The automotive sector is characterized by intense competition, driven by the requirement to improve fuel efficiency and reduce emissions. With the number of vehicles on the roads reaching record levels, reducing weight has become crucial in reducing fuel consumption and decreasing CO2 emissions. Manufacturers have found a solution in die casting to meet the demands of the automotive industry. This metal casting process transforms molten metal into high-quality machined parts, such as engine blocks and gearboxes. By utilizing die casting in automotive industry, manufacturers can minimize waste, save time and reduce costs, providing a win-win scenario for producers and customers.
Process Involved In Producing Automotive Parts Using Die Casting
- Hot Chamber Die Casting : In this technique, a gooseneck machine uses a built-in furnace to heat the metal until it melts. A hydraulically powered piston uses a nozzle and gooseneck to push the molten metal out of the furnace into the die chamber. The molten metal is then held under pressure in the die cavity until solidified. Die casting involves heating a metal until it melts, then forcing that liquid metal into the shape of a mold. It has a characteristic melting point. It works best with metals with low melting points, such as zinc or magnesium; aluminum is unsuitable for this process because of its high melting point.
- Cold Chamber Die Casting : To fill a die cavity with molten metal, an operator pours the metal into a shot sleeve placed over the injection cylinder. The plunger forces the molten metal into the die cavity without heating the sleeve. Cold chamber die casting uses pressures of 30 MPa to 150 MPa. This process uses high melting point aluminum alloys. Cold chamber die casting is a successful method of producing automotive components. The process results in dense metal castings and stronger automotive parts. It’s easy to perform, requires less maintenance than other processes, and has excellent dimensional accuracy.
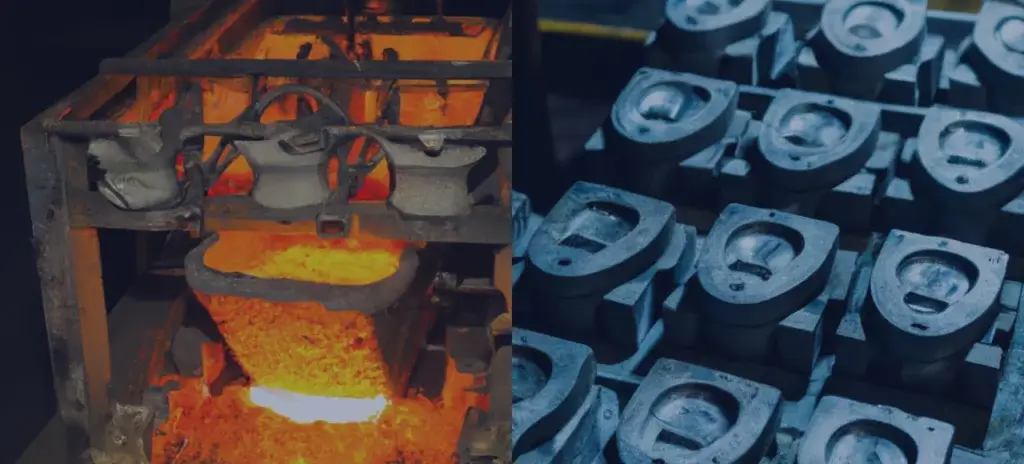
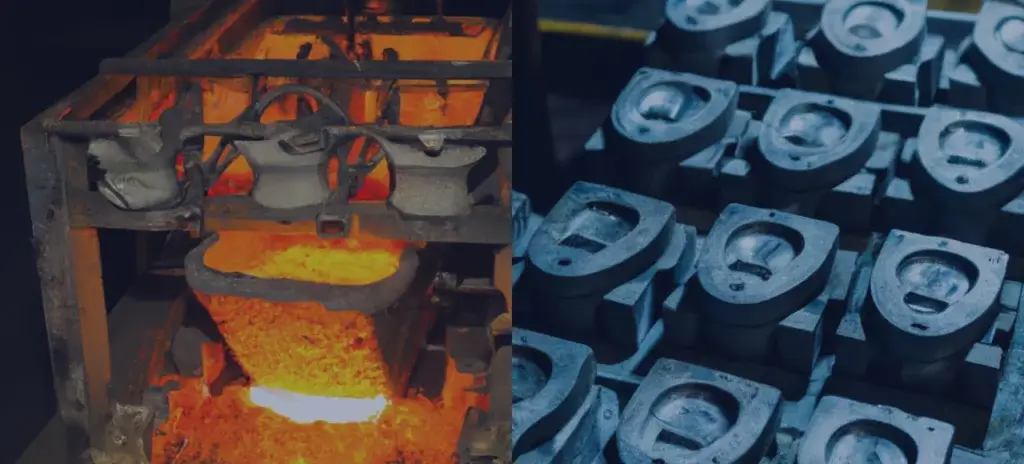
Benefits Of Die Casting In Automotive Industry
- Lightweight Components : One of the main reasons die casting has become so common in the automotive industry is that it’s a fantastic way to produce lightweight components. While other methods might be cheaper or faster, die casting offers a number of advantages when it comes to creating light parts that can be used in cars, trucks, and other vehicles. By reducing the weight of their vehicles, manufacturers can save money on shipping costs. They may then pass these savings on to customers through lower prices. As a result, consumers can save money on gas because they are driving lighter cars. Casting automotive parts in lighter materials can help manufacturers improve their energy efficiency, reducing the amount of waste they produce in the manufacturing process. This will contribute to a reduction in carbon emissions and global warming.
- Enhanced Productivity : Die casting is a highly efficient manufacturing process, requiring less labor per product production unit than traditional manufacturing processes. For illustration, Die casting machines can produce four times as many wheel hubs per operator as other casting equipment. This indicates that businesses can reduce the cost of their products by switching from more traditional production procedures to die casting as an alternative.
- Increased Flexibility & Automation : Die cast parts are ideal for mass-produced vehicles because they can be produced in large quantities. Die cast wheels, chassis, suspension systems, and body panels are used in standard vehicle models and custom-built cars. Die cast parts in the automotive industry are often used in multiple vehicles or sold as spare parts when production exceeds the manufacturer’s inventory needs.
Materials Used For Die Casting In Automotive Industry
Automotive parts use a variety of alloys. Die casting is an excellent process for machining these different metals because it can handle many materials. Here are some examples:
- Magnesium: It is commonly used metal alloy for casting. It is used to make strong alloys, which are often added to other metals to create parts of superior strength. Magnesium-containing alloys also have excellent heat conduction properties, making them ideal for use with high-temperature tools that need to be cooled down quickly after use.
- Zinc: Die casting uses zinc alloy the most frequently. It is the perfect material for making dies that can be used in several kinds of casting machines because of its high strength, superior corrosion resistance, and good surface polish.
- Aluminum: It is commonly used metal alloy for casting. The primary aluminum component is alumina, which can be used as an additive to other metals to make them more durable or more substantial. Aluminum alloys are the most commonly used mold raw materials due to their excellent heat transfer properties, surface finish, and low cost.





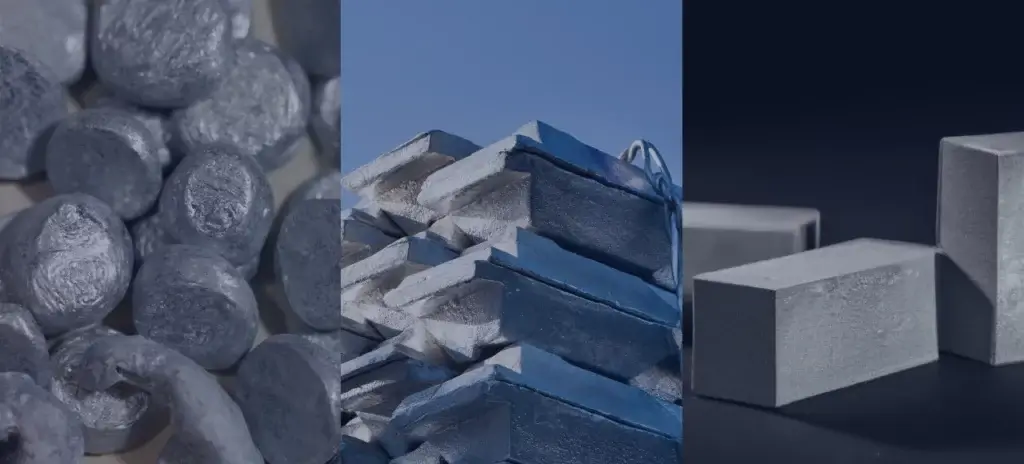
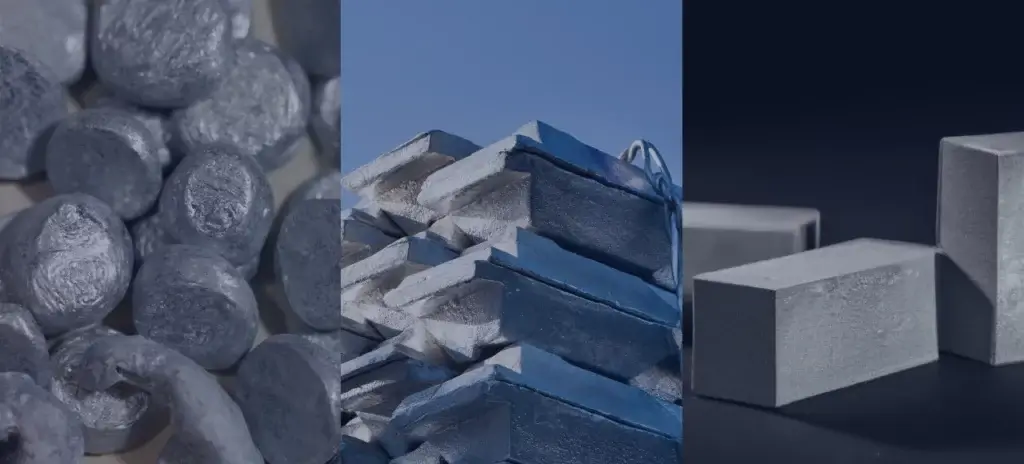
Reasons For Rising Trend Of Die Casting In Automotive Industry
In 2021, die casting in automotive industry was estimated for 61 billion dollars worth of production. By 2027, the die-casting process will be worth another 20 billion dollars in the automotive industry. The question on everyone’s mind is, “Why is this process making so much money?” Die casting makes so much money because of several factors. First, the automotive industry is moving toward making cars lighter. This is possible with die casting because die cast parts are thinner and lighter than other parts. Die casting has other advantages. In addition to being economical, it makes the workflow more efficient and produces high-quality products. This makes die casting attractive to many manufacturers.
Contact Zetwerk for reliable die cast parts supply for your business needs.




