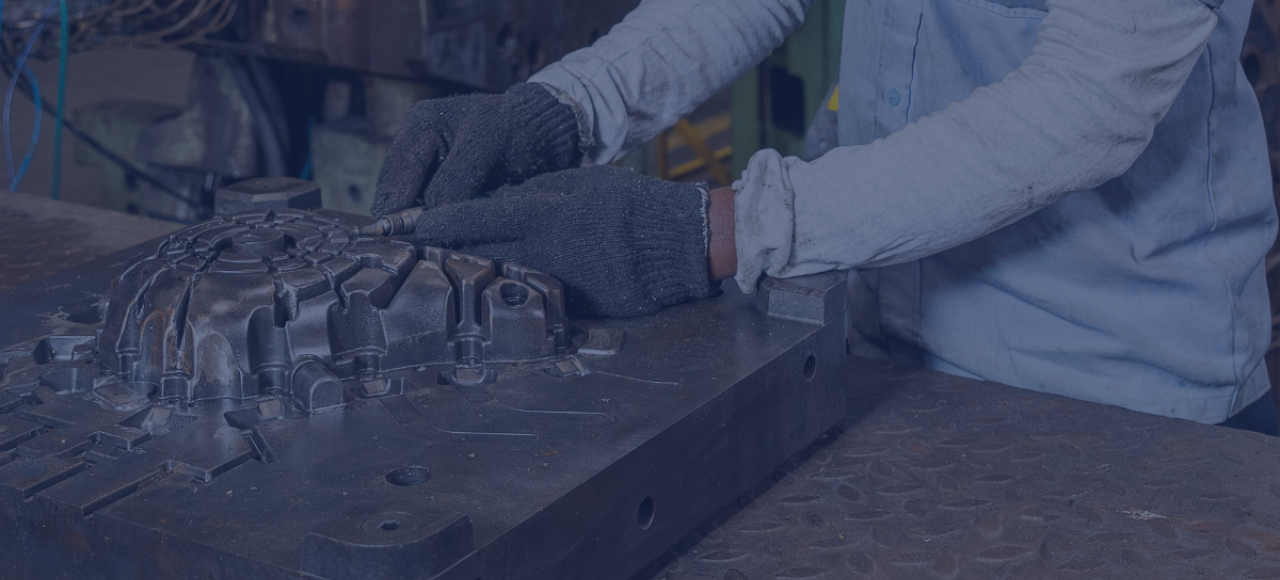
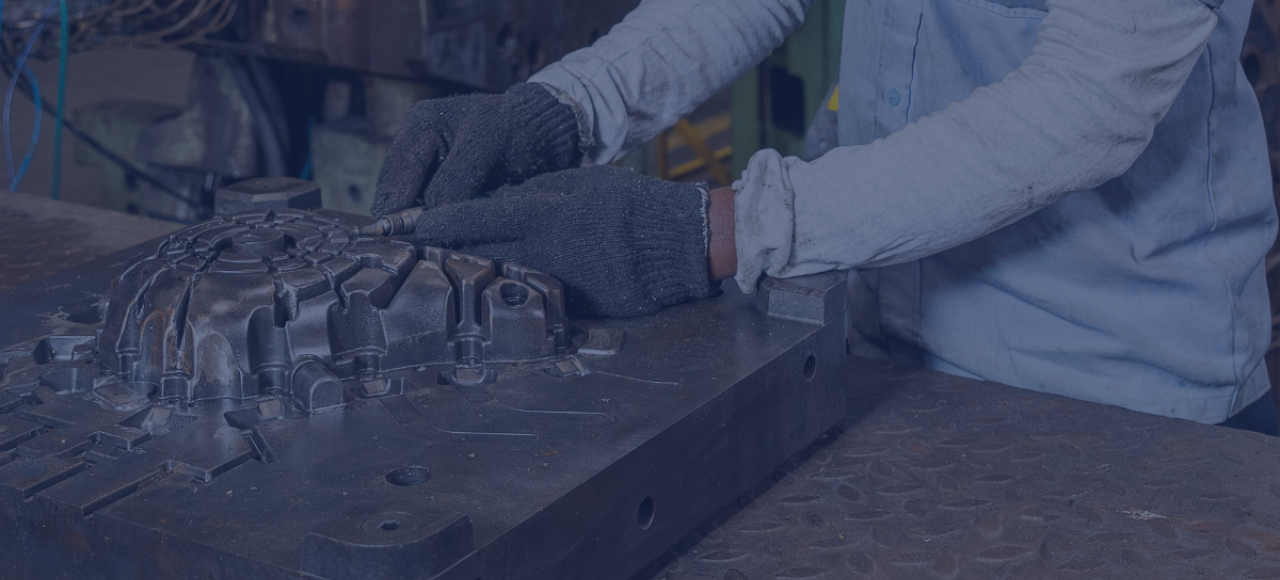
Maximize Efficiency and Reduce Cost through Design:
By maximizing efficiency in part design, manufacturers can reduce production steps and costs while maintaining quality standards. The tips to maximize efficiency through design are as follows:
- Keep designs simple: Complexity in design often translates into increased manufacturing complexity and higher costs. Simplifying part geometry can streamline production processes.
- Avoid stress concentrations: Sharp corners or sudden changes in thickness can lead to stress concentrations during solidification. Incorporating fillets, chamfers, etc., helps distribute stresses evenly across the part.
- Minimize wall thickness: Thinner walls decrease material usage and reduce cycle times without compromising necessary strength requirements.
Opt for Fine-Tuning Design through Iteration and Testing:
To ensure optimal design for die casting, manufacturers must engage in iterative processes based on feedback and testing results. This involves making design changes informed by simulation software predictions and actual manufacturing tests. Simulation software enables designers to predict potential defects before production begins. By analyzing factors like filling patterns, solidification rates, air entrapment risks or shrinkage effects during cooling, simulations help optimize die casting process parameters.
Key Takeaway
Design is a critical aspect of the die-casting process, impacting the quality, cost-effectiveness, and efficiency of the final product. By selecting materials carefully, optimizing part geometry and tooling design, selecting the right surface finishes, maximizing efficiency through design, and fine-tuning through iteration and testing, manufacturers across industries can produce quality components that meet performance requirements. The advanced design tips provided in this article ensure manufacturers not only meet their customer’s expectations but also maximize their manufacturing capabilities.
However, Zetwerk encourages manufacturers to apply these design tips in the die casting processes to produce components that are both cost-effective and reliable. For more information on how die-casting services provided by Zetwerk can help you achieve high-quality components for your business needs, please explore the Zetwerk Knowledge Hub.




FAQs
Die casting can be performed with a wide range of materials like aluminum, zinc, copper, brass, and bronze alloys. Material selection depends on factors like strength, cost, availability, and compatibility with the die casting process.
Common defects in die-cast aluminum parts include porosity, warpage, shrinkage, cold shuts, flashes, and cracks. One can minimize them through proper design considerations, tooling optimization, etc.
Optimizing cooling channels helps to achieve uniform solidification and minimize cycle time. Factors like channel placement, sizing, and shape optimization using simulation software or conformal cooling techniques help improve heat transfer efficiency and reduce part defects.
When choosing a surface treatment for your die-cast part, consider factors like desired appearance, corrosion resistance requirements, and functional performance needs (e.g., lubricity).
Simulation software allows manufacturers to predict potential defects like porosity or shrinkage before production starts. It helps optimize mold design by simulating flow patterns of molten metal during the filling and solidification stages. This leads to improved part quality while reducing costs and time-to-market.