Aluminum die casting is a versatile process that produces complex shapes with accuracy. Molten aluminum injected into molds under high pressure creates parts with excellent mechanical properties, high strength-to-weight ratio, corrosion resistance, and dimensional stability. Used in various industries like automotive, electronics, aerospace, and more. Material selection and mold design are crucial for optimal components.
Advantages of Aluminum Die Casting Parts
Aluminum die-casting parts offer numerous advantages for high-performance manufacturing applications. These advantages make them a preferred choice across various industries:
- Cost-effectiveness: Aluminum die casting allows for high-volume production capabilities, reducing per-unit costs significantly.
- Excellent surface finish: Die-cast aluminum parts have a smooth and aesthetically pleasing surface finish without the need for additional machining or finishing processes.
- Good tensile strength: Aluminum alloys used in die-casting provide excellent tensile strength and structural integrity to the components.
- Low-cost raw materials: The raw materials required for aluminum die casting are relatively inexpensive compared to other metals.
- Lightweight property: One of the key advantages of aluminum die-casting parts is their lightweight nature. This makes them ideal for applications requiring weight reduction without compromising performance.
- Thermal conductivity and electrical conductivity: Aluminum alloys exhibit excellent thermal conductivity and electrical conductivity, making them suitable for industries that require efficient heat dissipation or electrical conduction.
Applications of Aluminum Die Casting Parts in the Automotive Industry
The automotive industry relies on aluminum die casting for high-performance manufacturing. These parts enhance fuel efficiency, cut emissions, and boost vehicle performance. Some specific applications include:
- Engine blocks: Aluminum die-cast engine blocks offer lightweight alternatives to traditional cast iron blocks while maintaining the required strength and efficiency
- Transmission housings: Die-cast aluminum transmission housings provide a lightweight solution with excellent dimensional stability and durability.
- Steering knuckles: Aluminum die casting enables the production of steering knuckles that are strong, lightweight, and capable of withstanding high stresses.
Applications of Aluminum Die Casting Parts in the Electronics Industry
The electronics industry relies on precise aluminum die casting for quality components used in various devices. These parts ensure durability, structural integrity, and protection against shock and vibration. Key uses include:
- Smartphones: Aluminum die-casting parts are used in smartphones for their structural strength, durability, and aesthetic appeal.
- Laptops: The lightweight yet robust nature of aluminum die-casting parts makes them ideal for laptop casings to withstand day-to-day use.
- Cameras: Precise and durable camera components produced through aluminum die casting guarantee optimal image quality and long-lasting performance.
- Audio equipment: Aluminum die casting provides the necessary rigidity for audio equipment components while maintaining a compact design.
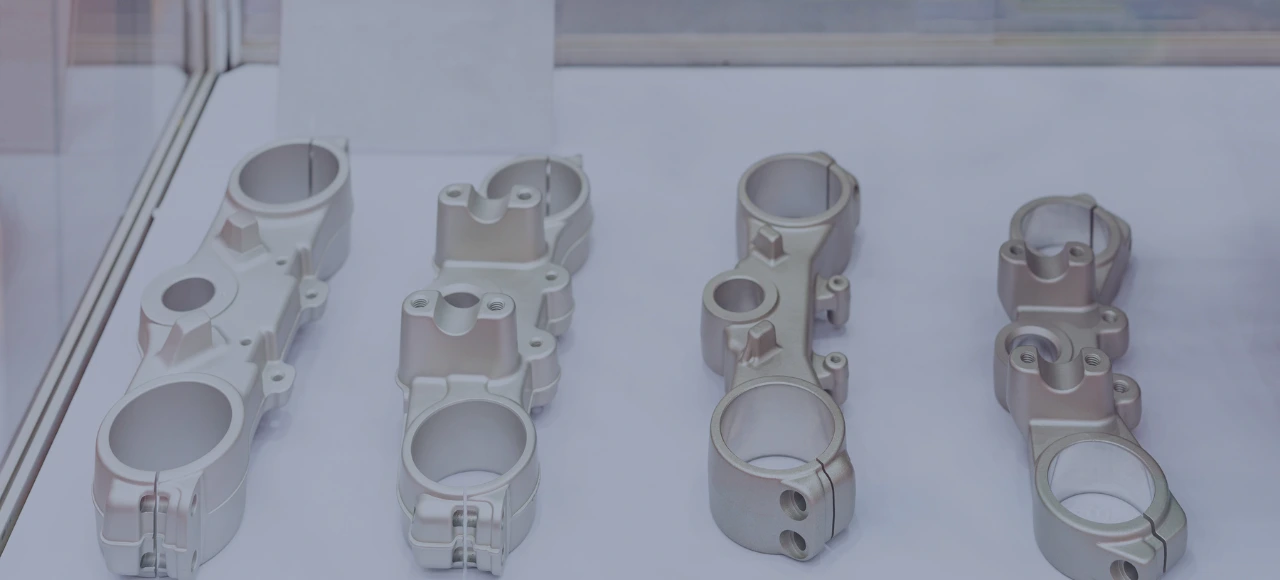
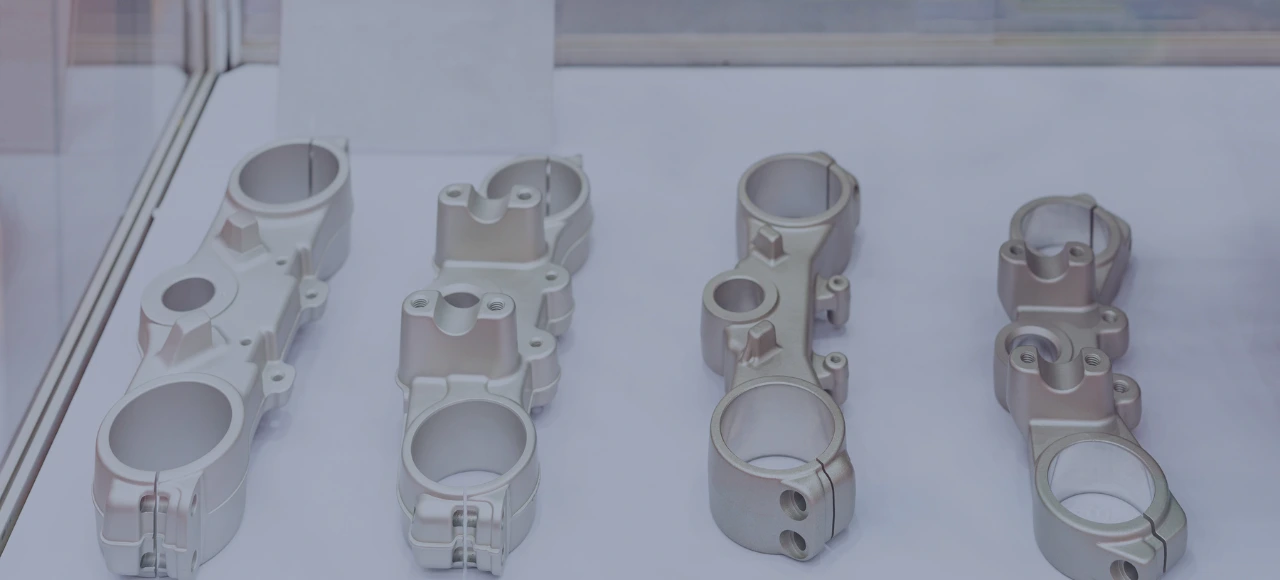
Applications of Aluminum Die Casting Parts in Aerospace Industry
The aerospace industry utilizes aluminum die casting for critical components, enhancing fuel efficiency, weight reduction, and flight performance. Key applications include:
- Aircraft engine parts: High strength-to-weight ratio in aluminum die casting ensures optimal performance and fuel efficiency for aircraft engines.
- Landing gear components: Lightweight die-cast aluminum parts reduce overall aircraft weight, making them ideal for landing gear.
- Structural parts: Aluminum die casting produces strong, durable components capable of withstanding the demanding conditions of aerospace environments.
Applications of Aluminum Die Casting Parts in Other Industries and Material Selection
Apart from automotive, electronics, and aerospace industries, aluminum die casting finds various applications:
- Industrial equipment: Pumps, valves, compressors, and other machinery use aluminum die casting for its strength and durability in harsh conditions.
- Lighting: Aluminum die casting helps dissipate heat efficiently in lighting fixtures due to its excellent thermal conductivity.
- Medical equipment: Surgical instruments, imaging devices, and patient monitors benefit from aluminum die casting’s high strength and biocompatibility.
- Telecommunications: Base stations, antennas, and connectors use aluminum die casting for its thermal conductivity and lightweight properties.
Aluminum alloys like A380, A390, A360, A413, ADC-12, and ADC-1 are popular choices for die casting. Careful consideration of requirements like strength, corrosion resistance, and conductivity ensures suitability for diverse applications.
Key Takeaways:
Aluminum die casting: a key advantage for high-performance manufacturing in various industries. From automotive to electronics, aerospace to industrial equipment, its parts have superior properties – lightweight, corrosion resistance, stability, and conductivity. Choosing materials and molds carefully is vital for desired performance. Precise complex shape creation makes aluminum die casting pivotal for high standards. Explore more at Zetwerk’s Knowledge Hub.
Zetwerk offers a range of manufacturing services for high-performance applications. From precision machining to fabrication, casting, and forging, Zetwerk can cater to your specific requirements. Explore Zetwerk’s Knowledge Hub for comprehensive information on aluminum die-casting parts and more.




FAQs
Aluminum casting parts have broad industrial uses – automotive, electronics, aerospace, industrial equipment, lighting, medical equipment, sports equipment, and telecommunications – thanks to their remarkable mechanical properties and versatility.
Customized aluminum die-casting parts are manufactured through the process of injecting molten aluminum into molds under high pressure. The molds are designed to create complex shapes with high accuracy and repeatability.
The cost of aluminum die casting is determined by factors such as initial tooling costs, the complexity of part design, the volume of production, labor costs, and material selection. Each factor contributes to the overall cost calculation.
Yes, aluminum die-cast parts can be machined and finished further. Processes like drilling, tapping, milling, grinding, polishing, anodizing, powder coating, or chemical film treatments can be applied based on specifications.
Aluminum die-cast parts excel in mechanics and performance for high-performance uses in diverse industries. However, they face size restrictions compared to processes like steel fabrication or CNC machining.