The construction supply chain is the process by which materials, equipment, and labor are procured and delivered to a construction site. Construction supply chain issues include delays in delivery, materials shortages, design changes, and quality control problems. These issues can lead to increased costs, schedule delays, and a lower quality of work. Poor communication and coordination between suppliers, contractors, and project managers are common causes of construction supply chain issues.
More transparency in the supply chain and effective supply chain management processes can also lead to problems. Companies should have a supply chain management process that is well-structured, organized, and robust to mitigate these issues. They should also have proactive management, clear communication among all stakeholders, and contingency plans to deal with unexpected problems.
Top Construction Supply Chain Issues
Delays in the supply chain have affected almost every industry since the start of the COVID-19 lockdown in 2020. It continues to plague us today as we recover from the pandemic. In this post, we examine some of the biggest challenges contractors face as work returns to pre-pandemic levels and offer strategies for mitigating:
Material Shortage
In the wake of the pandemic, construction materials that had been readily available before are now hard to find, and if you can find them, they may have longer lead times. As a result, contractors have been forced to use different materials to keep their project budgets and schedules intact. Steps to reduce the impact include:
- Letting suppliers know about the project schedule.
- Ordering durable goods in advance.
- Placing orders with local suppliers whenever possible.
- Paying suppliers on time.





Labor Shortage
The COVID-19 pandemic caused many construction projects to be delayed or stopped in 2020. In 2022, ABC (Associated Builders and Contractors) reported that 1.2 million workers had left the construction industry and were looking for other professions. The construction industry needs help finding skilled workers, according to ABC. The network predicts that the industry needs to employ nearly 600K people by 2023 to meet sustained demand.
Skilled labor is in short supply, and low-skilled workers—such as manual laborers—are the fastest-growing sector of the workforce in manufacturing. This will increase the demand for skilled labor, wages, and costs, encouraging these unskilled workers to specialize over time. Contractors are looking for ways to train employees more efficiently so that those employees have the training and certifications they need when they need them.
Rise In Project Costs
If a construction project is interrupted, it can affect the budget. Materials will likely cost more during disruption periods, making it difficult for contractors to stick with the initial budget. E-Builder, a project management solution used widely in the construction industry, recommends that design teams collaborate with engineers and architects during the planning phase.
It helps only select materials that may be available when it comes time to implement and purchase them. To secure materials, it is essential to maintain positive relationships with suppliers. This may mean finding substitutes to meet budget constraints, ordering materials as soon as possible to meet costs and delivery times, and revising traditional purchasing contracts to include incentive/compensation clauses.
Schedule Delays & Material Lead Time
Contractors needed help keeping to the project schedule due to the long delivery time of materials before the pandemic. Well-established contractors in the Washington area, according to HBW Construction, could continue to order materials knowing that deliveries would be made within the expected timeframe. One of the most common reasons for project delays is the late delivery of materials.
It’s usually a good idea to schedule your milestones to coincide with material deliveries and reschedule some early milestones that typically coincide with material delivery. A sound software system can help reduce project delays by helping contractors track material shipments, inventory levels, fuel surcharges, and automatic re-ordering.
Buckle Your Seatbelt And Get Ready For A Smooth Ride
In the coming years, the construction industry will face several supply chain issues that will likely affect project schedules and budgets. To successfully navigate these realities, consider the following:
- Discover the names, responsibilities, and areas of activity of all stakeholders.
- Look for opportunities to develop skills critical to your organization’s success.
- Think about the worst-case scenarios that could happen and plan for them.
- Work with them to identify and implement alternative plans.
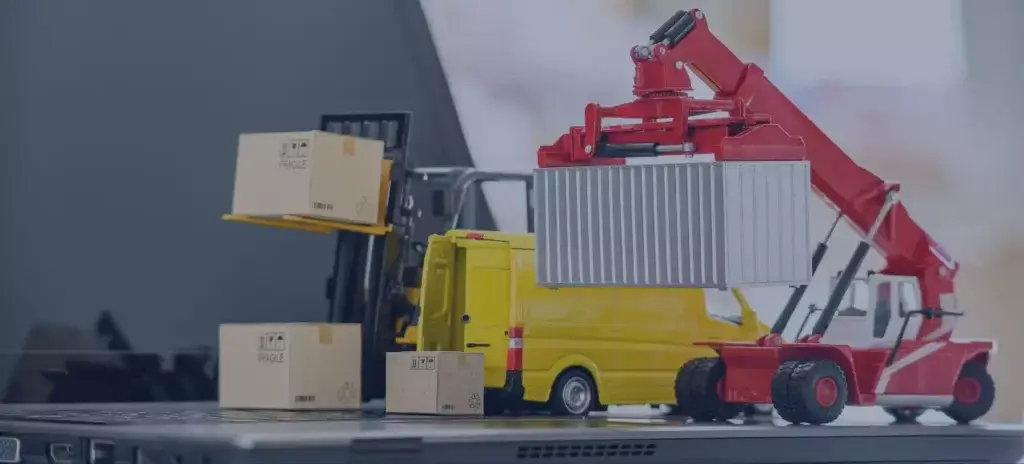
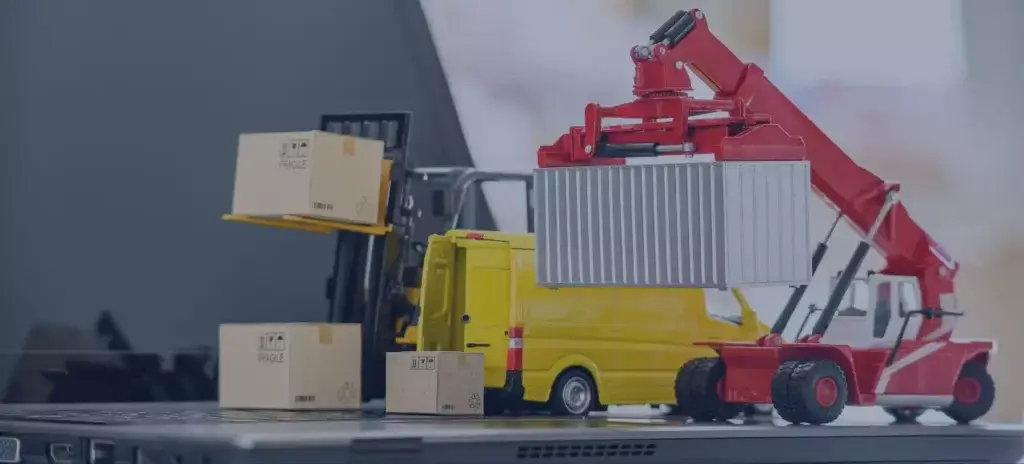
The construction industry has been facing numerous supply chain issues, such as delayed orders, inadequate inventory, and unmet deadlines. To address these issues, companies are increasingly turning to specialized supply chain solutions like Zetwerk.
Zetwerk helps to streamline the entire supply chain process by providing companies with the management service to ensure efficient order processing, inventory management, and timely delivery of construction materials. It also helps reduce manual labor costs by automating mundane tasks such as invoicing and billing. With its integrated capabilities, we also provide insights into the current market trends and suggest recommendations for better inventory management. Know more by contacting us!




