In the fast-paced world of manufacturing processes and supply chains, aerospace and defense industries seek cutting-edge technology and innovative materials to stay ahead. One such revolutionary material that has proven its mettle is the 7075 aluminum bar. Renowned for its exceptional strength-to-weight ratio and impressive mechanical properties, the 7075 aluminum bar has emerged as the go-to material for various applications. In this article, we delve into the characteristics of the 7075 aluminum bar, its applications, and why it has become an indispensable part of the aerospace and defense sectors.
What is 7075 Aluminum Bar?
At the heart of this groundbreaking material is the 7075 aluminum alloy, composed primarily of aluminum, zinc, magnesium, and copper. The precise combination of these elements results in an alloy with exceptional strength and hardness. The “T6” tempering process further enhances its properties, making it one of the strongest aluminum alloys available.
Properties of 7075-grade Aluminum Bar
- Superior Strength: The 7075 aluminum bar boasts a tensile strength of around 83,000 psi (570 MPa), making it comparable to many steel alloys. This remarkable strength enables it to withstand high-stress environments, making it ideal for critical aerospace and defense applications.
- Low Density: Despite its impressive strength, 7075 aluminum remains lightweight due to its low density. This characteristic is a game-changer for the aerospace industry, where weight reduction directly translates to fuel efficiency and increased payload capacity.
- Corrosion Resistance: The alloy’s composition provides excellent resistance to corrosion, ensuring longevity and durability even in harsh environments, such as marine and aerospace applications.
- Machinability: 7075 aluminum bar stock is relatively easy to machine, allowing for intricate designs and precise manufacturing processes. This factor significantly reduces production lead times and costs.
- Heat Treatability: The T6 tempering process increases strength and improves heat treatability. This means the material can be subjected to various heat treatments for further customization without compromising its inherent qualities.
Applications in Aerospace and Defense Industries
Aircraft Components
The aerospace industry relies heavily on 7075 aluminum bars for manufacturing critical components such as wings, fuselage frames, and landing gear. Its lightweight and high strength make it instrumental in achieving fuel efficiency and overall structural integrity.
Missile and Rocket Parts
In defense applications, missile and rocket components utilize 7075 aluminum round bars and flat bars. The alloy’s robustness and resistance to high pressures and temperatures are vital for successful space missions and defense operations.
Armored Vehicles
Armored vehicles require materials that can withstand impact and provide protection to personnel. The 7075 aluminum flat bar meets these demands, offering an excellent combination of strength and weight savings in armored vehicle applications.
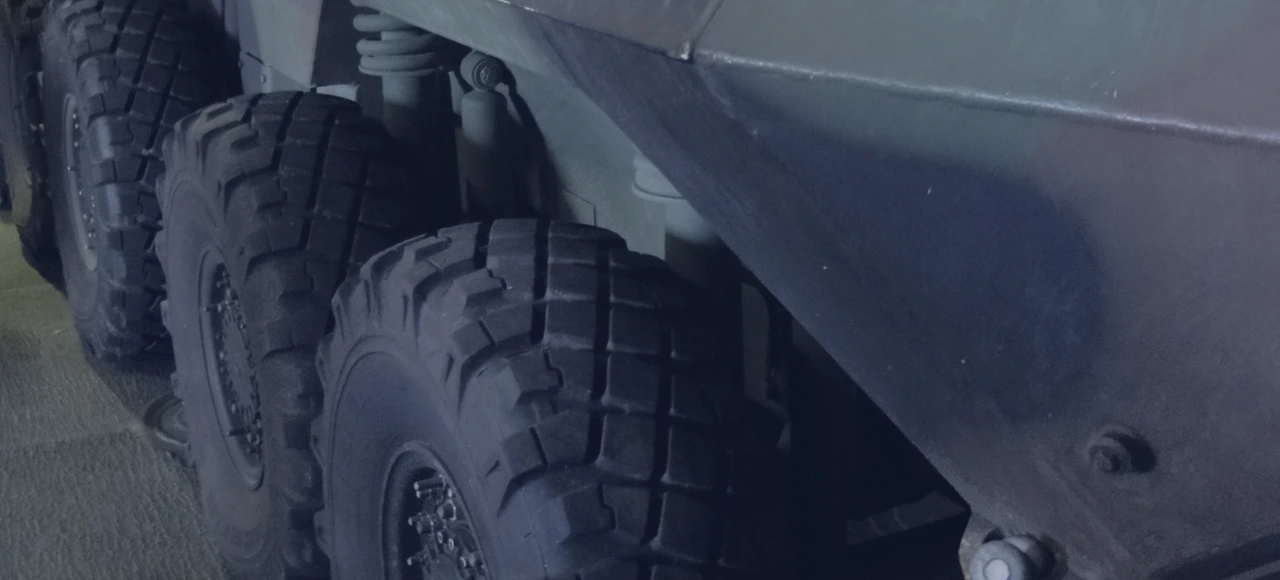
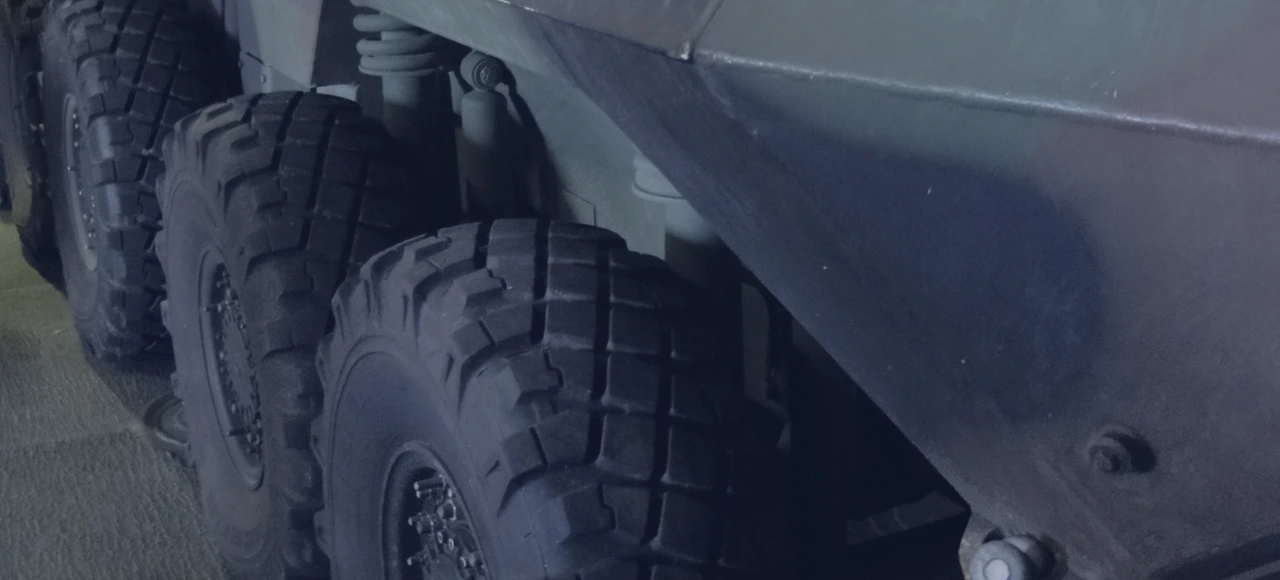
Firearms
Due to its durability and lightweight properties, the 7075 aluminum bar has found its way into manufacturing firearms, particularly in constructing gun frames and receivers.
Marine Equipment
The alloy’s corrosion resistance makes it an excellent choice for marine applications like boat fittings and structures.
Cost of 7075 Aluminum Bar
While the 7075 aluminum bar cost may be relatively higher than some other aluminum alloys, its superior performance and long-lasting properties more than offset the initial investment. The lightweight nature of the material also contributes to lower transportation costs and energy savings during its lifecycle.
The Sustainability Potential of 7075 Aluminum
Furthermore, aluminum is infinitely recyclable without any loss in quality. This recyclability makes 7075 aluminum bars a sustainable choice for industries aiming to reduce their environmental impact and move towards circular economies.
Discover Manufacturing With 7075 Aluminum Bars with Zetwerk!
As we conclude this journey into the world of 7075 aluminum bars, it becomes evident why this material has become an indispensable asset to the aerospace and defense industries. Its unmatched strength, low density, corrosion resistance, and machinability have revolutionized manufacturing processes and enabled groundbreaking innovations in these sectors. From aircraft components to rocket parts, this versatile material continues to play a pivotal role in shaping the future of aerospace and defense.
FAQs
The 7075 aluminum bar exhibits excellent heat resistance, making it highly suitable for high-temperature environments such as aerospace and rocketry.
The tensile strength of the 7075 aluminum bar is comparable to many steel alloys, allowing it to replace steel in various applications while offering significant weight savings.
Welding 7075 aluminum bars can be challenging due to their susceptibility to cracking. However, successful welds can be achieved with the right welding techniques and expertise.
The primary difference lies in their shapes. While round bars are cylindrical, flat bars have a rectangular cross-section. Both retain similar mechanical properties and strength.
Absolutely. The alloy’s corrosion resistance makes it well-suited for marine applications, where exposure to saltwater and harsh conditions is common.