Numerous best die casting methods used when manufacturing metal parts and components. In most industries, die casting is the preferred manufacturing process for producing metal parts. Due to its popularity and versatility, die casting is best known for producing clear, colorful parts with high-quality finishes. Moreover, the high production speeds can be attributed to the small number of tools used in this process. In terms of cost-effectiveness, die casting is less expensive than other processes, such as extrusion or forging.
What is Die Casting?
Die casting is a metal-forming process that has become popular in small and large-scale industries. It is often used to make components with many intricate details and designs. Die casting enables many identical products to be quickly produced, making it perfect to mass-produce numerous complex pieces of machinery.
Types Of Die Casting
- Hot Chamber Die Casting
A prevalent casting method is a hot-chamber process known as gooseneck casting. Hot-chamber die casting requires a chamber in constant contact with the liquid alloy and a valve for pouring metal into the casting chamber; a piston plays an important role, as it helps push molten metal into the chamber at high speed.
The hot chamber die casting process is used for metals with a low melting point, such as copper, magnesium, zinc, tin, and lead. While this process has several advantages, the main one is that direct dipping quickly transfers the molten metal into the mold cavity.
- Cold Chamber Die Casting
Cold-chamber die casting is a casting that uses an injection system. The molten metal is poured into the injection molding system in a cold room. Unlike hot chamber casting, the injected metal is cooled with water to prevent it from becoming corroded before the die can shape it. Cold-chamber die casting is suitable for metals with higher melting points, such as aluminum and copper.
A variation on these types implied in producing parts include:
- High-pressure die casting
- Low-pressure die casting
- Semi-solid die casting
- Squeeze die casting
- Vacuum die casting
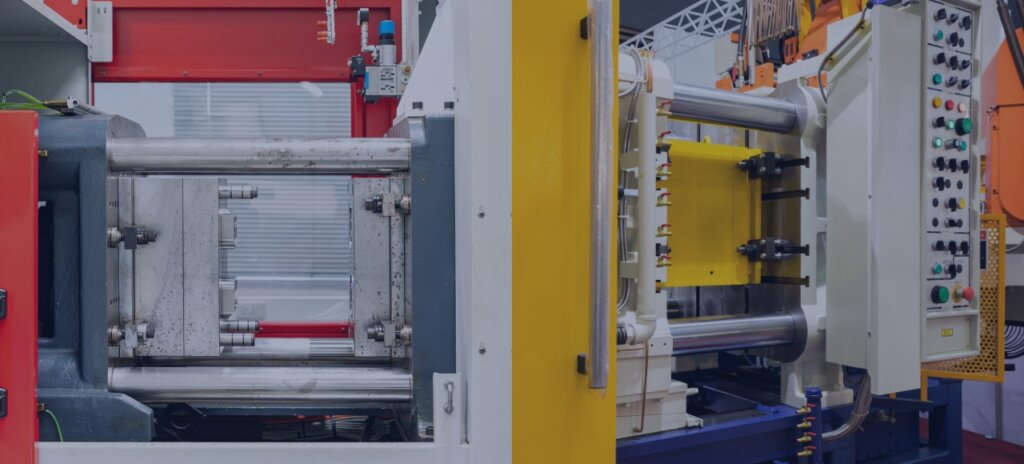
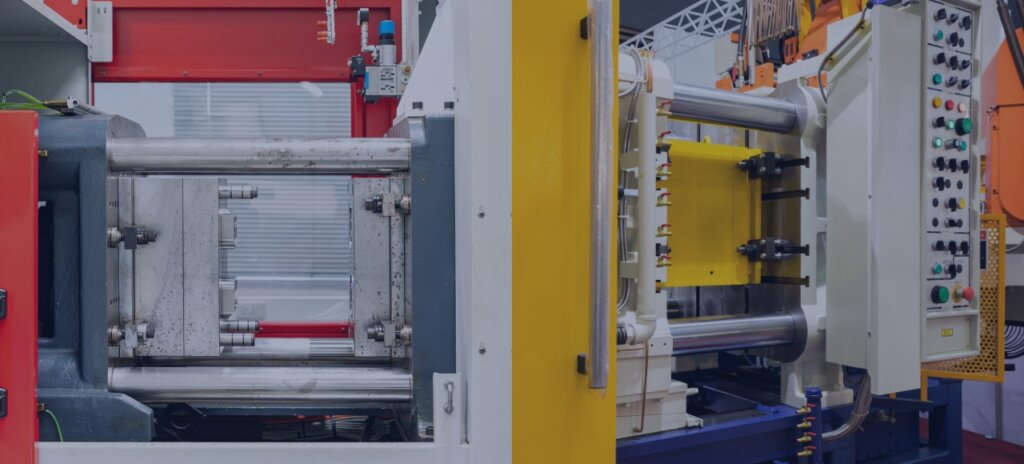
Which Is Best Die Casting: Hot Chamber Or Cold Chamber?
Hot and cold-chamber casting are both used to make metal parts. The hot chamber process, however, has some advantages over the cold chamber process: it is faster, more economical, less dangerous, and has a longer tool life than the cold chamber process. Hot-chamber casting indeed has its merits. But cold-chamber casting also has merits of its own. It’s hard to say which is the best die casting method because they differ. There are many different types of alloys, each with its properties. Hot chamber casting can be used to cast low melting point alloys. These include lead, magnesium, and zinc alloys.
Cold chamber casting is used for high melting point metals like aluminum, magnesium, ferrous, and copper alloys. When you are choosing an alloy, don’t focus on the process. You need to select an alloy that fits the requirements of the part you want to make. The alloy you choose determines the necessary production tools to make the required parts.





Die Casting Materials
Some of the materials that are commonly used for die casting include:
- Aluminum: Aluminum is a popular choice for die casting due to its combination of strength, weight, and corrosion resistance. It is also relatively inexpensive compared to other metals, making it a cost-effective choice for producing high volumes of parts.
- Zinc: Zinc is a popular choice for die casting due to its low melting point, which allows for faster production times. It is also strong and corrosion-resistant, making it suitable for various applications.
- Brass: Brass is a popular choice for die casting due to its strength and corrosion resistance. It is also relatively easy to cast, making it suitable for producing complex shapes.
- Bronze: Bronze is a popular choice for die casting due to its strength, corrosion resistance, and ability to withstand high temperatures. It is also relatively easy to cast, making it suitable for producing complex shapes.
- Magnesium: Magnesium is a lightweight metal popular for die casting due to its low density and high strength-to-weight ratio. It is also relatively easy to cast, making it suitable for producing complex shapes.
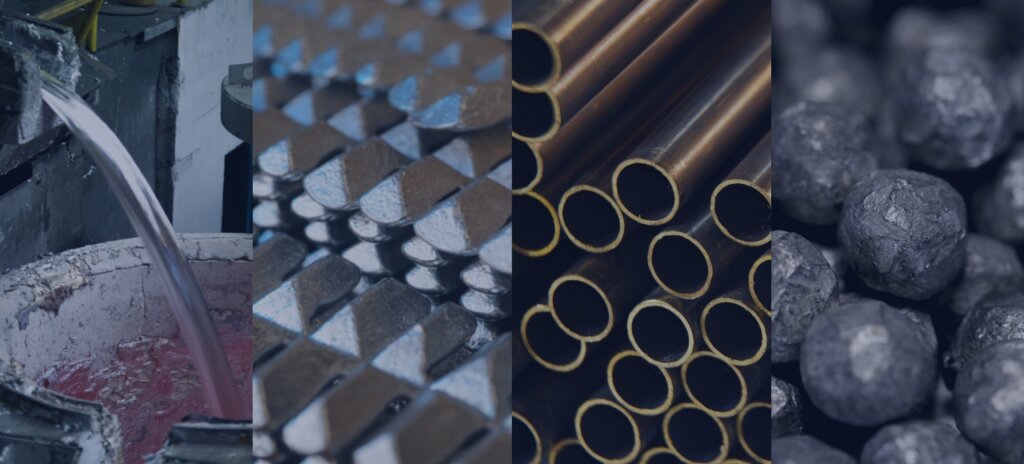
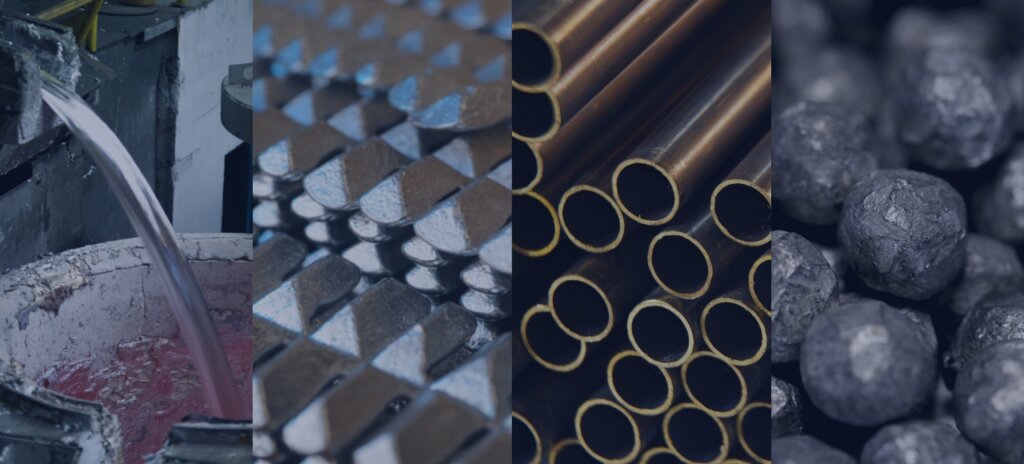
Industries That Use Die Casting
Some of the industries that use die casting highly include:
- The automotive industry relies on die casting to produce various parts and components, including engine blocks, transmission parts, wheels, and structural components.
- The aerospace industry uses die casting to produce various parts and aircraft components, including structural components, landing gear, and fuel system components.
- Die casting is used in producing electronic devices, appliances, and lighting fixtures, among other consumer products.
- Die casting is also applied to making various industrial equipment, such as pumps, valves, and bearings.
Finding a competent, capable, and best die casting company is challenging. Zetwerk is your best bet to ensure you have the right product at the right time. We know you want success, so we’ll do our best to provide it. Let us know what you’re looking for, and we’ll be able to help create exactly what you need.
Whether you need prototype die cast parts, a manufacturing partner for your business or manufacturing facilities, or something in between, Zetwerk is here to help. The choice is yours, so pick the one that’s right for you and start creating your next custom-made project today!




