When it comes to choosing the right aluminum alloy for your manufacturing processes, the options might seem overwhelming. Two commonly used alloys, aluminum 6061 and 6063, often find their way into the spotlight. These alloys possess unique characteristics and applications, making them essential for various industries. In this article, we will explore and dissect the differences between aluminum 6061 and 6063, providing you with a comprehensive understanding of their features and when to utilize each.
Aluminum 6061:
Aluminum 6061, an immensely versatile alloy, is known for its exceptional strength and corrosion resistance. It boasts remarkable machinability, making it a preferred choice in the aerospace and automotive industries. One of its standout features is its weldability, allowing for efficient joining with minimal loss of mechanical properties. This alloy is particularly well-suited for applications where structural integrity is paramount.
Aluminum 6063:
On the other hand, aluminum 6063 is celebrated for its impressive extrudability. This attribute stems from its lower silicon content compared to 6061. This alloy finds its niche in various architectural and decorative applications, as it can be extruded into intricate shapes and profiles. Additionally, 6063 offers a good surface finish and can be anodized, making it a popular choice for visible surfaces that require an aesthetic touch.
Aluminum 6061 vs. 6063: Comparing Strength and Hardness
In the realm of strength and hardness, the scales tip in favor of aluminum 6061. With notable figures of tensile strength reaching around 45,000 psi (310 MPa) and yield strength of approximately 40,000 psi (275 MPa), 6061 outshines 6063. This stark difference establishes 6061 as the prime choice for structural components and load-bearing duties. Its robustness ensures longevity and guarantees reliability in the face of rigorous conditions, making it an indispensable contender for demanding applications.
6061 vs. 6063 aluminum: Machinability and Formability
When it comes to machinability and formability, the spotlight shines on aluminum 6061. Boasting a Brinell hardness of around 95 HB, it takes the lead. This alloy’s exceptional machinability allows for efficient material removal during shaping processes, translating to reduced production times and cost savings. Conversely, if you prioritize malleability and effortless extrusion, consider 6063. With a Brinell hardness of approximately 73 HB, its lower silicon content enhances extrudability, making it the preferred choice for applications demanding intricate shapes and profiles.
6063 aluminum vs. 6061: Corrosion Resistance
In the realm of corrosion resistance, both aluminum 6063 and 6061 stand strong, ensuring durability even in challenging conditions. With a corrosion rate of around 0.15 mm/year, 6063 showcases its protective prowess. Meanwhile, 6061, boasting a slightly higher rate of around 0.20 mm/year due to its elevated copper content, remains stalwart against corrosion. Nonetheless, evaluating your specific application and environmental conditions is paramount to selecting the optimal alloy. A judicious choice ensures your project’s longevity and performance, aligning seamlessly with your industrial demands.
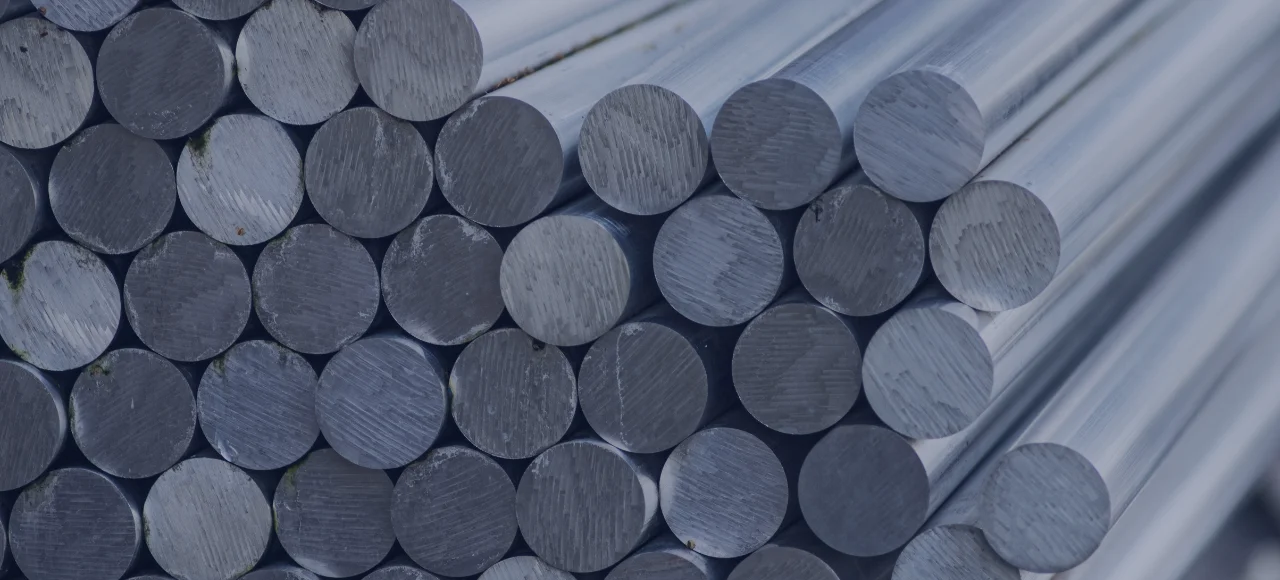
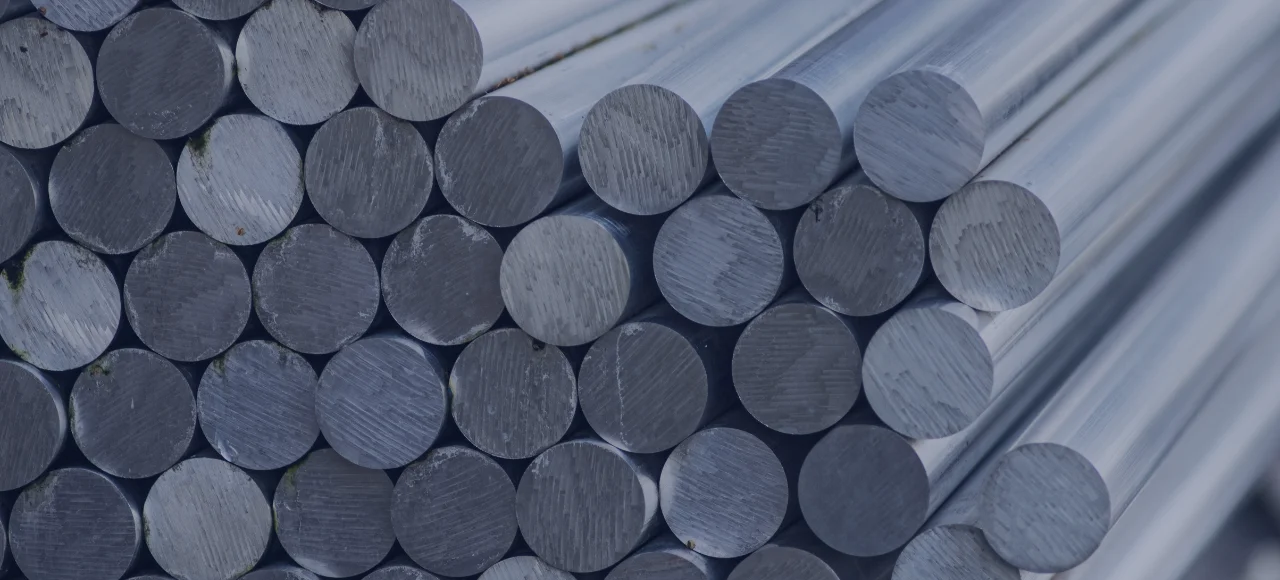
6063 vs. 6061 aluminum: Applications in Specific Industries
Aluminum 6061:
- Aerospace, automotive, and marine sectors benefit from their robustness.
- Superior strength-to-weight ratio and weldability.
- Vital for aircraft components, automotive parts, and marine structures.
Aluminum 6063:
- Flourishes in architectural, interior design, and window/door frame domains.
- Remarkable extrudability crafts intricate shapes for modern architecture.
- Lightweight attributes suit elegant yet functional structures.
Optimizing Your Alloy Choice: Leveraging the Unique Attributes
In the realm of aluminum alloys, the differences between 6061 aluminum and 6063 are substantial and consequential. Aluminum 6061 stands out for its exceptional strength and suitability for structural applications, while aluminum 6063 excels in its extrudability and aesthetic appeal. When deciding between these two alloys, consider the specific requirements of your project, whether it’s robustness or design intricacy that you seek. Understanding the distinctions between aluminum 6061 and 6063 empowers you to make informed decisions in your manufacturing endeavors. As industries evolve and demands diversify, having a clear grasp of alloy characteristics ensures that you choose the right material to optimize your products.
For a seamless integration of aluminum 6061 and 6063 into your manufacturing processes, Zetwerk offers a wide range of capabilities and services tailored to your needs. Explore our aerospace, automotive, and architectural industry expertise to elevate your products to new heights.




FAQs
When it comes to structural applications, aluminum 6061 takes the lead. Its remarkable strength and elevated hardness render it an optimal choice for components requiring enduring robustness.
While automotive manufacturing doesn’t typically lean towards aluminum 6063, this alloy finds its forte in architectural and decorative sectors. Its exceptional extrudability lends itself to crafting intricate designs in these domains.
If intricate shapes and profiles are on your agenda, aluminum 6063 is your ally. With a lower silicon content that enhances extrudability, it excels in bringing complex designs to life.
Both aluminum 6061 and 6063 boast commendable corrosion resistance. However, owing to its copper content, 6061 might display a slightly higher vulnerability to corrosion in specific environments.
Zetwerk stands as a dedicated supporter of industries seeking to harness the potential of aluminum 6061 and 6063. With tailored solutions spanning aerospace, automotive, and architectural applications, Zetwerk ensures seamless integration and optimized performance.