Die casting mold producers frequently start the process by talking with the customer to learn about their needs and specifications for the desired part or component. In order to produce a set of blueprints or drawings, they might utilize computer-aided design (CAD) software to create a detailed 3D model of the mold. Using these designs as a guide, the manufacturing process may be controlled to produce an accurate finished mold that matches customer requirements.
The die casting mold manufacturer will start the fabrication process after the mold’s design has been decided upon. This may entail either employing a casting procedure to build the mold or machining the mold from a solid block of steel or aluminum. The fabrication process can be rather laborious and may take many weeks or even months to finish, depending on the intricacy of the mold and the materials utilized. Once the mold has been created, it is checked and examined to ensure it complies with the necessary requirements. The mold might need to be altered or redesigned if any problems are found. The customer receives the finished mold, which can be utilized in the die casting process to create high-quality parts and components.
Factors to consider while selecting the Molding process
Various molding technologies are available, and determining the right technology is one for your needs and could be challenging. Here are a few steps one can follow to help you choose the right molding technology for your needs:
- Define your requirements: To get started, it’s essential to grasp precisely what it is you need to manufacture. Dimensional, geometrical, material, and quantitative constraints may all come into play.
- Research your options: After that, learn more about the various molding technologies that are now in use and their capabilities. The technology mentioned here could be die casting, injection molding, blow molding, or compression molding.
- Consider the materials: Different materials respond better to different molding technologies. For instance, die casting is frequently used for metals, while injection molding is frequently used for polymers. Consider the substance you’ll be working with before choosing a technology.
- Consider the lead time: The production lead time is crucial, particularly if you have a limited timeframe. Examine the molding technology’s speed to see if it can fulfill your schedule.
- Look for experience: Seek out a business with expertise in the molding technology you’re thinking about. By doing so, it will be possible to guarantee that they possess the skills and knowledge necessary to produce parts and components of excellent quality.
- Evaluate the cost: The price of the molding technique is crucial. The equipment’s initial price, as well as the ongoing costs of supplies, labor, and upkeep, should be considered.
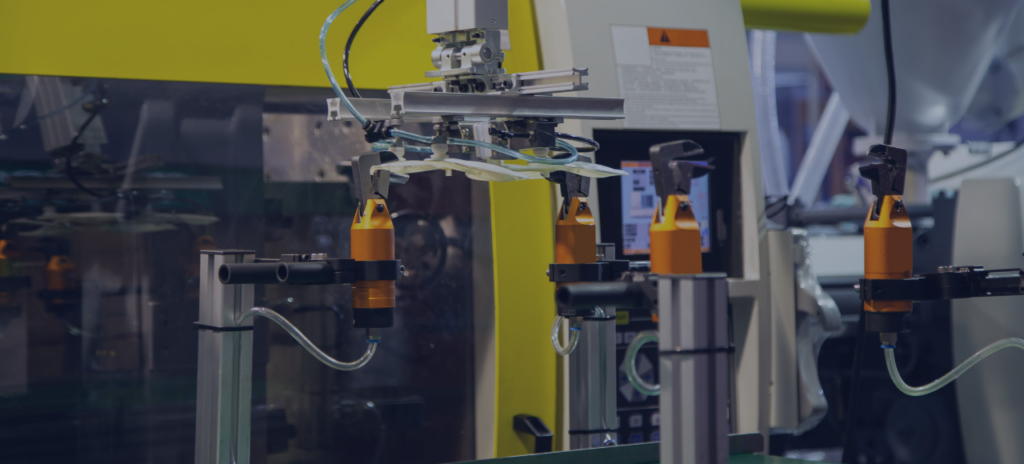
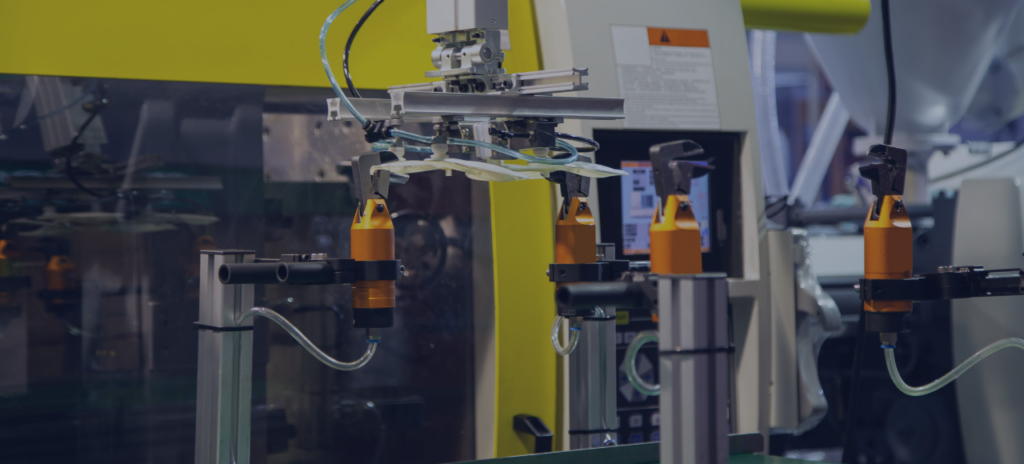
How to Choose a Die Casting Mold Manufacturer
There are several aspects to consider when selecting a die casting mold manufacturer to ensure that you choose a firm capable of meeting your objectives and providing high-quality molds. Here are some factors to note while choosing the right die casting mold manufacturer:
- Experience: Choose a company with a successful history in the die casting industry. This suggests they possess the skills and knowledge required to create molds of the highest caliber.
- Quality control: High-quality molds are necessary to produce precise and reliable parts and components. Choose a business that prioritizes quality control and has procedures in place to ensure its molds adhere to the requirements.
- Cost: Price is always a consideration, but it’s crucial to strike a balance between it and quality. Find a provider that offers reasonable prices without compromising on quality.
- Capabilities: Make sure the business is qualified to satisfy your unique requirements. This is an example of working with a particular material or creating molds of a specific size or complexity.
- Customer service: In any industry, providing excellent customer service is essential, but die casting molds are where it counts. Choose a business that is accommodating, simple to work with, and eager to go above and beyond to satisfy your demands.
- Capabilities: Make sure the business is qualified to satisfy your unique requirements. This is an example of working with a particular material or creating molds of a specific size or complexity.
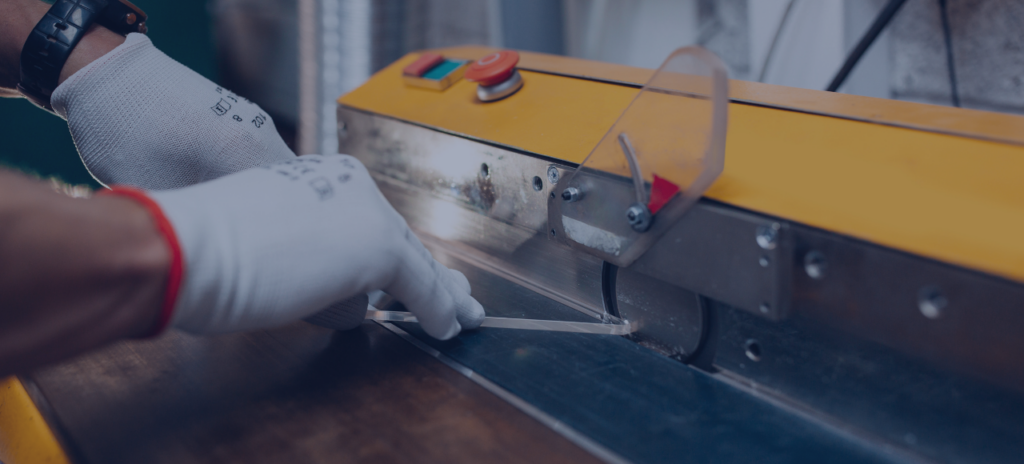
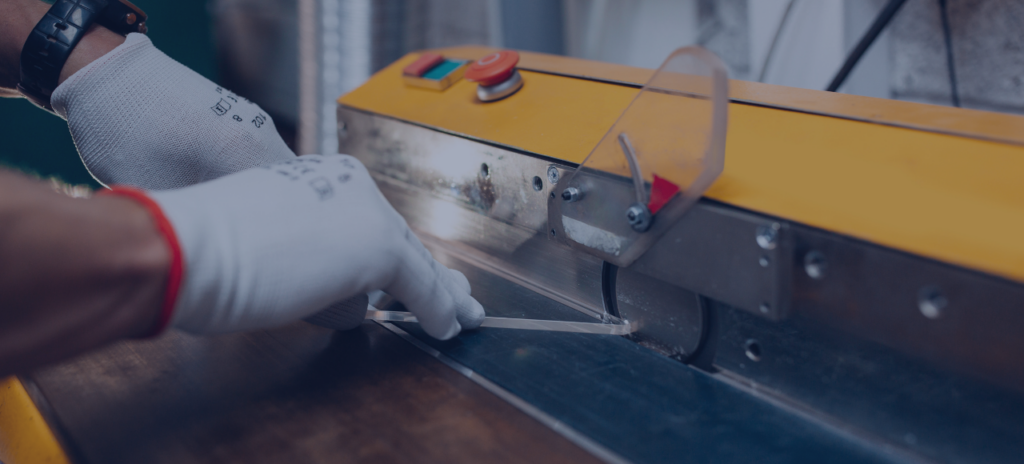
Zetwerk, A Leading Die Casting Mold Manufacturer and Service Provider in the USA
Zetwerk is a renowned American manufacturer and service supplier of die casting molds. The company has a reputation for making high-quality molds and providing excellent customer service. Zetwerk’s vast manufacturing capabilities are one of its primary strengths. The company can work with various materials, including aluminum, zinc, and brass, and can manufacture molds of varying sizes and complexities. This flexibility enables them to address the needs of a diverse clientele, ranging from small startups to massive businesses.
In addition to its manufacturing capabilities, Zetwerk provides various customer-supporting services. This includes prototyping, design aid, and manufacturing support, all intended to assist clients in bringing their goods to market as quickly as possible. Zetwerk’s devotion to quality is an additional crucial advantage. The organization employs stringent quality control procedures to ensure its molds satisfy the necessary specifications and manufacture high-quality parts and components. In addition, they have a team of specialists committed to offering excellent customer service, making it easier for clients to deal with them and receive the necessary support throughout the manufacturing process.
How Die Casting Mold Manufacturer can Boost Your Profit
Partnering with a reputable and skilled die casting mold manufacturer can help boost your profit in several ways:
- Better product quality: By using molds that are carefully designed and fabricated, you can produce parts and components that are of a higher rate. This can help improve customer satisfaction and increase repeat business, leading to increased profits.
- Improved efficiency: High-quality molds accurately made to specification can result in fewer defects and scrap, leading to a more efficient production process. This can reduce costs and increase profitability.
- Customization options: Many die casting mold manufacturers offer customization options to meet the specific needs of their customers. By working with a manufacturer that can create molds tailored to your particular requirements, you can differentiate your products in the market and potentially increase profits.
- Faster production: Working with a reliable die casting mold manufacturer can help reduce lead times, allowing you to get your components to market faster. This can help you meet customer demand more effectively and increase profitability.
- Cost savings: Partnering with a reputable die casting mold manufacturer can help secure competitive pricing for your molds, leading to cost savings and increased profits.