Maximizing efficiency in CNC machining is crucial for manufacturers. It saves time and cost by reducing production cycles and optimizing tooling setups. Efficient CNC machining enhances productivity, ensures consistent quality, and provides a competitive edge in the market. It enables resource optimization, minimizing material waste and energy consumption. By focusing on efficiency, CNC machine shops help to achieve faster production times, cost-effective pricing, and sustainable manufacturing practices.
Know About Maximising Efficiency In CNC Machining: Tips and Best Practices
Understanding CNC Machining
CNC machining is a computer-controlled manufacturing process that produces custom-designed parts with exceptional precision and consistency. Using computer-aided design (CAD) software and computer-aided manufacturing (CAM) instructions, CNC machines cut, shape, and finish raw materials to create intricate and complex components. CAD is used for designing the parts and CAM is used for generating the tool paths and machine instructions. This technology has revolutionized the manufacturing industry, offering greater flexibility, versatility, and accuracy than traditional machining methods.
CNC (Computer Numerical Control) machining is a precise and automated manufacturing process. It utilizes computerized controls and specialized machinery to produce custom-designed parts and components. Unlike conventional machining methods, which rely on manual operation, CNC machining relies on computer programs and instructions to guide the machine’s movements. These programs are typically created using CNC-specific programming languages such as G-code or M-code.
A typical CNC machine consists of a control unit housing the computer and software and a machine tool with various cutting tools. The CNC system guides the machine’s movements in multiple axes (X, Y, Z) with the help of precision mechanisms like ball screws and linear guides. Sensors and feedback mechanisms ensure accurate positioning and measurement.
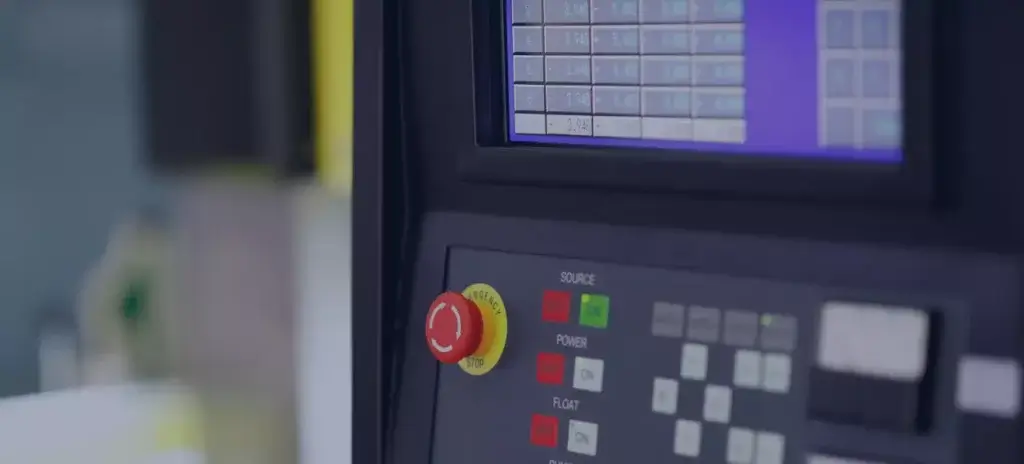
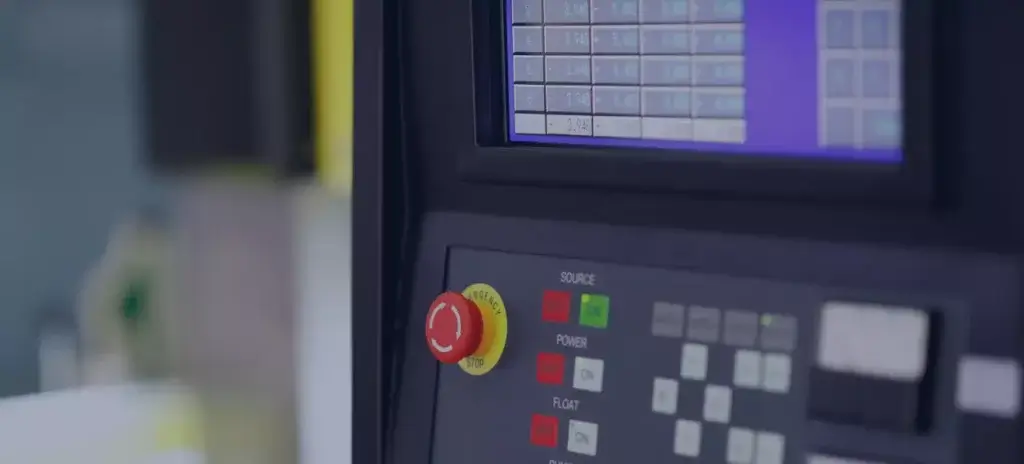
CNC machining offers distinct advantages over conventional machining methods.
- They are highly efficient, improving productivity with continuous operation, automated tool changes, and optimized cutting parameters.
- It delivers precise and consistent results, thanks to computer-controlled movements and advanced measuring systems.
- CNC machining ensures reproducibility, saving time and costs through faster production cycles, reducing material waste, and minimizing rework.
- CNC machines are flexible, can work with various materials, and perform complex operations.
Tips for Maximizing Efficiency in CNC Machining
Efficiency is crucial in CNC machining to ensure optimal productivity and cost-effectiveness. Manufacturers can maximize efficiency and improve their CNC machining processes by implementing the following tips.





Optimise Tooling and Setup
Choosing the right cutting tools and materials is essential for efficient CNC machining. Consider factors such as the material being machined, the desired surface finish, and the cutting speeds required. High-quality tools with appropriate coatings and geometries can improve cutting performance and life, reducing downtime for tool changes.
Ensure proper tooling setup and alignment to maximize efficiency. Check that tools are securely mounted and properly tightened. Verify that tool lengths, diameters, and offsets are accurately entered into the CNC program. Proper alignment of tools and workpieces helps maintain precision and prevents errors during machining.
Programming and Simulation
It is essential to employ efficient CAD/CAM programming techniques that optimize tool paths using advanced features like toolpath optimization algorithms, adaptive strategies, and efficient tool change sequences to maximize efficiency in CNC machining. It minimizes unnecessary movements and tool changes, reducing machining time.
Additionally, simulation software enables precision machined parts manufacturers to validate the machining process virtually, identifying, and rectifying errors, collisions, and inefficiencies before production. By leveraging these tools, manufacturers can optimize efficiency, enhance productivity, and ensure the safety and quality of the machining process.
Material Optimization
Efficient material utilization is crucial for maximizing efficiency in CNC machining. One way to achieve this is by carefully selecting stock materials that closely match the required part dimensions, minimizing excessive material removal, and reducing waste. Additionally, implementing nesting and clustering techniques can optimize material utilization when machining multiple parts from single stock material.
By arranging parts closely together to minimize unused space (nesting) and grouping similar parts for efficient machining (clustering), manufacturers can maximize the use of each stock material, resulting in improved efficiency and cost savings. These practices contribute to reducing material waste and enhancing overall production efficiency.
Process Optimization
To maximize efficiency in CNC machining, fine-tune cutting parameters such as speed, feed rate, and depth of cut based on material and part requirements. Implement advanced strategies like high-speed and multi-axis machining to reduce cycle times and minimize setup changes. These optimizations enhance efficiency, improve tool life, and boost overall productivity.
Quality Control & Inspection
Efficient quality control is crucial in CNC machining. Implement in-process monitoring and inspection techniques using sensors and probes to measure critical dimensions and verify tolerances. Real-time tracking enables immediate corrective actions, minimizing defects and rework. Implement statistical process control (SPC) to analyze production data, identify trends, and detect process variations, leading to minimizing defects, reduced scrap, and improved efficiency in CNC machining.
By embracing these strategies, manufacturers can unlock the full potential of CNC machining, streamline their operations, and achieve higher efficiency, productivity, and profitability. The initial investment in implementing these strategies will yield long-term benefits and position businesses for success in the dynamic manufacturing industry.
Takeaways
Maximizing efficiency in CNC machining is of paramount importance for machined parts manufacturers. It offers several key benefits that contribute to overall success in the industry.
- Firstly, optimizing efficiency helps reduce production costs. Precision CNC machine parts manufacturers can significantly decrease expenses associated with raw materials, energy consumption, and tool replacement by minimizing material waste, streamlining processes, and optimizing tooling and setup.
- Secondly, maximizing efficiency leads to improved productivity. By reducing cycle times, eliminating unnecessary movements, and adopting advanced machining strategies, manufacturers can increase their production capacity, meet tight deadlines, and take on more projects.
Efficiency-driven approaches also enhance product quality. Manufacturers can ensure the final parts’ accuracy, precision, and consistency by fine-tuning cutting parameters, implementing quality control techniques, and utilizing simulation software for process validation. Moreover, maximizing efficiency allows manufacturers to stay competitive in the market. It enables them to offer faster turnaround times, lower costs, and higher quality products, meeting customers’ demands and seeking reliable and efficient CNC machining services.
Maximizing efficiency in CNC machining is vital to achieving cost savings, improving productivity, enhancing product quality, and remaining competitive. It enables manufacturers to streamline operations, optimize resources, and deliver superior results, ultimately driving their success in the dynamic manufacturing industry.
For custom machining services, please feel free to contact Zetwerk.





CNC Machining FAQ’s
CNC machine shops like Zetwerk provide precision machining services using computer numerical control (CNC) technology, producing custom parts and components according to your specifications. They offer efficient and accurate manufacturing solutions for various industries, benefiting you with their expertise and capabilities.
Precision machined parts are highly accurate components made with tight tolerances using advanced machining techniques. They are crucial in industries like aerospace and automotive, ensuring precise fit and optimal performance in the final product.
Few examples of precision machines are CNC milling, CNC turning, grinding, laser cutting, water jets, EDM (Electrical Discharge Machining), Coordinate measuring machines (CMM), and more.