Die casting factories typically operate on a 24/7 basis to meet the demand for parts. The process begins with creating a die, a specialized mold to shape the molten metal. Dies are usually made of steel or another strong, durable material and are precision machined to produce parts with tight tolerances.
Once the die is complete, it is installed into a die casting machine, which consists of a furnace to melt the metal, a plunger or piston to inject the metal into the die, and a cooling system to solidify the metal. The operator loads the die into the machine and sets the parameters for the casting process, such as the injection pressure, casting speed, and cooling rate. The molten metal is injected into the custom die under high pressure, filling the cavities and taking on the shape of the produced part. The metal cools and solidifies in the die, and the finished part is ejected.
After the casting process is complete, the parts are removed from the die and undergo a series of finishing operations, such as deburring, polishing, and painting. The finished parts are then inspected for quality and shipped to customers. Die casting factories are typically highly automated, with robots and computer-controlled equipment performing many of the tasks involved in the production process. The use of automation helps to ensure consistent quality control and efficiency and helps to reduce the risk of errors and accidents.
Best Practices For Die Casting Factory
Here are some best practices that could be followed in a die casting factory:
- Monitor quality: Regularly monitoring the quality of finished parts is essential for ensuring that customers receive products that meet their specifications. This can be done through various, such as visual inspection, dimensional measurement, and metallurgical testing.
- Use advanced technology: Advanced technologies, such as robotics and computer-controlled equipment, can help to improve efficiency and accuracy in the production process. Implementing these technologies can reduce the risk of errors and improve overall quality.
- Control injection pressure: Injection pressure is an important factor in the casting process, as it can affect the dimensions and surface finish of the parts. It is important to monitor and control injection pressure to ensure it is consistent and within the desired range.
- Use high-quality dies: The die’s quality is a major reflection of the quality of the finished parts. High-quality well-maintained dies can ensure consistent, accurate parts with a smooth surface finish.
- Follow safety protocols: Die casting can be hazardous, so it is important to follow proper safety protocols to protect workers. This includes using personal protective equipment, training employees in safety procedures, and regularly inspecting equipment for potential hazards.
- Communicate with customers: Good communication is important for meeting their needs. This includes providing timely updates on the status of orders, addressing any concerns or issues that arise, and seeking feedback to improve the production process continuously.
- Maintain equipment: Maintenance of die casting machines and other equipment is crucial to ensuring consistent quality and productivity. This includes regularly cleaning and lubricating machines and performing regular maintenance and repairs as needed.
Zetwerk’s die casting factories will produce custom parts for your project
In order to produce custom parts, the factories may use various tools and equipment, such as computer-aided design software, prototyping equipment, and specialized production machinery. They may also have a team of engineers and technicians who are skilled in designing and producing custom parts using the die casting process.
Zetwerk Key Strengths:
- Production Capability: Zetwerk can produce large volumes of parts quickly and efficiently, thanks to our advanced machinery and highly skilled team of technicians. This enables Zetwerk to meet the demands of clients requiring high-volume parts orders with short lead times.
- Project Management: Zetwerk is also well-equipped to handle custom projects. The company’s engineering team is skilled in working with clients to understand their specific requirements and designing a custom production process to meet their needs. This could involve creating custom dies, adapting production processes, or using specialized materials. Zetwerk’s approach to custom projects is designed to help clients bring their ideas to life and ensure they receive high-quality parts that meet their specific requirements. Zetwerk’s engineers and technicians are dedicated to working closely with clients throughout the production process to ensure that their needs are met and that their projects are completed on time.
- Faster Lead Time: By leveraging its advanced technology and efficient production processes, Zetwerk can produce parts quickly and deliver them to clients on time. This can be especially important for clients working on tight deadlines or needing to get their products to market quickly.





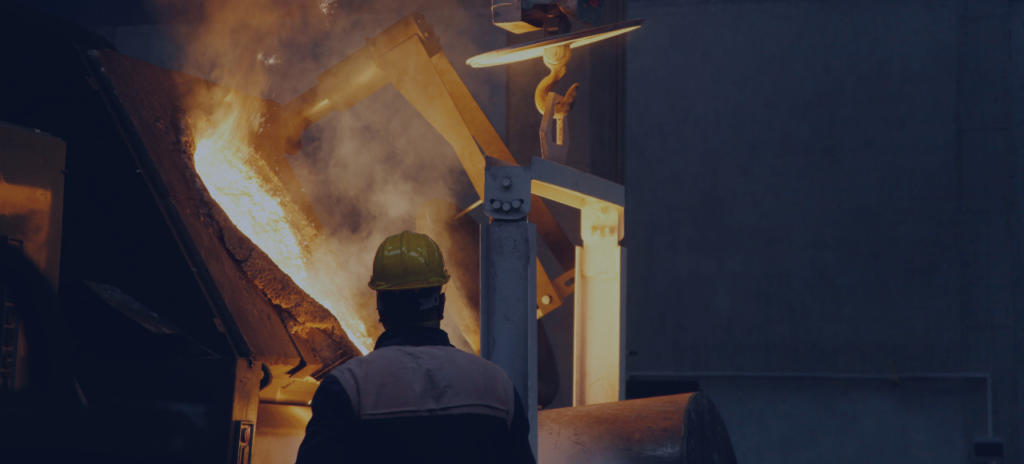
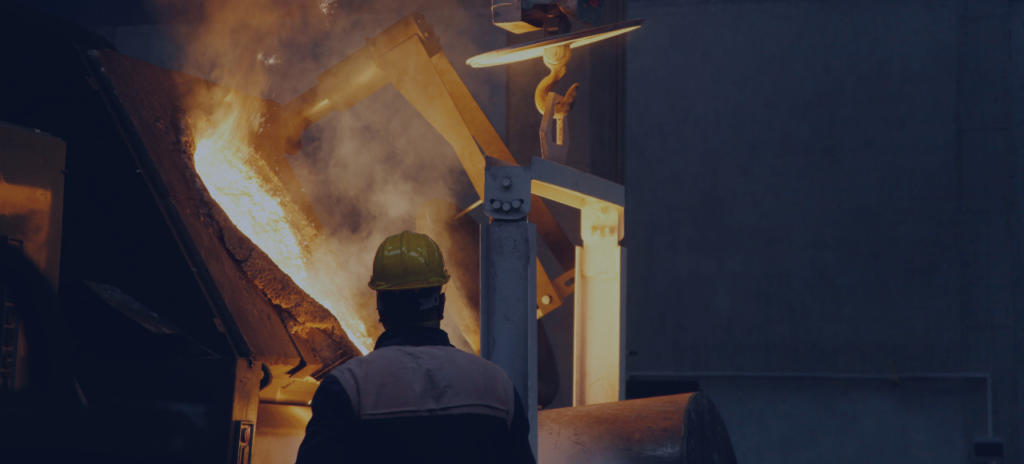
Facts about Die Casting Factory around the globe
Here are some potential facts about die casting factories around the globe:
- Die casting produces a wide range of parts, including car parts, electronic components, and industrial machinery components.
- The use of die casting can help manufacturers reduce prices and improve efficiency by eliminating the need for multiple production steps, such as machining and assembly.
- Die casting is a widely used manufacturing process, with factories in many countries worldwide. The global die casting market at the international level is expected to grow exponentially in the coming decades, driven by increasing demand for lightweight and high-strength parts in various industries.
- Die casting factories use a variety of materials, including aluminum, zinc, brass, copper, and magnesium, to produce parts with different properties and applications.
- Die casting factories often use automation and advanced technology, such as robotics and computer-controlled equipment, to improve efficiency and accuracy in the production process.
- The die casting process is known for producing parts with high dimensional accuracy and a smooth surface finish.
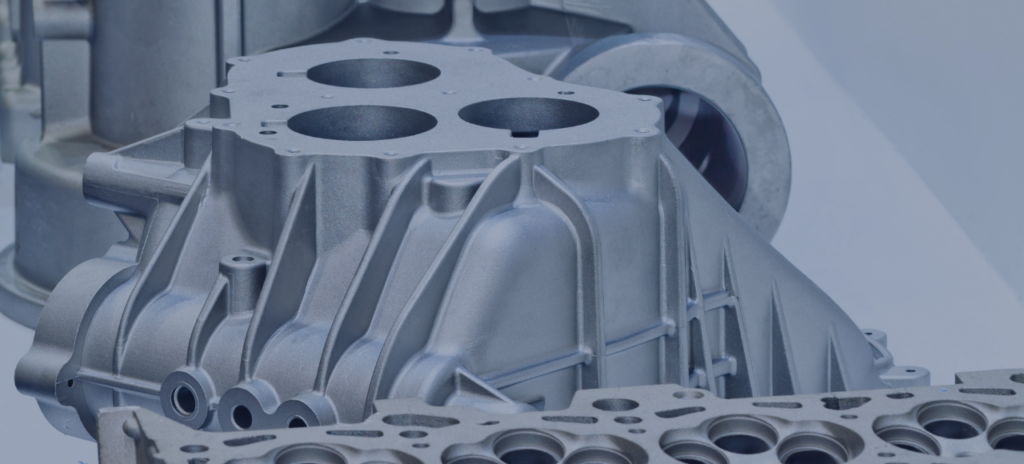
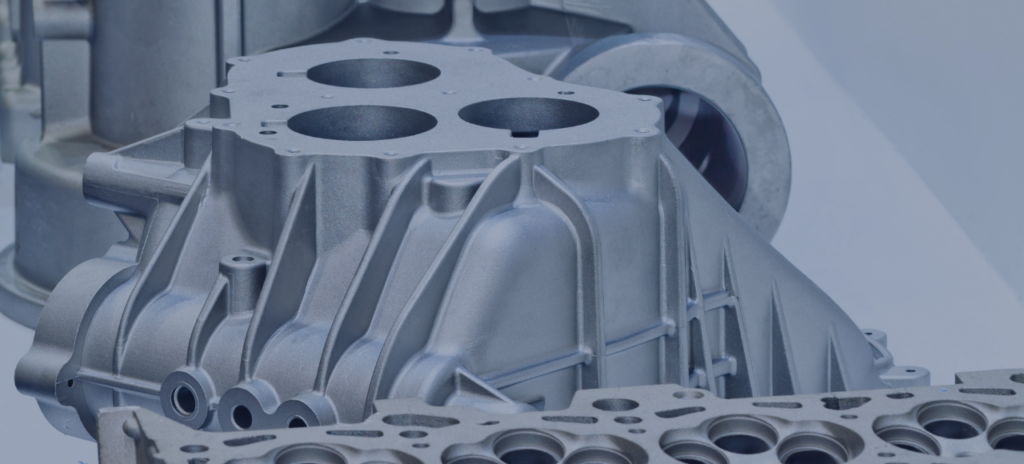