Aluminum extrusion channels are widely used for framing, protection, or decoration purposes. The inside radius corners give them their channel shape and hence they are called channel extrusions. Aluminum extrusion profiles are used everywhere. From electrical systems to automotive parts and building materials, aluminum has been used as the primary metal. Two of the biggest sectors that widely use aluminum channels are the architectural and construction industry.
Not only are these aluminum channels versatile and robust for projects, but they save a lot compared to other metals. Traditionally, aluminum channels are known as C and U-shaped channels with uniform thickness and flanges with internal and external radius corners. Let’s understand what aluminum channels are, and how they are used for architectural projects.
Aluminum channel extrusion is a piece of support metals that are shaped to support the structure. Formed into specific shapes like C, J, U, and T, these channels feature equal-sized sizes attached to the ground of the channels with uniform thickness.
Used in a wide range of projects, aluminum channels can be found in home appliances, factories, industrial designs, and more.
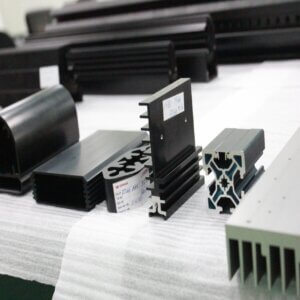
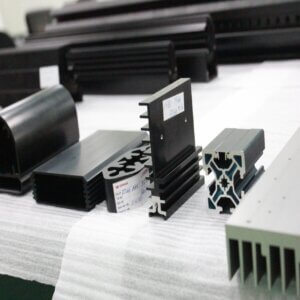
TYPES OF ALUMINUM CHANNELS
Aluminum Hat Channels
With a hat-like appearance, hat-shaped channels are created with two horizontal flanges that reach two vertical dimensions. The thickness is around 5.25 in height and 0.005 with a lightweight and high-strength design. Hat channels include a high strength-to-weight ratio at a low-cost extrusion process.
Applications of Hat Channels
- Hat channels are used to level uneven walls and ceilings
- Protect interior and exterior framing
- Corrosion-resistant and fire-resistant
- Widely used in curtain walls
- Concrete wall applications
U Shaped Aluminum Channels
U-type aluminum channels feature an additional extrusion process. The process includes an extended length of aluminum shaped through a press from the aluminum billet into a cross-section. The wall thickness of U-shaped aluminum channel extrusion is comparatively low, up to 0.03. With a good density, significant thermal expansion, and electrical resistance, U channels are pretty famous for construction projects. The parts of U-shaped channels could be of different dimensions with either short web and long flanges or wide web with short flanges, depending on the requirements.
Applications of U channels
- Framing, slides, and protective edges
- Railing, rims, and decorations
- Architectural projects and window sheets
- Home appliances
- Commercial spaces
C-shaped Aluminum Channels
All the C-shaped channels come in the same variety and size with three basic standards like American, Canadian, and Aluminum Association. The thickness of aluminum c channel extrusion ranges between 0.003 to 0.5000. It could be shaped with various lengths and thicknesses, and the extrusion process is similar to U & J channels. Widely used in architectural projects and factories C shaped channels are readily available due to the higher supply and demand ratio.
Applications of C-shaped channels
- Widely used in railways, buses, and boats
- Railings and posts
- Wood panels are used as store fixtures and framing.





REASONS WHY C-SHAPED CHANNELS ARE GREAT FOR METAL FABRICATION
For fabrication work, C channels aluminum extrusion is considered one of the best options, and here are the reasons why:
Strength to Weight Ratio
The essential requirement of metal fabrication in a project is the strength-to-weight ratio of the material used. Aluminum, as compared to other metals, holds better strength to weight management capability, making it ideal for structural and architectural usage. C-shaped aluminum channels are widely used in structural projects due to their high strength and weight balance ratio.
Heat & Wear Resistance
Most aluminum channels used in construction projects are based on their high rust and corrosion resistance. While other metals quickly get weathered and suffer in extreme cold or heat, aluminum channels can endure and efficiently manage their strength.
Non-Magnetic Features
Aluminum Extrusion C channels are utilized in electrical devices due to their incapability to be affected by magnetic energies, which can cause failures and problems.
Wide Range of Applications
Another reason why C channel extrusion is highly used is the variety of applications it is used for. From architectural projects, railings, and auto parts manufacturers to industrial and residential construction, the aluminum C channel is everywhere, making the structure strong and durable. It is also used for making the design look aesthetically pleasing in various sectors.
WHY ALUMINIUM C CHANNEL EXTRUSION?
Aluminum is a popular metal used in the fabrication sector with a wide variety of usage and extruded products. Since the beginning of construction, metal has been a vital part of commercial and industrial equipment. Its excellent features like appearance, corrosion resistance, and strength capacity have made it one of the best choices for various projects. Aluminum extruded products have been used for durability and reusability for many decades.
Regarding its applications, aluminum is a popular choice for C channel extrusion amongst manufacturers.
- Aluminum is a lightweight material, making it ideal for automotive, industrial devices, and heavy carriers.
- Corrosion resistance and rust-free finish of aluminum extrusion c channels increase the longevity and strength of the structural designs.
- Aluminum holds a high tensile strength.
- The fire and heat resistance quality of aluminum makes it ideal for warmer environments.
Besides all the above reasons, aluminum is used for both architectural work and structure applications. The channels are made from alloy 6063 and 6061-grade aluminum, which is through the most challenging weather conditions.