Precision casting manufacturers produce high-quality metal parts that are used in a variety of industries. These parts must meet strict tolerances and requirements, and the casting process must be carefully monitored to ensure that the finished product meets these standards.
Precision casting is a versatile manufacturing process that can produce various metal parts. The process begins with creating a mold used to shape the molten metal. The metal is cooled and solidified, and the finished product is removed from the mold.
Precision casting manufacturers must have extensive experience and knowledge to produce high-quality parts. They must also have the necessary equipment and facilities to produce parts that meet the required standards.
Learn More About Precision Casting
Precision casting, also known as investment casting, is a manufacturing process in which a liquid material, typically a metal, is poured into a mold made from a disposable pattern. The pattern is created using wax or plastic and shaped like the final product. The mold is then placed in a container filled with a refractory material, which surrounds the pattern and mold.
The refractory material is then cured, and the pattern is melted or burned out, leaving a cavity in the shape of the final product. The liquid material is then poured into the cavity and allowed to solidify. Once the material has solidified, the mold is broken away to reveal the final product. Precision casting produces high-quality, intricate parts with precision accuracy and surface finish.
The process often produces parts with intricate geometries and fine details that would require more than other manufacturing methods. Precision casting is also well-suited for making large parts, as the process is highly automated and can be easily scaled up to meet demand. However, the process can be more expensive than other manufacturing methods, as it requires the creation of a disposable pattern and using a refractory material to create the mold.
Precision casting is used in various applications, including the production of engine components, wind turbine blades, and other parts for the aerospace and power generation industries. In addition, the process is often used to create medical implants and other parts for the medical device industry.
Precision Casting Vs. Die Casting
What’s the difference between investment casting vs die casting? They are both manufacturing processes used to produce metal parts that involve the use of a mold to shape the final product, but there are some critical differences between the two processes:
Precision casting: It involves the creation of a disposable pattern, which is used to create a mold. The mold is then filled with a liquid metal, which is allowed to solidify. The process produces high-quality, accurate parts with a smooth surface finish. However, the process can be more expensive and have longer lead times compared to die casting.
Die casting: It involves injecting a molten metal alloy into a mold under high pressure. The process is faster and more cost-effective than precision casting and is well-suited for producing large quantities of parts. However, the process is less accurate than precision casting and may produce parts with a rougher surface finish.
The better process will depend on the specific requirements of the part being produced. Precision casting is typically the better choice for making high-quality, accurate parts with complex geometries and fine details. In contrast, die casting is better suited for producing large quantities of parts at a lower cost.





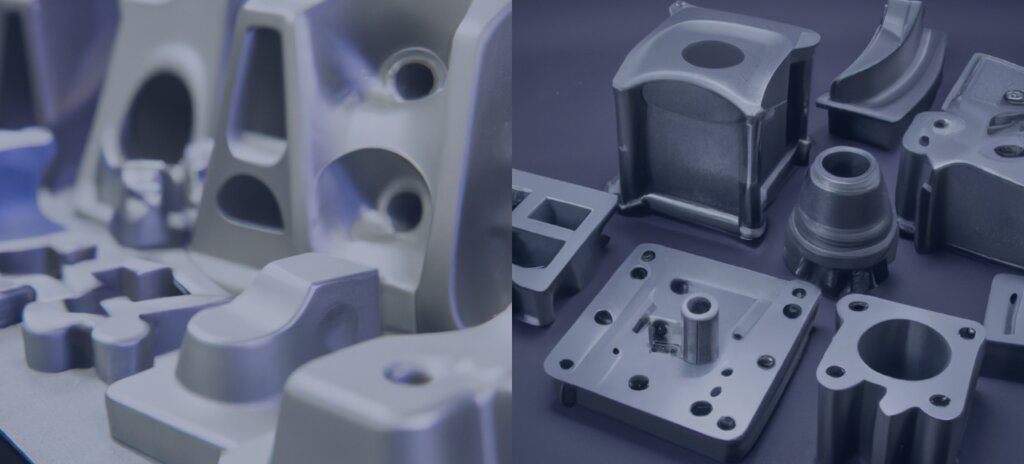
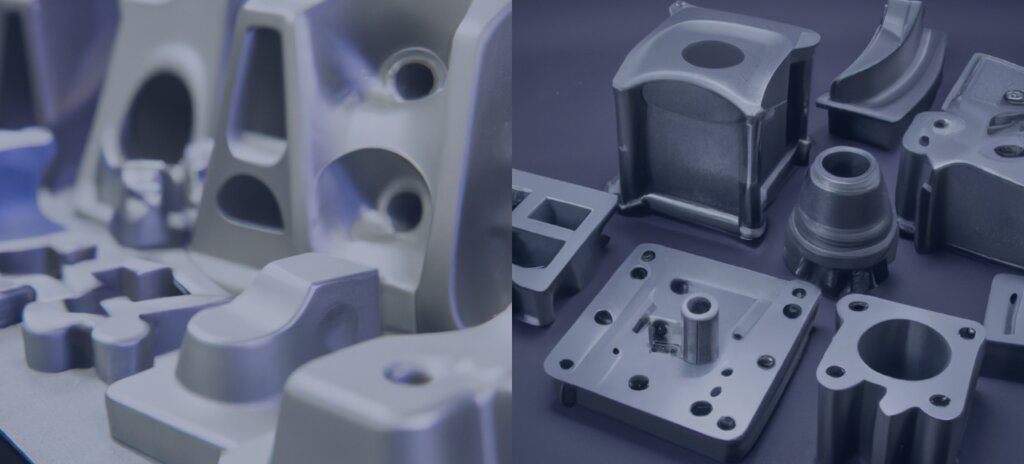
Is it Beneficial Getting Precision Cast Parts For Your Business?
There are several benefits to using precision casting to produce parts for your business:
- Ability to produce complex geometries: The precision casting process is well-suited for making parts with complex geometries and fine details that would be difficult or impossible to achieve using other manufacturing methods.
- High accuracy and precision: Precision casting produces highly accurate and precise parts with tight tolerances and a high degree of dimensional consistency. This makes the process well-suited for producing parts that require high precision, such as aerospace and medical components.
- Ability to produce large quantities: The precision casting process is highly automated and can be easily scaled up to meet demand, making it well-suited for producing large parts.
- Durability and strength: Precisely casted parts are known for their durability and strength, as the process produces parts with a uniform microstructure free from defects. This can benefit applications where the parts will be subjected to high stresses or loads.
- Cost-effectiveness: The initial cost of the precision casting process may be higher than some other manufacturing methods. The process can be cost-effective in the long run, as it allows for producing large quantities of high-quality parts with a low scrap rate.
- High surface finish: The molding process used in precision casting produces a smooth, high-quality surface finish on the final product. This can be beneficial for parts that will be visible or require a high level of aesthetics.
The need for high-quality, accurately-produced parts with complex geometries and fine details drives the demand for precision casting in the industry. The process is highly automated and can be easily scaled up to meet demand, making it well-suited for producing large parts.
We are one of the leading precision casting manufacturers in the casting industry, with over many years of experience. We have a team of experts who can help you with all your casting needs, from design to production. We use the latest technology and equipment to ensure that all our products are of the highest quality. Contact us today to learn more about our services.




