When you’re on the hunt for aluminum die casting companies, there are likely many things to consider. One of the first steps in finding a partner is to look at the numbers. For example, what die casting services are they currently providing, how long have they been in business, and how much experience do they have in their field?
Selecting a single supplier offering only one service type might not provide the best solution for your business. Instead, working with a team that offers solutions to complex manufacturing issues in multiple industries and fields is more likely to meet your needs. The decision will come down to determining which aluminum die casting company provides the best and most cost-effective alternatives so that you can grow your business profitably.
The Popularity Of Die Casting
According to a new study report from Grand Wire Research, the global aluminum die casting market was valued at USD 69.36 billion in 2021 and is expected to grow at a compound annual growth rate (CAGR) of 5.5% from 2022 to 2030. The growing demand for aluminum drives this market to die castings from various industries, such as automotive, electrical and electronics, and construction.
Some of the reasons for its popularity include:
- High production speed: Die casting is a fast and efficient process that is capable of producing high volumes of parts quickly and accurately.
- Good dimensional accuracy and surface finish: Die casting makes parts with good dimensional accuracy and surface finish, which reduces the need for additional machining and finishing.
- Cost-effective for high volumes: Die casting is generally more cost-effective for producing incredibly complex parts than other manufacturing processes.
- Versatility: Die casting can create a wide range of parts and components, including simple and complex shapes, and can be used with various metals, including aluminum, zinc, brass, and bronze.
- Strong and durable: Die castings are typically solid and stable, making them suitable for various applications.
Die Casting Process
The process involves the following steps:
- Design and preparation (Clamping): The first step in the die casting process is to design the part and create a die (mold) that will be used to produce the part. The die is typically made of steel and consists of two halves designed to create the desired shape of the part.
- Injection: The next step is to melt the metal, typically aluminum, zinc, brass, or bronze, and pour it into a crucible or holding furnace. The molten metal is then poured into a cold or hot chamber, depending on the die casting process used, and injected into the die using a plunger or hydraulic ram.
- Cooling: As the molten metal cools and solidifies, it takes on the shape of the die.
- Ejection: Once the metal has cooled and solidified, the die halves are separated, and the part is ejected.
- Trimming and finishing: The final step in the die casting process is to trim any excess material from the part and perform additional finishing operations, such as deburring, polishing, or painting.





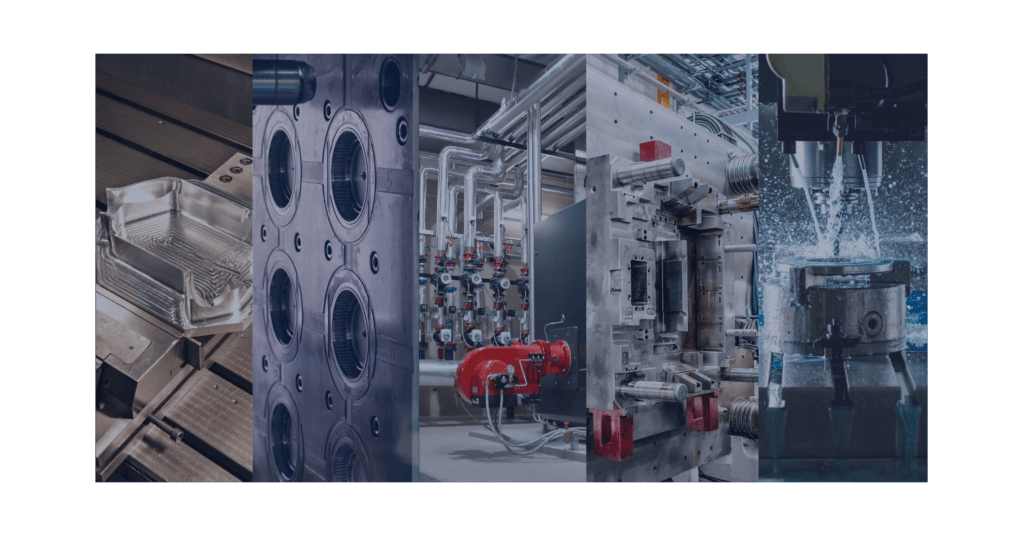
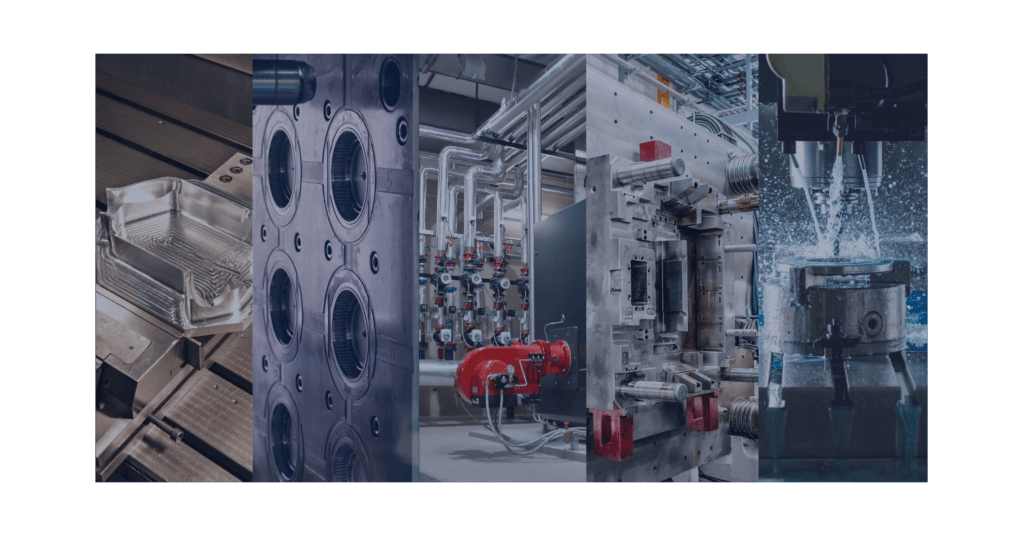
Aluminum Casting Alloys
The three metals most widely used in casting are zinc, aluminum, and magnesium. They have a wide range of mechanical properties and can be used to make just about anything. They also withstand high temperatures, are fully recyclable and are reasonably priced. They do have the following:
- Corrosion-resistant
- Strong and hard
- Excellent heat conduction
- Good processing properties
- Electrical conductivity
- EMI/RFI Shielding
Each casting alloy has its properties and advantages. Die-casting is a good option because it allows you to choose which metal to use.
What Are The Uses Of Aluminum Die Casting In Industries?
Aluminum die casting is used in a wide range of industries and applications, including:
- Automotive: The automotive industry uses aluminum die casting to produce engine blocks, transmission cases, and wheels.
- Aerospace: Die casting produces lightweight, high-strength aluminum parts used in the aerospace industry to create aircraft and aerospace components.
- Consumer products: Aluminum die casting produces consumer products such as appliances, electronics, and furniture.
- Industrial equipment: Aluminum die casting produces parts for various industrial equipment such as pumps, valves, and compressors.
- Construction: Aluminum die casting produces door handles, window frames, and curtain wall systems.
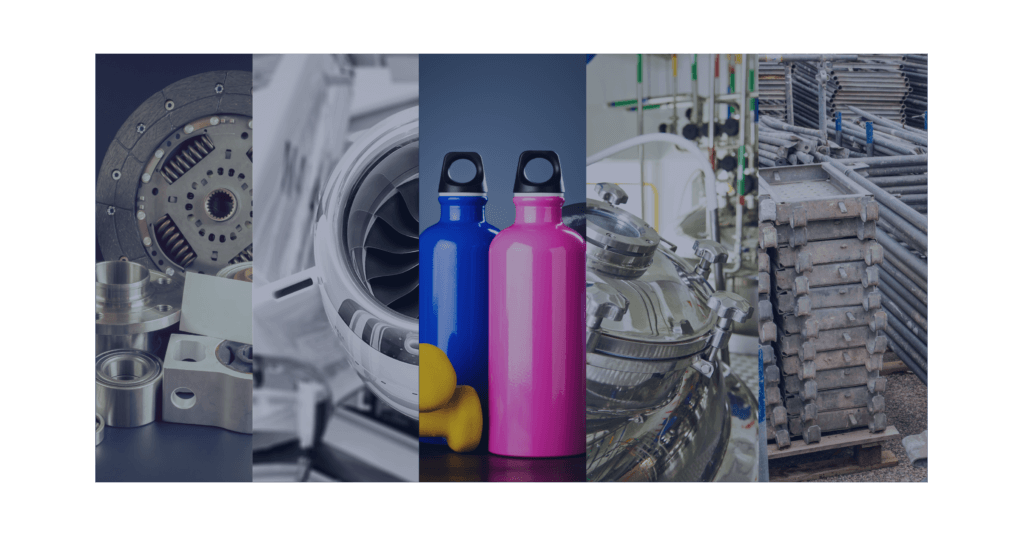
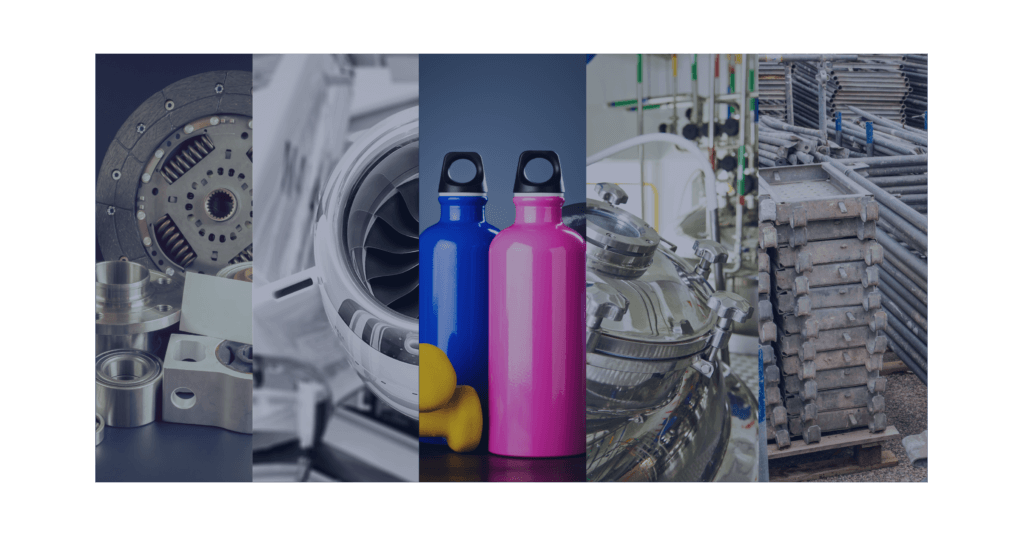
If you need a go-to die castings and prototype supplier, turn to Zetwerk. We have the range, expertise, and high-quality standards that any project demands. Zetwerk is a US-based aluminum die casting company and has been in the business for many years. Our services include precision machining, EDM wire cutting, injection molding, stamping, CNC machining, and complex die casting. We offer aluminum and zinc die castings; therefore, you can always choose the best material for your project. It’s evident that with our expertise in the field and state-of-the-art technologies, Zetwerk is the premier choice for aluminum die casting.




