Metal Injection Molding (MIM) has emerged as a critical technology in modern manufacturing processes, known for its ability to produce intricate and high-volume components across various industries. MIM metal injection molding is particularly valuable in the automotive, aerospace, medical, and consumer electronics sectors, where precision and scalability are paramount. But, like all innovative processes, it has its own unique set of challenges.
This article will explore the common metal injection molding problems and present solutions, aligning with Zetwerk’s commitment to precision, quality, and meeting diverse industrial needs.
Challenges in Metal Injection Molding
Material Selection and Handling
- Choosing the right combination of metals and binders is vital in MIM, and any mismatch can lead to compromised product quality. Further, handling the material requires care to prevent contamination.
- Solution: Researching and understanding the product’s specific needs and professional guidance can prevent a material mismatch. Proper storage and handling protocols can minimize contamination risks.
Tooling and Design Complexity
- MIM metal injection molding requires complex tools and designs. Mistakes in tooling design can lead to manufacturing defects, high costs, and delays.
- Solution: Utilizing advanced software for design, coupled with experienced engineers, ensures accurate tooling. Prototyping and iterative testing can further eliminate errors.
Debinding and Sintering
- Debinding and sintering stages in Metal Injection Molding are time-consuming and delicate, with a possibility of distortion and shrinkage.
- Solution: Proper temperature control, expert monitoring, and adapting industry-standard techniques can reduce these risks.
Enhancing the Process Through Technology
Implementing technological advancements like Computer-Aided Design (CAD), 3D printing, and process automation can significantly alleviate the challenges associated with MIM metal injection molding.
Advanced Applications of Metal Injection Molding
Aerospace Industry
- MIM metal injection molding is paving the way for the production of complex aerospace components. Precision, weight reduction, and strength are paramount, and MIM technology can deliver these attributes.
- Challenges: High-precision demands, strength-to-weight ratio optimization, compliance with stringent regulations.
- Solutions: Collaborative engineering, material innovation, stringent quality control, and certification processes.
Medical Industry
- The medical field’s reliance on MIM metal injection molding is growing for producing intricate parts like surgical instruments and implants.
- Challenges: Biocompatibility, sterilization, customization, and adherence to medical standards.
- Solutions: Utilizing biocompatible materials, clean manufacturing environments, specialized design, and collaboration with medical experts.
Automotive Industry
- Metal Injection Molding is revolutionizing automotive manufacturing by enabling mass production of complex parts like gears, levers, and connectors.
- Challenges: Scalability, durability, cost control, and adapting to evolving automotive technologies.
- Solutions: Continuous process optimization, leveraging technology for design and testing, and alignment with automotive industry needs.
Quality Control in MIM Metal Injection Molding
- Maintaining quality in MIM is not just about the final product; it spans every production stage.
- Challenges: Quality inconsistency, high defect rates, and quality assurance costs.
- Solutions: Implementation of Statistical Process Control (SPC), regular quality audits, collaboration with quality control experts, and automation in inspection.
Environmental Considerations
- As businesses are more conscious of their environmental impact, MIM metal injection molding processes must align with sustainability goals.
- Challenges: Waste management, energy consumption, environmental compliance.
- Solutions: Recycling and reusing materials, investing in energy-efficient technologies, compliance with environmental regulations, and certifications.
Future Prospects and Innovations
- The future of MIM metal injection molding looks bright with continuous technological advancements, collaboration between industries, and a strong focus on research and development.
- Challenges: Keeping up with technological trends, investing in research, and building interdisciplinary collaborations.
- Solutions: Fostering innovation, investment in research and development, collaboration with research institutions and industry experts.
Customization Capabilities in MIM Metal Injection Molding
- The ability to customize metal parts to meet specific requirements is one of the essential advantages of MIM metal injection molding.
- Challenges: Balancing customization with cost, and scalability, ensuring specific customer requirements are met.
- Solutions: Implementing advanced design software, prototyping, working closely with clients to understand their needs, and lean manufacturing practices.
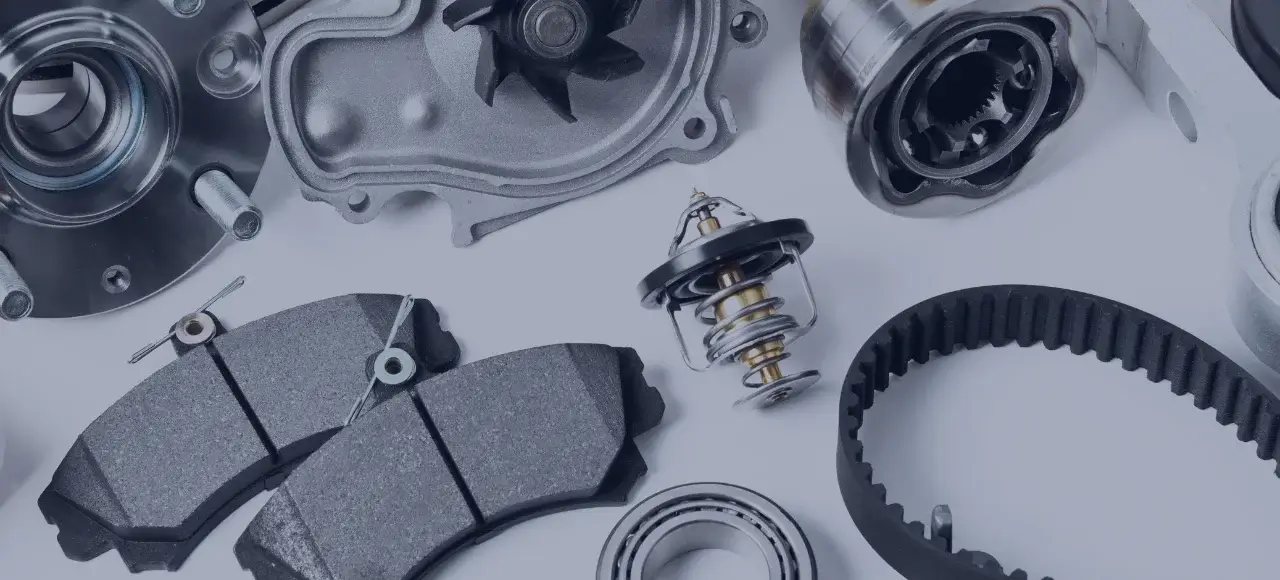
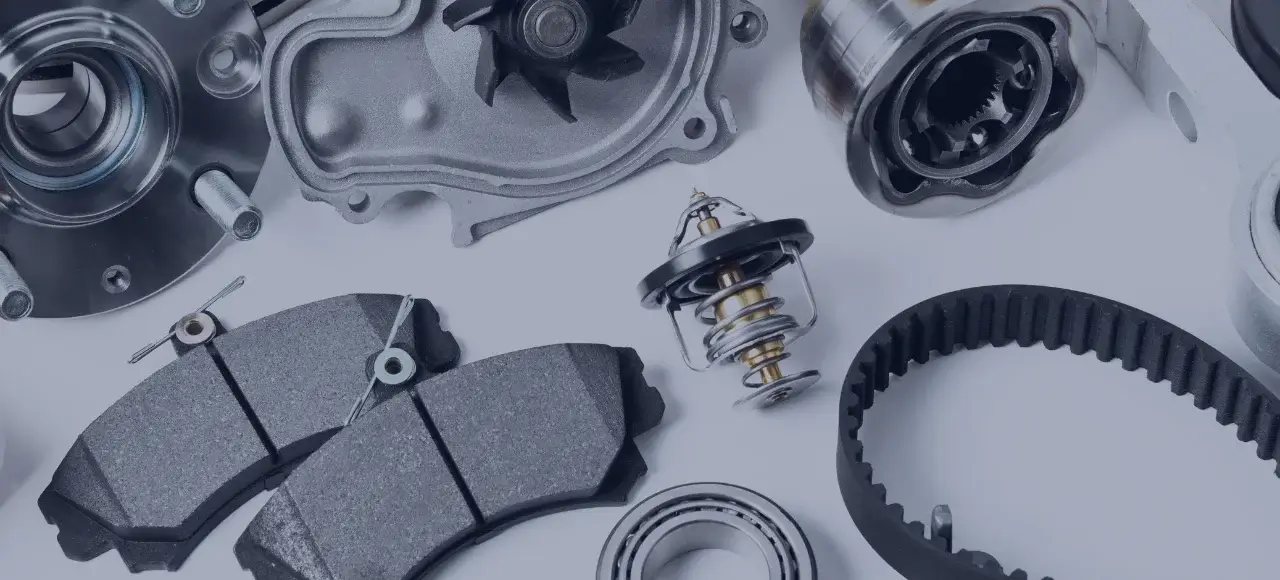
Integration with Other Manufacturing Processes
- The ability to integrate MIM with other manufacturing processes can enhance the efficiency and flexibility of production.
- Challenges: Compatibility issues, optimizing workflow, maintaining quality across different processes.
- Solutions: Thorough planning, cross-disciplinary collaboration, implementing Industry 4.0 principles, and investing in flexible manufacturing systems.
Labor and Skill Requirements
- Operating within the MIM process demands specialized skills and knowledge.
- Challenges: Skill shortages, training requirements, maintaining safety standards.
- Solutions: Investing in employee training, collaboration with educational institutions, and implementing safety protocols.
Market Trends and Economic Factors
- MIM metal injection molding is affected by various economic factors and market trends.
- Challenges: Fluctuating raw material prices, changing regulations, and global economic uncertainties.
- Solutions: Strategic planning, risk management, monitoring global trends, and building flexible and resilient supply chains.
Research and Development in MIM
- Innovation is crucial in keeping MIM at the forefront of manufacturing technology.
- Challenges: Funding research, aligning with industry needs, and protecting intellectual property.
- Solutions: Collaborative research with academia and industry, securing patents, and building a culture of innovation.
Global Supply Chain Considerations
- With the globalization of manufacturing, Metal Injection Molding problems related to supply chain logistics become more prominent.
- Challenges: Transportation costs, customs regulations, global quality standards, fluctuating currency rates.
- Solutions: Building robust global partnerships, implementing efficient logistics management systems, and compliance with international standards.
Summary
The multifaceted nature of MIM metal injection molding brings along various challenges, ranging from technological and quality control to market dynamics and global supply chain complexities.
However, choosing a manufacturing partner who understands the intricacies of MIM is crucial. The deep understanding of Metal Injection Molding problems and solutions, combined with cutting-edge technology and a team of experts, ensures the highest quality results. Zetwerk’s approach to these challenges is rooted in innovation, collaboration, quality, and a profound understanding of the industry.




FAQs
MIM is a process that combines traditional injection molding with powder metallurgy. It allows for high-precision production of complex metal parts, making it vital for aerospace, automotive, and medical industries.
Common challenges include material selection, design complexity, debinding and sintering stages, quality control, environmental considerations, and integration with other processes.
MIM enables customization by allowing intricate designs and various metals and alloys. It can adapt to specific customer needs, delivering tailored solutions in diverse industries.
Technology enhances MIM by providing advanced design tools, automation, process optimization, and quality control methods. It supports innovation, efficiency, and scalability.
Zetwerk offers expertise, innovative technology, and a deep understanding of Metal Injection Molding problems and solutions. Their commitment to quality, precision, and customization makes them an ideal partner for MIM manufacturing.