In the world of component manufacturing and engineering, precision is paramount. CNC-turned components shine as a beacon of excellence when creating intricate parts for various industries. CNC, short for Computer Numerical Control, represents the pinnacle of precision engineering. CNC turned components are intricately designed and manufactured using computer-controlled machines, each programmed with meticulous accuracy. These components are crafted from metals, plastics, and composites, ensuring they meet exacting specifications for diverse industries. In this comprehensive article, we delve deep into CNC turned components, exploring their applications, advantages, and critical role in modern industries.
How Are CNC Turned Components Made?
CNC turned components are manufactured using computer numerical control (CNC) machining processes, specifically CNC turning. CNC turning is a subtractive manufacturing process that creates cylindrical or round-shaped components by removing material from a workpiece. Here’s an overview of how CNC turned components are made:
Design and CAD/CAM Programming
The process begins with the design of the component. Engineers or designers create a detailed CAD (ComputerAided Design) model of the part they want to produce. Once the CAD model is complete, CAM (ComputerAided Manufacturing) software generates the CNC program to control the machining process. This program contains instructions for the CNC machine on moving the cutting tools to shape the workpiece.
Material Selection, Workpiece, and Tooling Setup
The next step is to select the appropriate material for the CNC turned component. Common materials include metals like aluminum, steel, brass, and plastics. A raw material, known as a workpiece or blank, is secured in the CNC lathe machine’s chuck or collet. The chuck holds the workpiece in place while it rotates. The CNC machine has various cutting tools, drills, and inserts. The appropriate tooling is selected and installed in the tool turret or toolpost of the CNC lathe.
CNC Machining
The CNC program is loaded into the machine’s computer, and the machining process begins. The workpiece rotates while the cutting tool moves along its length to remove material and create the desired shape. CNC turning machines can perform various operations, including facing, drilling, threading, grooving, and contouring. The CNC machine’s computerized control system precisely coordinates the movements of the tool, ensuring high accuracy and repeatability.
Quality Control and Secondary Operations
During the machining process, operators may periodically measure the dimensions of the workpiece using precision instruments like micrometers and calipers to ensure it meets the design specifications. Visual inspection is also performed to check for surface finish and any defects.
Depending on the specific requirements of the component, secondary operations such as heat treatment, plating, or coating may be performed after CNC turning to enhance its properties or appearance.
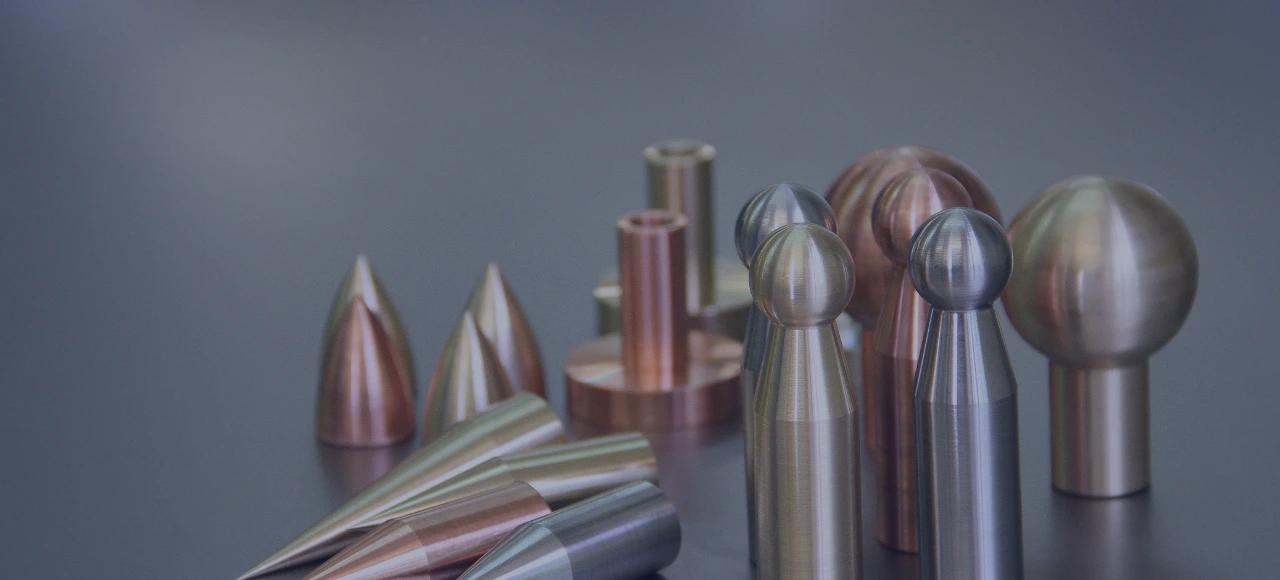
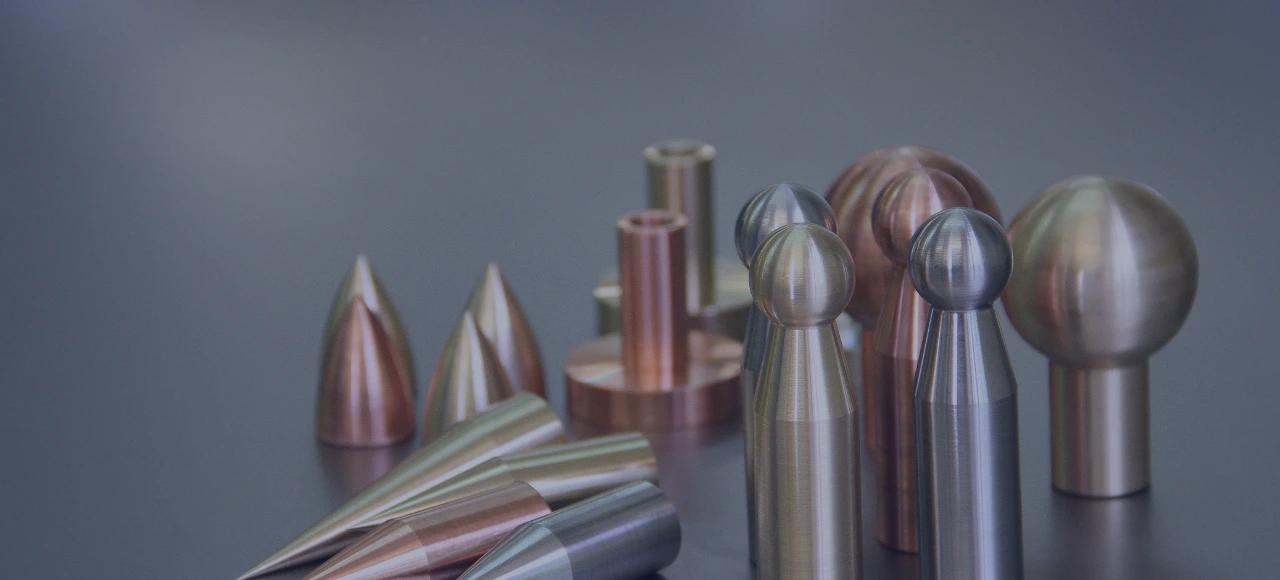
Advantages of Turned Components Parts
Cost-Effective (Save On Energy)
CNC precision-turned components can reduce your operating energy costs by minimizing friction and waste heat, with the ability to generate the same power output while running at lower speeds. Deploying CNC precision turned components within your application can optimize your production processes and increase overall efficiency by improving accuracy and minimizing human error.
High-Quality Parts with a Wide Range Of Materials
Investing in precision-turned parts also gives you greater control over the materials and size configurations of your parts, with a variety of materials, including steel, titanium, aluminum, chromium, or even types of thermoplastic or acrylic – without compromising on quality, accuracy, or lead times. CNC precision production allows manufacturers to optimize their use of precious raw materials, with savings that can be passed on to their customers without compromising the quality and turnaround times for premium products.
Dimensional Accuracy and Reduced Human Error
CNC machining can sustain tight tolerances across any volume’s production requirements, maintaining dimensional accuracy throughout the entire production process. This helps reduce human error and lowers costs by rationalizing the use of materials and minimizing wastage, which can lower the unit cost of CNC turned components across a production run and simplify the inspection and approval process.
Applications of CNC Turned Components
Aerospace Industry
In the aerospace sector, precision is a non-negotiable requirement. CNC turned components find extensive use in aircraft engines, landing gear systems, and avionics. These critical components ensure the safety and reliability of every flight with zero margin for error.
Automotive Engineering
In the automotive industry, efficiency and durability are key. CNC turned components produce engines, transmission systems, and chassis components. Their precision ensures smooth operation and longevity in vehicles.
Electronics and Technology
In our technologically advanced world, electronic devices’ compactness and precision are critical. CNC turned components manufacture connectors, housings, and intricate parts for smartphones, computers, and consumer electronics.
Final Words
CNC turned components are crucial in various industries, ensuring that intricate and accurately shaped parts are consistently produced. The CNC turning process, driven by computer numerical control technology, allows for the creating of components that adhere to tight tolerances and complex designs, meeting the stringent requirements of sectors such as aerospace, automotive, and healthcare. As industries demand excellence in their products, CNC turned components remain indispensable, delivering the reliability and performance necessary for cutting-edge applications.
Leveraging innovative technology and a global network of manufacturing partners, Zetwerk has streamlined the procurement process, ensuring that clients receive top-tier CNC turned components that meet the highest quality and precision standards. Their commitment to excellence and dedication to transparency and efficiency has made Zetwerk a key player in facilitating the production and delivery of CNC turned components, further enhancing the quality and precision of components across industries.




FAQs
CNC turned components are precision-engineered parts created through computer-controlled machining processes. These processes involve rotating a workpiece while a cutting tool shapes it into the desired form.
CNC turned components can be made from a wide range of materials, including metals like aluminum, steel, brass, and copper, as well as plastics and specific composites. The material choice depends on the component’s intended use and requirements.
CNC turned components offer several advantages, including high precision, tight tolerances, excellent repeatability, and the ability to create complex geometries. They are also efficient for producing large quantities of parts with consistent quality.
CNC machining is computer-controlled, whereas traditional machining methods are manual or semi-automated. CNC machining offers greater precision, faster production, and the ability to produce highly complex parts with minimal human intervention.
Zetwerk is a prominent player in the CNC turned components industry, providing a platform that connects clients with a global network of manufacturers. They facilitate the procurement of high-quality CNC turned components, ensuring adherence to strict quality and precision standards, making the sourcing process efficient and transparent for their clients.