Die casting is a manufacturing method in which molten metal is injected under high pressure into a mold or die. The resulting components are referred to as die cast parts. The procedure is highly effective and capable of producing parts with exceptional precision and fineness.
Gravity die casting, low-pressure die casting, and high-pressure die casting are among the various types of die casting. The type of die casting employed is determined by the type of metal being used, the shape and size of the component being manufactured, and the needed production volume.
Die casting enables the production of complex and intricate components, which is one of its primary advantages. Making items with thin walls, sharp edges, and complicated features is feasible, which would be difficult or impossible to do using traditional production procedures.
Speed is another advantage of die casting. The technique is highly automated and capable of producing components rapidly, making it a viable alternative for high-volume manufacturing runs. Die casting is also a very affordable technique, which makes it an economical option for many firms. Die cast components are utilized in the automotive, aerospace, electrical, and medical industries. They can be found in automobile engine components, power tools, and electronic equipment.
Die casting demands a great level of skill and precision, which is one of its challenges. To assure the accuracy of the pieces, the dies used in the process must be carefully designed and maintained. In addition, the procedure demands the utilization of high temperatures and pressures, which might be hazardous if not adequately regulated. Despite these obstacles, die casting is an essential manufacturing method used to make a vast array of components for a variety of applications. Numerous manufacturers favor it due to its speed, precision, and affordability.
Why are die casting parts widely used?
Die casting provides a number of advantages over other production processes, which has led to its widespread use. Among the many reasons for die casting’s popularity are:
- High accuracy and detail: Die casting permits the production of components with a high level of precision and complexity, including thin walls, sharp corners, and intricate details
- Strength: Typically, die-cast parts are stronger and more durable than ones manufactured using other methods.
- Wide range of applications: The automotive, aerospace, electrical, and medical sectors are just a few of the many that rely on parts made from die casting.





- Versatility: Die casting can be used to make parts from a wide variety of metals, including aluminum, zinc, and copper.
- Speed: The technique is highly automated and capable of producing components rapidly, making it a viable alternative for high-volume manufacturing runs.
- Cost-effective: Die casting is a relatively affordable technique, making it a cost-effective option for many industries.
- Low waste: Die casting is an environmentally sound method since it generates minimal scrap.
The premium materials in die casting parts
Various materials are used in the die casting process, including metals and alloys. Some of the premium materials commonly used in die casting parts include:
- Magnesium: Die casting often makes use of magnesium since it is both light and sturdy. Wheels, steering components, and electrical housings are only some of the products to which it is put to use.
- Zinc: Metal die casting frequently employs zinc because of the metal’s strength and malleability. The company manufactures a variety of products, including hardware and auto parts.
- Steel: Steel is a strong and long-lasting metal used in die casting. It is used to manufacture various items, including automotive and industrial machinery components.
- Copper: Copper is a popular metal for die casting because it is durable and electrically conductive. Connectors and switch housings are only two of the many products it makes for the electronics and electrical sectors.
- Aluminum: In the die casting industry, aluminum is commonly utilized because of its low cost, high strength, and high corrosion resistance. It manufactures various components, including those for automobiles and electronic enclosures.
In general, the material selection for die casting is determined by the specific requirements of the produced item, including its strength, corrosion resistance, and conductivity.
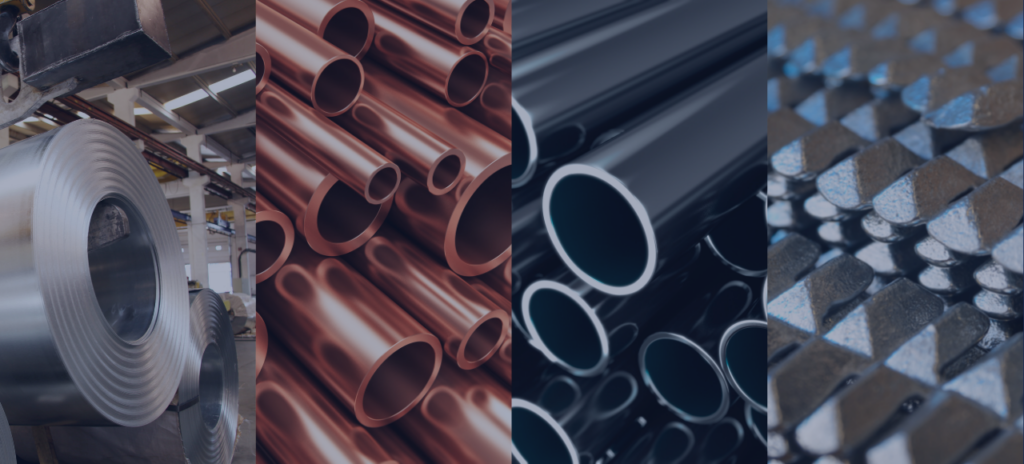
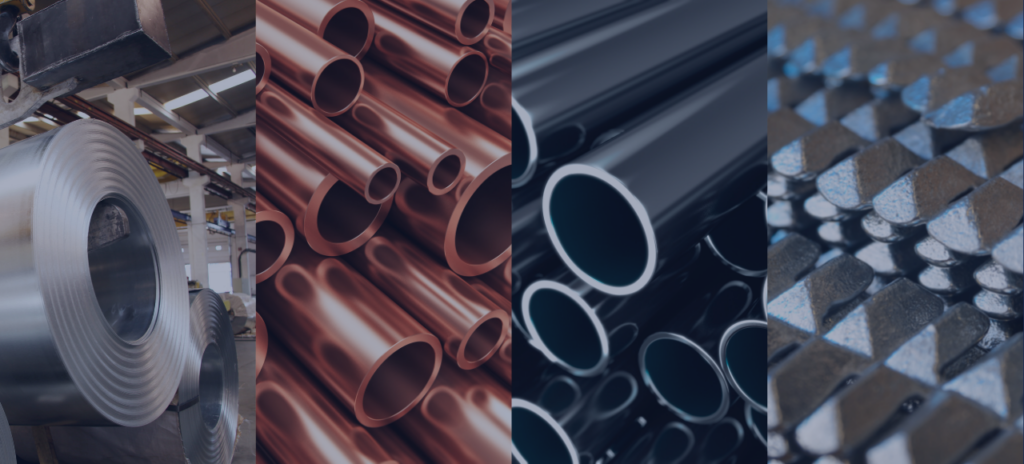
Industrial Application of Die Casting Parts
Die casting parts are used in a wide range of industries, including:
- Automotive: Different components, including engines, transmissions, and suspensions, are all made using die casting elements in the automotive industry.
- Industrial machinery: Components for industrial machineries, such as pumps and valves, are manufactured using die casting.
- Aerospace: Aerospace components, including structural and engine parts, are manufactured using die casting.
- Electrical: The electrical sector relies on die casting to create components like connections and electronic device housings.
- Consumer goods: Die casting is a manufacturing process that creates components for a variety of consumer items, including power tools and electrical devices.
- Medical: Medical instruments and implants are only two examples of the kinds of products that can be manufactured using die casting in the healthcare sector.
- Defense: Parts for guns and military vehicles are manufactured using die casting.
- Construction: Building hardware like door knobs and lock sets are manufactured using die casting.
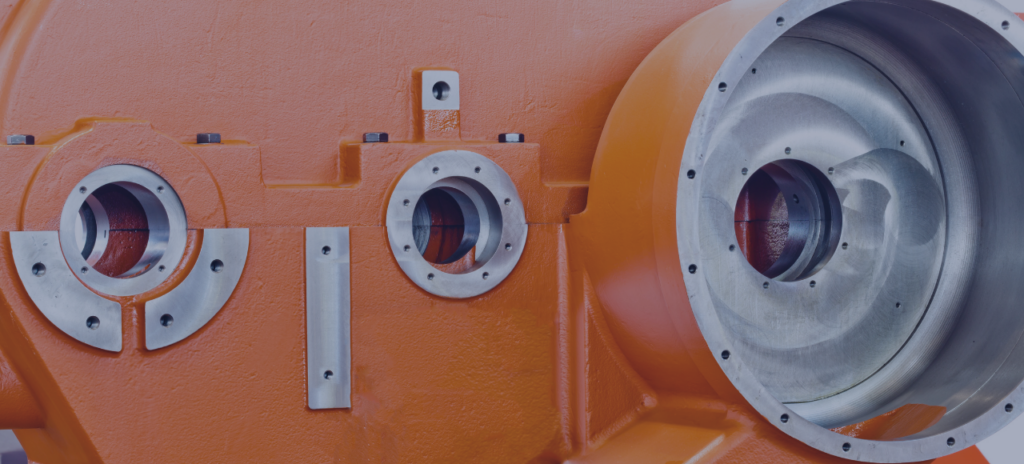
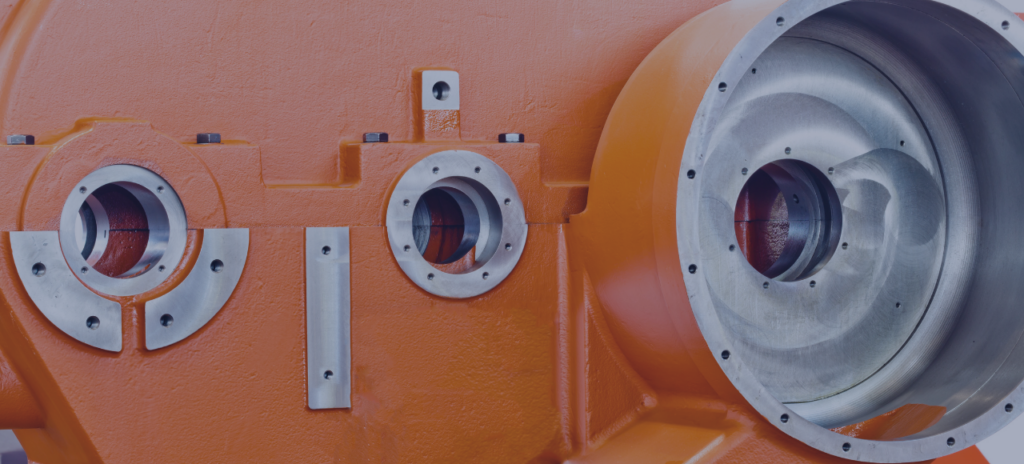
Custom die casting refers to the production of die casting parts designed and manufactured to meet a customer’s specific requirements. This can include the parts’ shape, size, material, and special features or finishes.
We at Zetwerk deal with custom projects to produce parts tailored to your requirements and needs. The benefits of custom die casting at Zetwerk is that we manufacture die casting parts with a high level of accuracy and detail and based on the requirements of your components in small or large quantities, and materials.




