Introduction
In modern manufacturing, precision, durability, and efficiency are paramount. It’s the crucible where innovation meets practicality, and few processes embody these ideals as masterfully as aluminum pressure die casting. In this article, we embark on an exploration of this transformative technique, delving deep into the heart of its significance, advantages, applications, and prospects. Brace yourself for a journey through the world of high-pressure aluminum die casting, where we unveil the unique attributes that set it apart as the go-to method for crafting high-quality aluminum pressure die casting products.
Know About Aluminum Pressure Die Casting and What Sets It Apart?
Understanding Aluminum Pressure Die Casting
At its core, aluminum pressure die casting is a metalworking process that leverages high-pressure methods to shape molten aluminum into a desired form. What sets it apart is the use of high-pressure aluminum die casting, which ensures the creation of components with unrivaled accuracy and surface finish. This precision makes it the preferred choice for industries where quality and consistency are non-negotiable.
Key Advantages of Aluminum Pressure Die Casting
The use of aluminum as the primary material in this process is a game-changer. Aluminum pressure die casting is not only lightweight but also possesses excellent thermal conductivity and corrosion resistance. These qualities make it a top choice for industries requiring precision and durability.
Moreover, high-pressure aluminum die casting process enhances the final product’s quality and precision. The pressure used in the process eliminates porosity and voids, ensuring that the end product is virtually flawless. The exceptional repeatability and consistency achieved through this method are unmatched by other casting processes.
The Aluminum Pressure Die Casting Process
To understand why this technique is so exceptional, let’s delve into the intricate aluminum pressure die casting process it entails. The aluminum pressure die casting process involves several key steps, each executed with meticulous precision.
Die Preparation: It begins with the preparation of a steel mold, or die, which is precisely engineered to match the intended product.
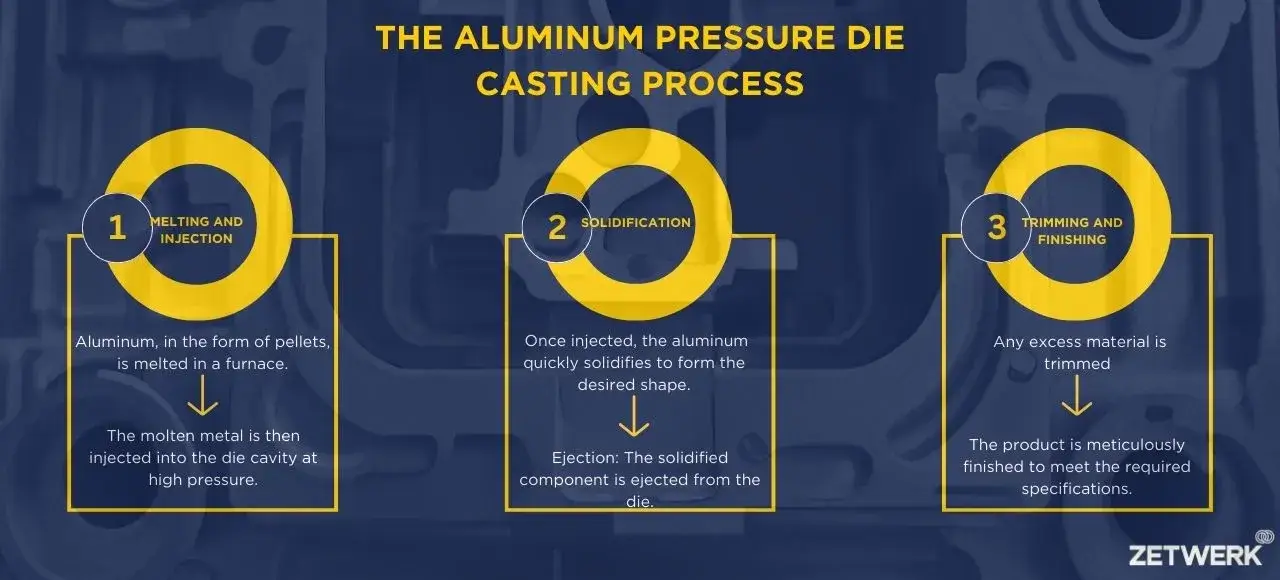
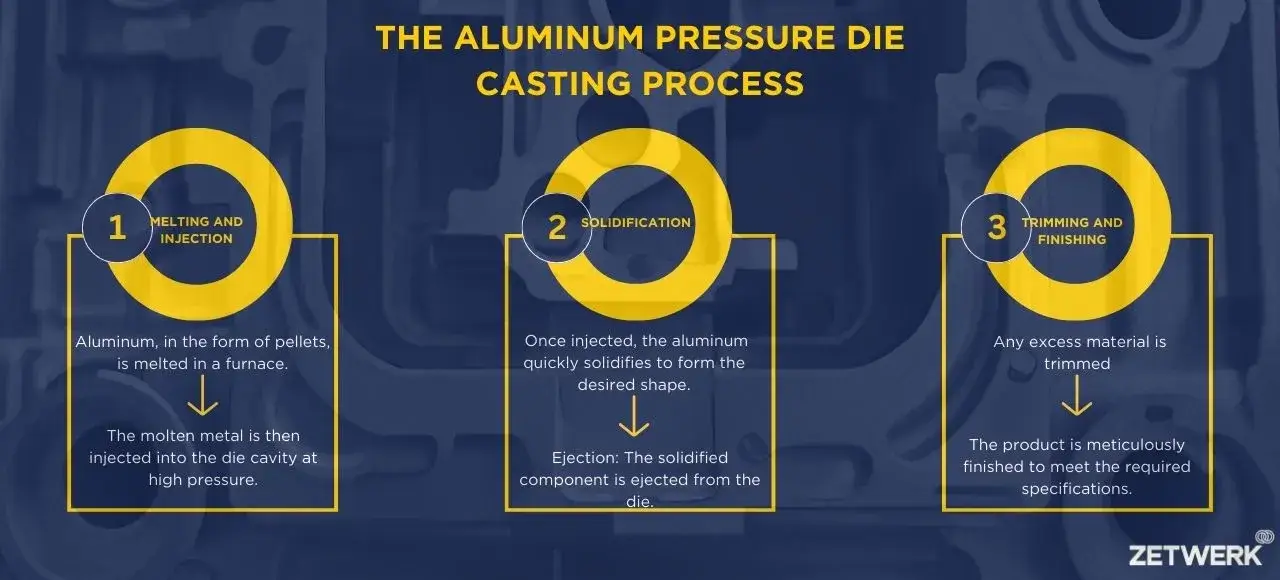
- Melting and Injection: Aluminum, in the form of pellets, is melted in a furnace. The molten metal is then injected into the die cavity at high pressure.
- Solidification: Once injected, the aluminum quickly solidifies to form the desired shape.
Ejection: The solidified component is ejected from the die.
- Trimming and Finishing: Any excess material is trimmed, and the product is meticulously finished to meet the required specifications.
Applications and Industries
The versatility of aluminum pressure die casting is exemplified by its extensive range of applications. It caters to a myriad of industries, each benefiting from its unique attributes.
- Automotive Industry
In the automotive sector, aluminum pressure die casting plays a pivotal role in the creation of engine components, transmission housings, and structural parts. The lightweight nature of aluminum is a boon for improving fuel efficiency, without compromising on strength and durability.
- Aerospace Industry
In aerospace, precision and lightweight components are essential. This technique is used to manufacture critical parts, such as turbine blades and structural components, where the balance of weight and performance is crucial.
- Electronics Industry
In the electronics industry, where miniaturization and precision are paramount, aluminum pressure die casting is the method of choice for creating intricate housings and heat sinks.
Comparing Aluminum Pressure Die Casting with Other Methods
While there are alternative casting techniques available, aluminum pressure die casting stands apart for several reasons:
- Precision: As discussed, this method excels in delivering high-precision components, something not easily achievable with other casting methods.
- Surface Finish: The surface finish of components produced through this process is exceptionally smooth and free from defects.
- Reduced Waste: The high-pressure aluminum die casting method minimizes material waste, making it an environmentally responsible choice.
Environmental and Cost Considerations
Sustainability is a growing concern in modern manufacturing. Aluminum pressure die casting is an environmentally friendly process, owing to its efficiency and the reduced material waste it produces.
Additionally, this method is highly cost-effective in the long run. While the initial tooling costs may be higher, the reduced material waste, energy efficiency, and the ability to produce high-pressure aluminum die casting components ultimately result in significant cost savings.
Key Takeaways
The aluminum pressure die casting is a powerhouse in modern manufacturing, setting itself apart with precision, versatility, and sustainability. The ability to produce high-pressure aluminum die casting components for various industries while maintaining strict tolerances, makes it the method of choice for those seeking excellence in metalworking. As the industry continues to innovate and adapt to future demands, it’s safe to say that aluminum pressure die casting will remain at the forefront, solidifying its reputation as a cornerstone of the manufacturing world.
Zetwerk offers comprehensive manufacturing services including aluminum pressure die casting along with other capabilities such as CNC machining and forging. To learn more about aluminum pressure die casting or related topics, visit Zetwerk Knowledge Hub for informative articles and expert insights.




FAQs
High-pressure aluminum die casting differs from sand or investment casting by injecting molten aluminum into steel or hard alloy molds at high pressure and temperature. This method allows for tight tolerances, excellent surface finishes, and rapid production compared to traditional methods.
When designing parts for aluminum pressure die casting, businesses should consider factors such as application requirements, appearance specifications, assembly methods, cost analysis, material selection based on desired properties like weight and conductivity, and draft angles for easy ejection of castings from dies.
Aluminum pressure die-cast parts find applications in various industries such as automotive manufacturing due to their lightweight nature and precise shapes with tight tolerances. Other sectors benefiting include aerospace operations where heat resistance is required and infrastructure development where durability is essential.
The key benefits of aluminum pressure die casting in automotive manufacturing are its weight reduction leading to fuel efficiency and cost-effective transportation, precise shapes with tight tolerances ensuring accurate components, corrosion resistance for durability, and high operating temperatures suitable for engine components.
Yes, aluminum pressure die casting can meet specific requirements by selecting appropriate alloys that offer desired mechanical properties. It also allows for weight reduction due to its lightweight nature, making it suitable for applications where weight is a concern.