A die casting supplier that meets your needs is key to a successful business. Researching and comparing suppliers ensures you pick the right one. As the saying goes, you get what you pay for — and that’s especially true when it comes to finding the best die cast supplier. You need to ensure you’re going with a reputable manufacturer dedicated to providing their clients with outstanding services from start to finish.
So how do you choose the proper pressure die casting supplier? Make sure they can provide you with what you need in the required time frame and can offer a creative solution if you need to be made aware of one. An ideal partnership with your pressure die casting supplier should deliver top-notch value at every touch point.
Pressure Die Casting Overview
Pressure die casting is a manufacturing process that involves injecting molten metal into a mold under high pressure to produce parts with good dimensional accuracy and surface finish. The process is suitable for producing high volumes of parts, and it is often used to produce parts with complex shapes and tight tolerances. In pressure die casting process, a mold (die) is created in the shape of the desired part, and molten metal is injected into the mold under high pressure. The metal solidifies within the mold, and the finished part is then removed from the mold. The process is typically automated, and it can produce high volumes of parts with minimal downtime.
There are several advantages that pressure die casting provides over other methods. First and foremost, it offers various metals that can be produced as castings. Most other processes will only create simple aluminum castings, whereas pressure die casting can create complex alloys in addition to aluminum.
Know more: Aluminum Die Casting.
Also, compared to other methods, there is much higher dimensional accuracy control in the final product through numeric control machines, which can promise a high degree of consistency from piece to piece. This is especially useful for industries that need precision parts that cannot fail once customers use them. Finally, and possibly most appealing to consumers, this process allows for thinner walled castings than could be achieved with traditional sand casting methods. This means these parts will weigh less and cost less due to less material used overall.
Though it has more merits, some limitations are also there. It requires complex and expensive equipment, however, and requires significant capital investment for setup. It’s also relatively inflexible compared to gravity die casting since it’s less suited to limited production runs or individual casting, which become proportionately more expensive the fewer there are.
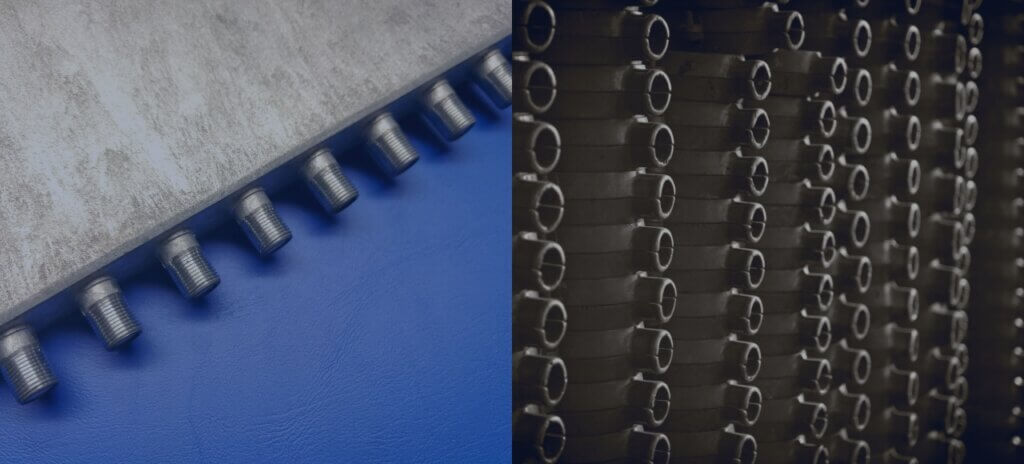
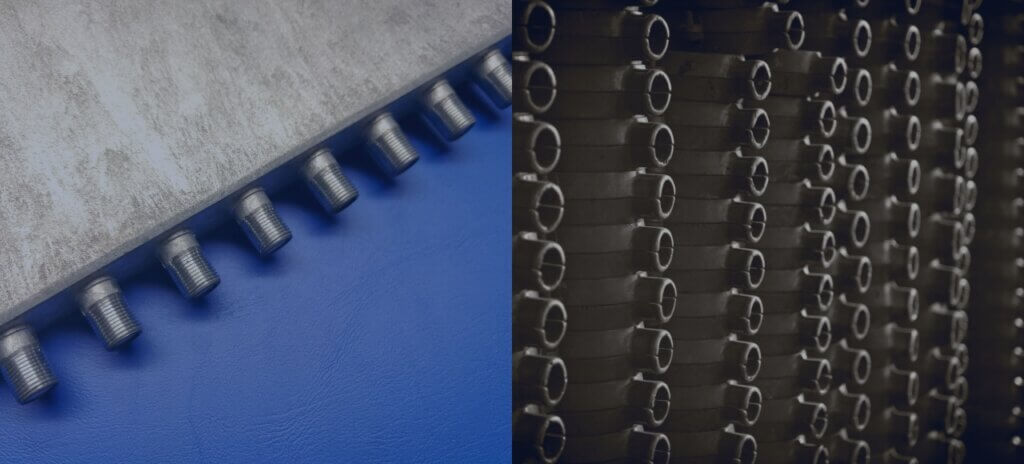
Materials Used In Pressure Die Casting
When thinking of the process, it’s important to remember that certain metals are better suited than others for the operation and that each type of mold has its strengths and weaknesses. The primary materials in pressure die casting are aluminum, zinc, and magnesium. These materials are commonly used for their excellent casting properties, strength, and corrosion resistance.
- Aluminum : Commonly used material in pressure die casting, as it is strong, lightweight, and corrosion-resistant. It has good casting properties and can produce parts with good dimensional accuracy and surface finish. Aluminum is widely used in various industries, including automotive, aerospace, and consumer products.
- Magnesium is a lightweight material often used in pressure die casting, as it is strong and has good casting properties. Magnesium can produce finished parts, and it is often used in the aerospace and automotive industries.
- Zinc is another commonly used material in pressure die casting, as it is strong, corrosion resistant, and has good casting properties. Zinc is often used to produce small, complex parts with thin walls and tight tolerances, and it can produce parts with excellent dimensional accuracy and surface finish.





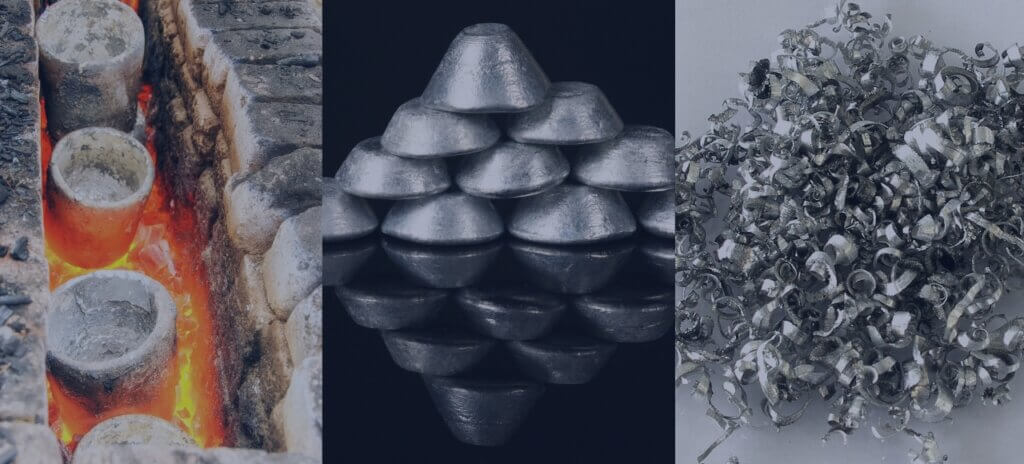
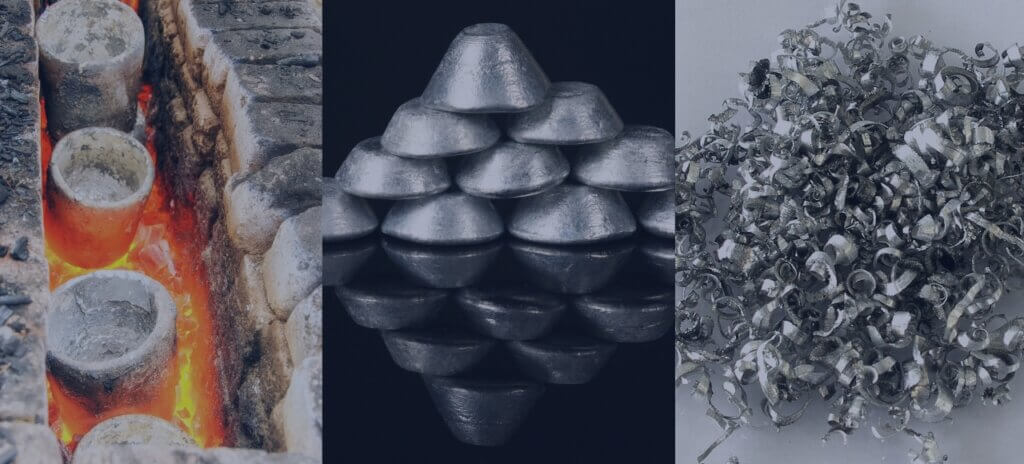
Zetwerk is not just an ordinary pressure die casting manufacturer – it is a professional partner that values customer partnership and long–term relationships. This is something that every original equipment manufacturer and end customer seeks today to accomplish set goals. With our experience and customer-centric approach, we will continue to help you meet all your design, manufacturing, and delivery needs, enabling you to focus on what you do best.
Zetwerk is proud to offer various pressure die cast products for multiple applications. We aim to meet your expectations by providing quality products, applying stringent standards, and best-in-class delivery times. We are committed to delivering high-quality customized production services for our customers.




