The manufacturing world continually evolves, fueled by technological advancements and the quest for optimal efficiency. Among the notable shifts in this landscape is the rise of component manufacturing in regions like China, particularly in precision CNC (Computer Numerical Control) machining. This technology and the growing significance of precision electronic components manufacturing companies underscores the industry’s commitment to innovation, quality, and precision.
The Synergy of Electronic Components and CNC Machining
CNC machining, a marvel of modern manufacturing technology, allows computer-controlled machines to perform myriad tasks – from cutting to milling. Although this technology has roots in the past, its adoption and refinement in places like China have been revolutionary. This surge is not accidental but the result of several contributing factors:
- China’s Drive for Modernization: The ambitious “Made in China 2025” strategic plan outlines the nation’s vision to become an advanced manufacturing behemoth. Investing in technologies such as CNC machining is pivotal to this dream.
- Skilled Labor Availability: A vast, well-educated workforce equipped with the technical prowess to handle sophisticated machines has facilitated the large-scale adoption of precision CNC machining.
- Consumer Demand for Quality: The global consumer’s rising expectation for high-quality products necessitates manufacturing processes that offer utmost accuracy and consistency.
Bridging the Gap: Precision Electronic Components and CNC
While CNC machining excels in creating parts with intricate details, the electronic sector is an arena where precision is non-negotiable. This synergy is evident in several industries:
- Automotive Sector: CNC machining supports the automotive industry’s drive for lightweight and efficient components, catering to the rising demand for eco-friendly vehicles.
- Aerospace Domain: In an industry where precision is paramount for safety, CNC machining ensures the manufacture of vital components, from turbine blades to structural parts.
- Medical Field: The delicate nature of medical devices requires the utmost accuracy, and CNC machining offers the precision needed for tools like surgical instruments and implantable devices.
- Electronics Sector: From semiconductor devices to circuit boards, the electronics industry leans heavily on the accuracy and precision that CNC machining and precision electronic components manufacturing companies offer.
The Road Ahead: CNC Machining and Electronic Component Manufacturing
The commitment to adopting and optimizing CNC machining indicates the country’s dedication to pushing the boundaries of what’s possible in manufacturing. As the thirst for high-quality products amplifies, the symbiotic relationship between CNC machining and precision electronic component manufacturing will grow stronger.
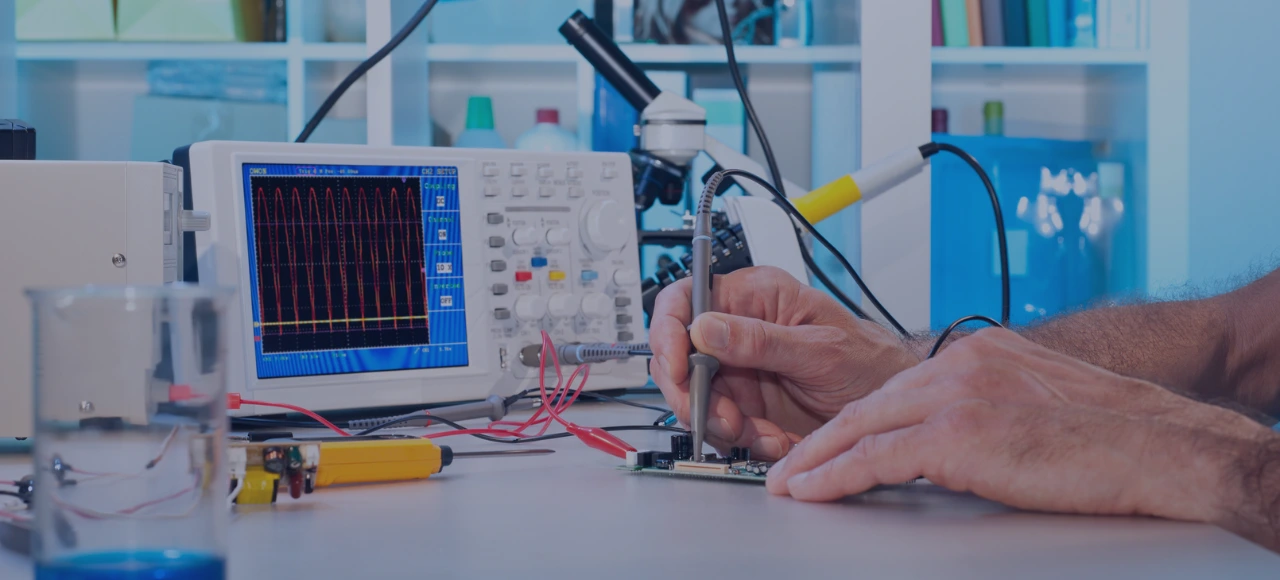
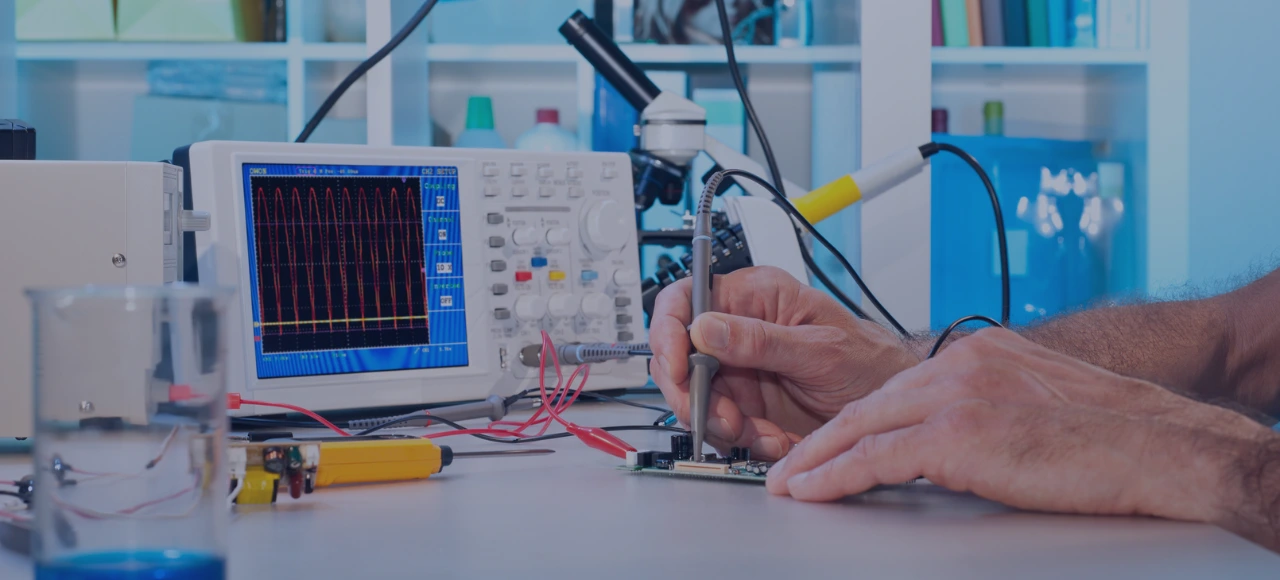
Adapting to the Future: The Integral Role of Precision in Electronics
In today’s era of advanced technology, the quality and precision of electronic components are paramount. The role of a precision electronic components manufacturing company is pivotal in addressing this demand. Delving deeper into the importance of precision manufacturing, we uncover insights that set the trajectory for the future of electronics.
The Miniaturization Revolution
Miniaturization stands as one of the cornerstones of modern electronic design. Devices are shrinking, and with this comes the imperative need for components to be even more precise. Consider a device like a smartphone. It contains billions of transistors, each minuscule. Achieving such intricate designs requires impeccable manufacturing techniques.
The Environmental Perspective
In our progressive stride toward environmental sustainability, the manufacturing processes adopted by industries come under scrutiny. Minimizing waste becomes not just an economic goal but an environmental one. Herein lies the value of precision manufacturing. Waste is drastically reduced by ensuring that each component is made accurately, promoting efficient resource utilization. A responsible precision electronic components manufacturing company emphasizes such eco-centric approaches.
Safety and Reliability
Specific sectors, like aerospace and medical equipment, demand absolute reliability. In such domains, there’s zero tolerance for malfunction. The need for components to operate seamlessly and consistently becomes non-negotiable. The emphasis on precision in electronic component manufacturing ensures this level of reliability, a testament to the industry’s commitment to safety and excellence.
The Economic Perspective
Efficiency in production, reduced errors, and avoidance of recalls are pivotal from an economic standpoint. Precision in electronic component manufacturing minimizes potential financial pitfalls, fostering better profit margins and competitive pricing. In this context, the company is a beacon of economic efficiency in the electronics sector.
Harnessing Advanced Technologies
Technologies at the frontier of modern innovation, such as AI, IoT, and quantum computing, have an insatiable demand for precision in their electronic components. These are spaces where minor discrepancies can cascade into major functional issues. An electronic company ensures these emergent technologies operate at peak performance by providing utmost precision, steering the next wave of tech revolutions.
Navigating the Fourth Industrial Revolution with Precision
The Fourth Industrial Revolution (or Industry 4.0) is upon us, reshaping industries with digital technologies—from IoT and blockchain to machine learning. As these technologies continue to forge interconnected manufacturing ecosystems, the precision of every electronic component becomes even more vital. Here’s why.
The Digital Thread and Component Authenticity
Industry 4.0 introduces the concept of a “digital thread”—a communication framework that connects traditionally siloed elements in manufacturing processes and allows for an integrated view of an asset throughout its lifecycle. In this ecosystem, the accuracy and functionality of each electronic component can be tracked. A precision electronic components manufacturing company ensures that each element is built to exact standards and can be authenticated and monitored in real time.
Predictive Maintenance and the Role of Components
Predictive maintenance, empowered by machine learning and real-time data analytics, is becoming a staple in modern manufacturing setups. This involves continuously monitoring equipment to predict when maintenance should be performed. The accuracy of these predictions heavily relies on the precision of the electronic components gathering the data. For instance, a slight variance in a sensor’s readings could lead to misguided maintenance decisions.
Customization and the Need for Scalable Precision
As consumer demands shift towards customization, manufacturing processes must adapt. This often means short production runs of highly customized products. For a precision electronic components manufacturing company, this translates to producing a wide variety of features with the same precision level, ensuring that the quality remains consistent, whether the run of one unit or one million.
In the evolving landscape of electronic component manufacturing, precision and innovation stand at the forefront. As an exemplar in this domain, Zetwerk’s commitment paves the way for a technologically advanced, sustainable, and efficient future. This transformation sets the stage for the next chapter in electronics.




FAQs
CNC machining is paramount in the electronics sector because it provides the accuracy and precision required for manufacturing components used in devices ranging from semiconductor devices to circuit boards.
Industries such as the automotive, aerospace, medical, and electronics sectors heavily rely on the accuracy and precision provided by CNC machining.
As devices shrink, a growing need for even more precise components is needed. For example, smartphones contain billions of minuscule transistors, necessitating impeccable manufacturing techniques to achieve such intricate designs.
Precision manufacturing minimizes waste, promoting efficient resource utilization. This approach has economic benefits and aligns with the push towards environmental sustainability.
These sectors demand absolute reliability, and there’s zero tolerance for malfunction. Precision in manufacturing ensures components operate seamlessly, highlighting the industry’s commitment to safety and excellence.