Aluminum is one of the most versatile and widely used materials in the manufacturing industry, thanks to its lightweight, excellent strength-to-weight ratio, and corrosion resistance. Among the many aluminum alloys available, 6061 and 7075 are two popular options. Both alloys have unique characteristics that make them suitable for various applications. In this comparison guide of 7075 vs. 6061, we will delve into the differences between aluminum 6061 vs. 7075, their respective strengths, weaknesses, and the industries where they excel.
6061 Vs. 7075 Aluminum
6061 Aluminum:
- 6061 aluminum is an alloy primarily composed of aluminum, magnesium, and silicon.
- It is known for its excellent weldability and formability, making it a favorite in various fabrication processes.
- With a moderate to high strength level, 6061 aluminum is commonly used in structural applications.
- Its corrosion resistance is suitable for outdoor use and marine environments, though it’s not as high as some other alloys.
7075 Aluminum:
- 7075 aluminum is an alloy containing aluminum, zinc, copper, and small amounts of other elements.
- Renowned for its exceptional strength, 7075 aluminum is often used in high-stress applications and aerospace components.
- Despite its strength, 7075 aluminum is not as formable as 6061 and requires careful handling during fabrication.
- It offers excellent corrosion resistance and is often used in critical components for aircraft and defense industries.
6061 Vs. 7075: Applications of 6061 and 7075 Aluminum
6061 Aluminum Applications:
- General Engineering: The versatility and moderate strength of 6061 aluminum make it suitable for various engineering applications, such as bridges and building structures.
- Transportation: It is commonly used in automotive parts, bicycle frames, and marine components due to its corrosion resistance.
- Consumer Electronics: 6061 aluminum is widely used to manufacture laptops, smartphones, and other electronic devices.
- Sporting Goods: Many sporting goods, including baseball bats and bicycle components, are made from 6061 aluminum.
7075 Aluminum Applications:
- Aerospace Industry: Due to its high strength and lightweight properties, 7075 aluminum is the go-to choice for aircraft components, such as wings, fuselage parts, and landing gears.
- Defense Sector: In military applications, 7075 aluminum is used for armor plates, missile components, and firearms due to its exceptional strength.
- High-Performance Sports Equipment: Premium bicycles, rock climbing equipment, and mountaineering gear utilize 7075 aluminum for its durability and reliability.
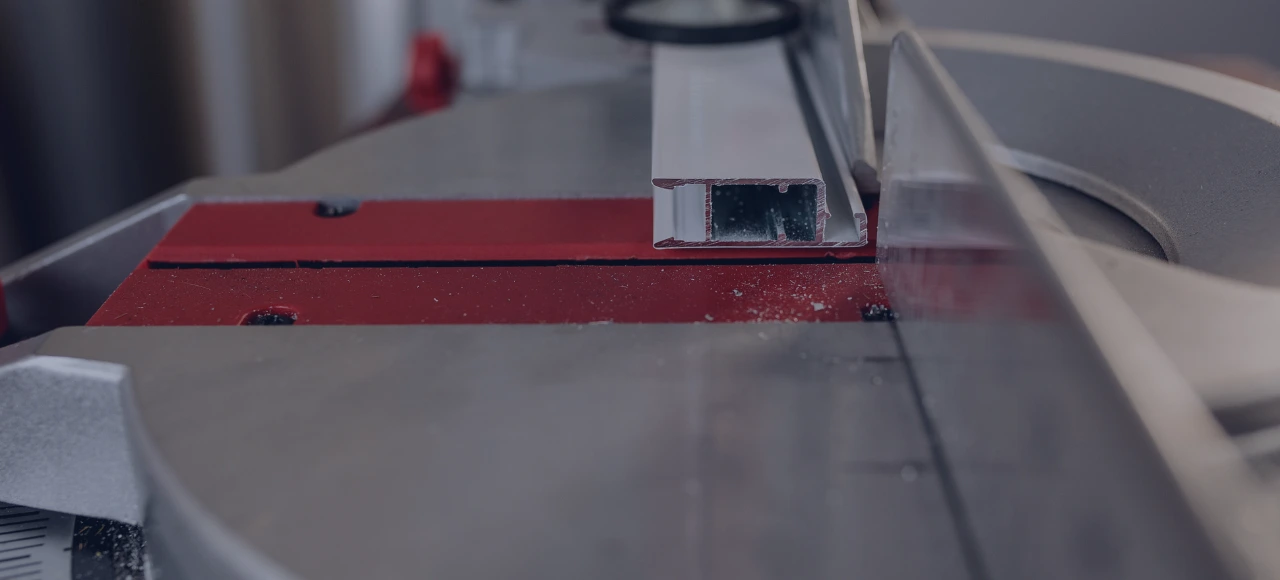
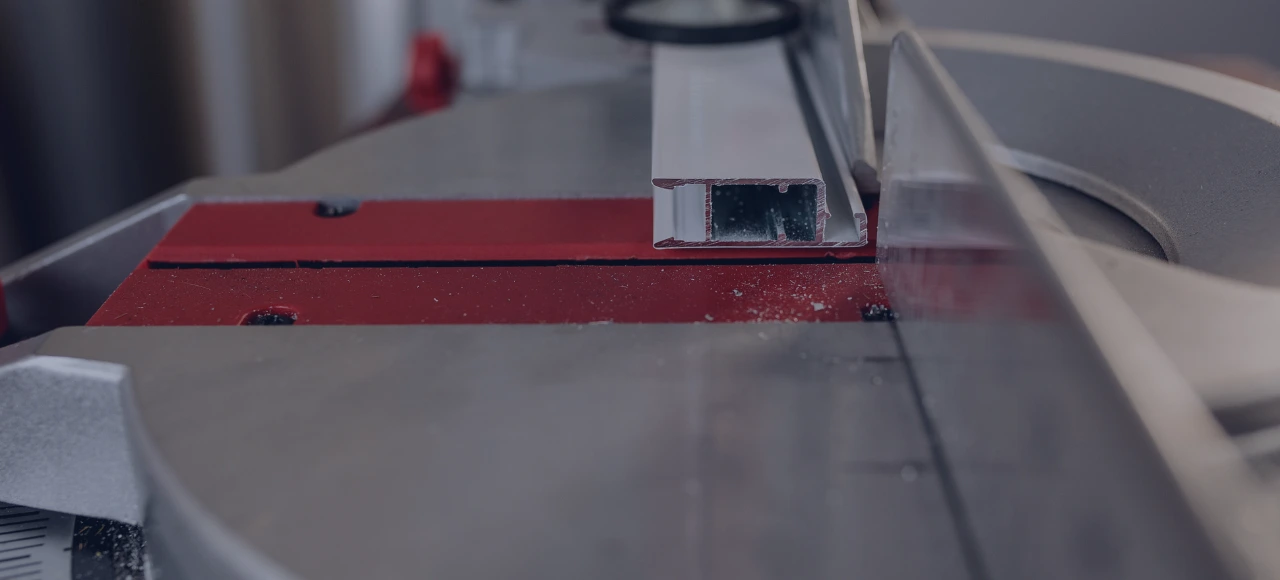
6061 Vs. 7075: Strength and Weight Comparison
In this section, we will comprehensively compare the strength and weight between 7075 and 6061 aluminum alloys.
6061 Aluminum:
- Tensile Strength: 45,000 psi (310 MPa)
- Yield Strength: 40,000 psi (276 MPa)
- Density: 2.7 g/cm³
7075 Aluminum:
- Tensile Strength: 83,000 psi (572 MPa)
- Yield Strength: 73,000 psi (503 MPa)
- Density: 2.81 g/cm³
From the strength and density comparison, it is evident that 7075 aluminum is significantly stronger than 6061. However, this strength comes at the cost of lower formability and higher weight. In applications where strength is critical, 7075 is preferred, while 6061 is chosen when a balance between strength and formability is needed.
6061 Vs. 7075: Machinability
6061 Aluminum:
- 6061 is easily machinable, requiring less power and producing smooth finishes.
- It is ideal for intricate and complex shapes due to its excellent formability.
7075 Aluminum:
- While 7075 aluminum can be machined, it requires more power and specialized equipment.
- Its lower machinability is attributed to its higher strength and hardness.
6061 Vs. 7075: Corrosion Resistance Comparison
Both 6061 and 7075 aluminum offer good corrosion resistance, but the 6061 has a slight edge in this aspect. The addition of magnesium in 6061 enhances its corrosion resistance compared to 7075, making it suitable for applications exposed to harsh environments.
6061 Vs. 7075: Weldability
6061 Aluminum:
6061 offers excellent weldability, allowing for various welding methods such as TIG and MIG welding.
7075 Aluminum:
- 7075 aluminum has poor weldability due to its high zinc content, which can cause cracks during welding.
- Welding 7075 requires special techniques and precautions to prevent defects.
Making the Right Aluminum Choice: 6061 vs. 7075
The choice between 6061 and 7075 aluminum depends on the application’s specific requirements. If high strength and lightweight properties are paramount, 7075 is the superior choice. On the other hand, if formability, weldability, and corrosion resistance are essential, 6061 is the more suitable option.
Zetwerk is a leading manufacturing and supply chain technology company that connects businesses with pre-qualified manufacturing partners. They offer various aluminum extrusions and custom metal fabrication solutions for various industries.
To learn more about aluminum extrusions and our applications, visit Zetwerk’s aluminum extrusions resource page. For all your manufacturing needs, explore our services and knowledge base.




FAQs
7075 aluminum is the preferred choice for aerospace applications due to its high strength and lightweight properties.
Both alloys offer good corrosion resistance, making them suitable for marine environments. However, 6061 performs slightly better in this regard.
6061 aluminum is widely used in industries such as general engineering, transportation, consumer electronics, and sporting goods.
While 7075 aluminum can be welded, it requires special techniques and precautions due to its poor weldability.
6061 aluminum is more formable and easier to work with compared to 7075 aluminum.