Introduction
India’s CNC (Computer Numerical Control) manufacturing industry has experienced remarkable growth and development. This abstract provides.
- An overview of the CNC manufacturing landscape in India,
- Focusing on critical aspects such as its growth trajectory,
- Technological advancements,
- Market trends, and
- The contributions of prominent manufacturers.
This article showcases the impressive capabilities of top CNC manufacturers in India. They specialize in creating intricate and complex components with a reputation for delivering high-quality CNC machined parts. These manufacturers maintain strict quality standards and ensure timely delivery to their clients.
India’s CNC manufacturing sector has grown substantially, driven by increasing demand for precision-engineered components across various countries and sectors, including automotive, aerospace, electronics, and healthcare. Integrating advanced technologies in CNC machines has significantly improved productivity, accuracy, and efficiency, making CNC manufacturing a preferred choice for domestic and international markets. Precision engineering has become the cornerstone of excellence in the fast-paced manufacturing world.
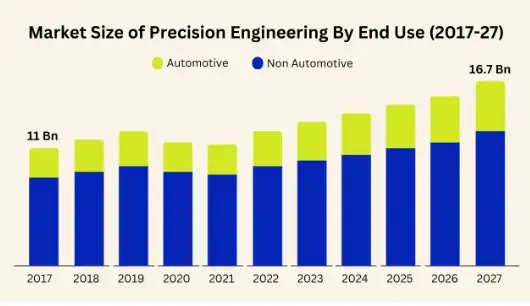
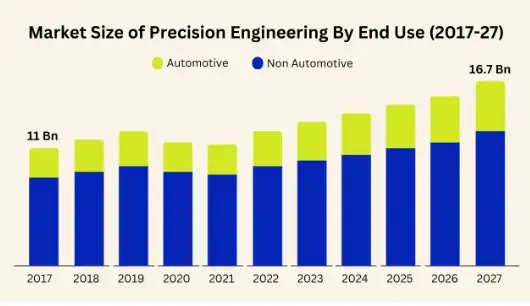
The image showcases the market size of precision engineering for automotive and nonautomotive sectors. The Global Precision Engineering Machines Market Size is expected to reach USD 23.24 billion by 2032, at a CAGR of 6.4% during the forecast period 2023 to 2032. Image Source: Spherical Insights
Expertise in Utilizing Advanced CNC Machines and Software
- The success of CNC manufacturers in India can be attributed to their mastery of utilizing advanced CNC machines and cutting-edge software. These manufacturers invest in state-of-the-art equipment, such as multi-axis CNC machining centers and lathe machines, capable of intricate and complex operations.
- With powerful CAD/CAM software, they translate designs into precise instructions for the CNC machines, ensuring unparalleled accuracy and repeatability in every component they produce.
- India’s leading CNC manufacturers boast a team of skilled engineers and technicians who deeply understand advanced CNC machines and software. These experts stay updated with technological advancements and attend specialized training programs to enhance their knowledge and proficiency that match the global requirements. Their expertise allows them to optimize the CNC machining process, reduce cycle times, and minimize material wastage, resulting in cost-effective production without compromising precision.
Adherence to Strict Quality Control Standards
- One of the hallmarks of top CNC manufacturers in India is their unwavering commitment to quality control. From the selection of raw materials to the final inspection of finished components, every step of the manufacturing process undergoes meticulous scrutiny.
- Manufacturers in India who adhere to international quality standards, such as ISO 9001, ensure their products are flawless and leave no room for compromise. Quality control is of the utmost importance to CNC manufacturers in India, and they take great care to avoid errors.
- Quality assurance teams conduct comprehensive inspections at each stage of the manufacturing process, including material inspection, in-process inspections, and final product checks. Advanced coordinate measuring machines (CMMs) and non-destructive testing techniques ensure the components meet the required tolerances and surface finish standards.
Application of CNC Technology in Diverse Industries
CNC technology has various applications across various industries, including aerospace, automotive, healthcare, and woodworking. It provides improved precision, productivity, and consistency. This article will examine some significant sectors that rely on CNC technology.
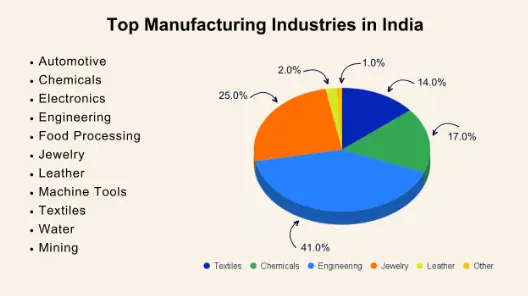
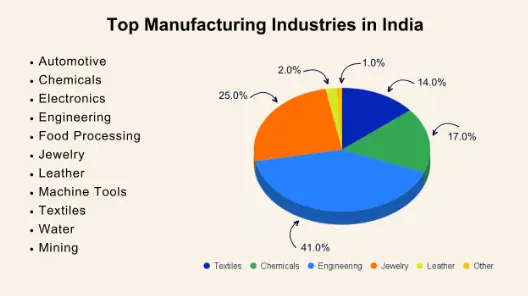
Image source – Researchgate
- Aerospace: Crafting intricate aircraft components with high precision for safety and performance.
- Automotive: Producing engine parts, transmission components, and brakes with consistent quality and reduced lead times.
- Medical: Fabricating custom medical devices and implants tailored to individual patient needs.
- Electronics: Creating printed circuit boards (PCBs) with precise routing and drilling.
- Oil and Gas: Manufacturing durable and reliable drilling tools and equipment.
- Woodworking: Using CNC routers to create intricate furniture and cabinetry designs.
- Mold Making: Ensuring the accuracy of complex molds for efficient mass production of plastic and metal parts.
- Jewelry: Engraving and shaping precious metals and gemstones for detailed designs
- Defense: Producing precision components for weapons and vehicles.
- Construction: Utilizing CNC machines for architectural elements and fixtures, optimizing construction efficiency.
CNC technology drives innovation and enhances productivity across diverse industries, offering unmatched precision and repeatability in manufacturing processes.
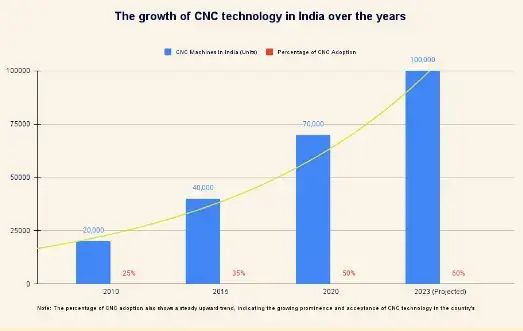
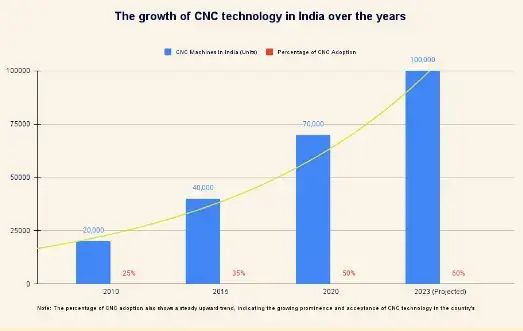
Data Source- Business Wire/Linked-in/Volza
Cost-Effectiveness and Competitive Pricing
India’s CNC manufacturers have earned a reputation for delivering cost-effective solutions without compromising quality. Thanks to their expertise in process optimization, material utilization, and efficient production planning, they can offer competitive pricing to their clients. This combination of quality and affordability has made Indian CNC manufacturers an attractive choice for domestic and international businesses.
- The cost-effectiveness of Indian CNC manufacturers is attributed to various factors. India offers a significant advantage in labor costs, making the manufacturing process more economical without compromising quality.
- Additionally, these manufacturers maintain well-organized supply chains, sourcing materials at competitive prices.
- The emphasis on process optimization and lean manufacturing practices further contributes to their ability to offer competitive pricing to clients without compromising on quality and precision.
Collaboration with Global Companies for Custom Components
Precision Engineering: India’s Global Role in CNC Manufacturing
India is a top CNC manufacturer with expertise in CNC technology. It is a significant contributor to the global market, especially in the export of CNC machined parts. Collaborations with multinational companies have helped India become a global exporter of precision-engineered components.
Crafting Precision through Collaboration
Collaborations between Indian CNC manufacturers and global companies are a testament to India’s capacity for precision craftsmanship. The synergy of technological innovation, skilled labor, and a commitment to delivering intricate designs and high-quality components has sparked a wave of collaborations redefining precision engineering.
Global Industries, Custom Solutions
These collaborations extend across a range of industries, each benefiting from India’s CNC expertise:
- Aerospace and Aviation: The aviation sector relies on precision components to ensure the safety and performance of aircraft. Indian CNC manufacturers collaborate with global aviation companies to create parts that adhere to stringent industry standards.
- Automotive Engineering: The automotive industry demands precision parts that contribute to vehicle performance and safety. Collaborations between Indian CNC manufacturers and global automakers yield components that power innovation in the automotive sector.
- Electronics and Semiconductors: In the fast-paced world of electronics, precision components are critical for technological advancement. Collaborative efforts between Indian CNC manufacturers and global electronics companies fuel the creation of cutting-edge devices.
- Healthcare and Medical Devices: The healthcare sector depends on precision-engineered medical devices and equipment components. Collaborations ensure the availability of high-quality parts that are vital for patient care.
Compliance with International Quality Standards
Precision Aligned with Excellence: Adhering to Global Quality Standards
As India’s CNC manufacturers establish themselves as global exporters of CNC machined parts, their unwavering commitment to complying with international quality standards is paramount to this growth. These standards underscore the reliability, performance, and safety of CNC machined components, reinforcing India’s reputation for precision engineering.
Stringent Adherence to Regulations
Collaborations between Indian CNC manufacturers and global partners are founded on a shared commitment to meet and exceed international quality norms:
- ISO Standards: Indian CNC manufacturers adhere to ISO quality standards, ensuring consistent and reliable manufacturing processes that are recognized and respected worldwide.
- Certification Processes: Components produced in India undergo rigorous certification processes to verify their compliance with industry-specific quality standards.
- Material Selection: CNC manufacturers in India prioritize using materials that align with international quality norms, guaranteeing the durability and reliability of the machined parts.
Trust and Reliability
Compliance with international quality standards serves as the cornerstone of trust between Indian CNC manufacturers and their global collaborators:
- Consistency: Adherence to quality standards ensures that components are produced consistently, maintaining high performance and reliability.
- Risk Mitigation: Quality compliance mitigates risks associated with component failures, ensuring that CNC machined parts meet or exceed expectations.
- Global Recognition: The commitment to international quality standards positions Indian CNC manufacturers as reliable global precision engineering partners.
As India’s CNC manufacturers continue their journey towards becoming global exporters of precision-engineered CNC machined parts, their dedication to collaborative excellence and stringent quality compliance underscores their vital role in the evolving landscape of precision engineering.
Emphasis on Continuous Improvement and New Technologies
Elevating Precision Engineering
In CNC manufacturing, India’s success as a global exporter of precision-engineered parts is driven by a commitment to continuous improvement and integration of new technologies. This focus on innovation has positioned Indian CNC manufacturers at the forefront of the industry, leading the evolution of precision engineering. Indian CNC manufacturers place continuous improvement at the core of their operations. This approach encompasses various facets that contribute to the refinement of CNC manufacturing processes:
- Lean Manufacturing: Adopting lean principles enhances efficiency by eliminating waste and streamlining workflows, resulting in optimized production cycles and reduced lead times.
- Quality Enhancement: Continuous improvement initiatives focus on enhancing the quality of CNC machined parts through rigorous quality control measures, resulting in components that meet or exceed global standards.
- Process Optimization: Manufacturers invest in process optimization, leveraging data-driven insights to fine-tune CNC machining processes for improved precision, reduced errors, and increased productivity.
Integration of New Technologies
In the pursuit of excellence, Indian CNC manufacturers are embracing cutting-edge technologies that push the boundaries of precision engineering:
- Advanced CNC Machines: Investments in state-of-the-art CNC machines enable manufacturers to achieve intricate designs, tighter tolerances, and enhanced production efficiency.
- Automation and Robotics: Integrating automation and robotics in CNC manufacturing optimizes workflows, reduces human error, and accelerates production cycles.
- AI and Machine Learning: Leveraging AI and machine learning algorithms, CNC manufacturers analyze data to identify patterns, optimize processes, and predict potential manufacturing challenges.
- Digital Twin Technology: Digital twin simulations allow for real-time monitoring and analysis of CNC machining processes, enabling rapid adjustments and improvements.
Fostering a Culture of Innovation
The emphasis on continuous improvement and new technologies extends beyond the manufacturing floor, encompassing the entire organization:
- Training and Skill Development: Continuous learning initiatives ensure the workforce remains current with CNC technologies and methodologies.
- Collaboration and Knowledge Sharing: Indian CNC manufacturers collaborate with research institutions, technology experts, and industry peers to stay informed about emerging trends and best practices.
- Innovation Hubs: Establishing innovation hubs and research centers fosters an environment of creativity and experimentation, driving the development of pioneering solutions.
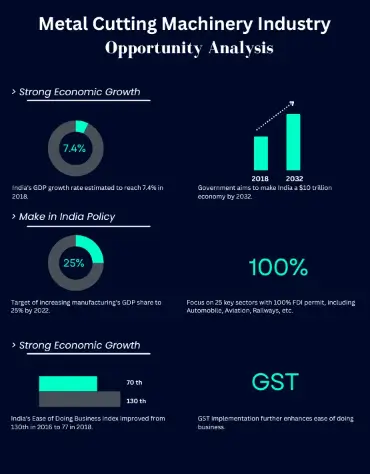
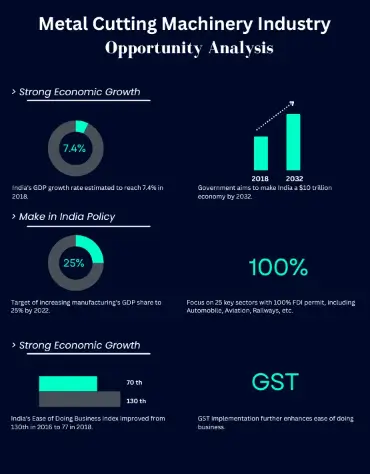
Conclusion
In the world of CNC manufacturing, India’s CNC manufacturers have emerged as trailblazers of precision engineering, showcasing their mastery of cutting-edge technology, commitment to quality, and spirit of innovation. As industries worldwide seek custom components that meet the highest standards of precision, Indian CNC manufacturers have proven their mettle as global leaders.
Zetwerk is a globally renowned industrial solutions provider that offers unmatched reliability, particularly emphasizing utilizing cutting-edge CNC machines and employing rigorous quality control measures. Their expertise in the industry makes them a trusted partner for businesses worldwide, providing top-notch services that meet the highest standards of excellence.
By embracing new technologies, fostering a culture of continuous improvement, and setting the bar for precision engineering, Zetwerk embodies India’s rise as a global exporter of CNC machined parts. With Zetwerk leading the way, the future of precision engineering is bright, with a promise of exceptional quality, innovation, and transformative solutions that will shape industries across the globe.


